A Comprehensive Guide to Belt Scales: Components, Working Principles, Types and Applications
Belt scales are workhorses in many industries, continuously monitoring the flow rate of bulk materials on conveyor belts. They play a crucial role in ensuring accurate material transfer, production efficiency, and inventory control. This guide delves into the world of belt scales, exploring their components, working principles, different types, and diverse applications.
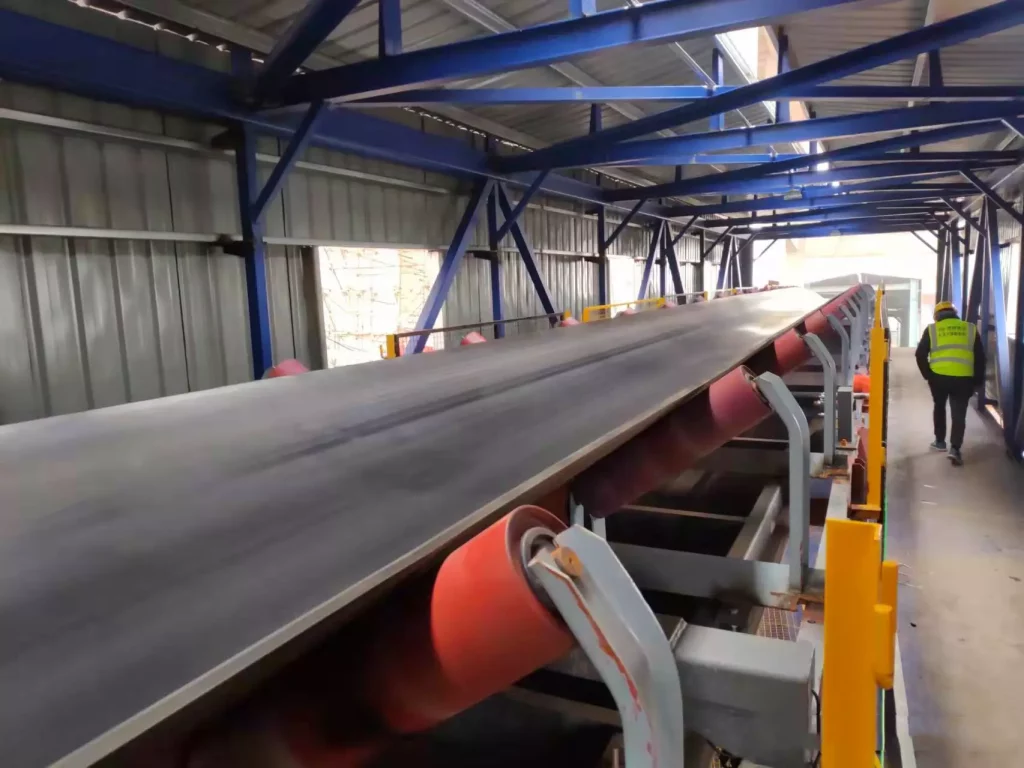
What are the Components of a Belt Scale System?
A belt scale system typically consists of three key components:
- Weigh Frame: This is the heart of the system, housing load cells that measure the weight of material passing over the conveyor belt. The weigh frame can be a roller design, where the belt rides on rollers supported by load cells, or an idler design, where the belt rides on idlers that incorporate load cells.
- Speed Sensor: This component accurately measures the speed of the conveyor belt. Common types include tachometers mounted on the belt pulley shaft or magnetic sensors that detect the passage of metal tags embedded in the belt.
- Integrator: This is the brain of the system. It receives signals from the load cells and speed sensor, calculates the mass flow rate of the material on the belt, and displays the weight data. Integrators can be simple displays or sophisticated units offering data logging, control outputs, and communication capabilities.
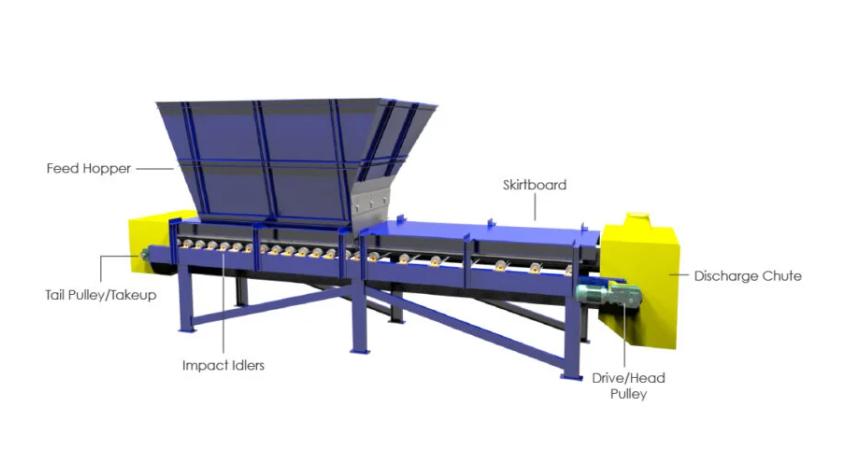
How a Belt Scale Work?
The operation of a belt scale is founded on a precise interplay of mechanical and electronic components, ensuring accurate measurement of material flow rates along a conveyor belt. Let’s delve deeper into the intricacies of its functioning:
- Material Transport: As bulk material travels along the conveyor belt, it traverses over a specialized section known as the weigh frame. This segment is strategically positioned to facilitate accurate weight measurement of the material as it passes through.
- Force Measurement: The weight of the material exerts a downward force onto the load cells embedded within the weight frame. Load cells are precision-engineered sensors designed to detect and quantify the magnitude of this force.
- Conversion to Electrical Signal: Upon sensing the applied force, the load cells swiftly and precisely convert it into an electrical signal. This signal is directly proportional to the weight of the material passing over the weigh frame at any given moment.
- Speed Measurement: Concurrently, a speed sensor, often integrated into the conveyor system, continuously monitors the velocity of the conveyor belt. This speed data is essential for calculating the mass flow rate of the material accurately.
- Integration and Calculation: The electrical signals generated by the load cells, representing the weight of the material, and the speed sensor data are transmitted to a sophisticated electronic integrator unit. Within the integrator, these signals are meticulously analyzed and processed.
- Mass Flow Rate Determination: Leveraging the weight and speed data, the integrator employs advanced algorithms to calculate the mass flow rate of the material. This calculation involves multiplying the weight of the material by the conveyor belt’s velocity, yielding a precise measurement of the material flow rate in terms of weight per unit time.
- Data Display and Transmission: Finally, the integrator presents the calculated mass flow rate in a user-friendly format, typically on a digital display. Moreover, this data can be transmitted to external systems for further analysis, integration with plant control systems, or recording for regulatory compliance and quality assurance purposes.
In essence, the operation of a belt scale encompasses a meticulously orchestrated process, combining mechanical precision with electronic sophistication to deliver accurate and reliable measurement of material flow rates in industrial settings.
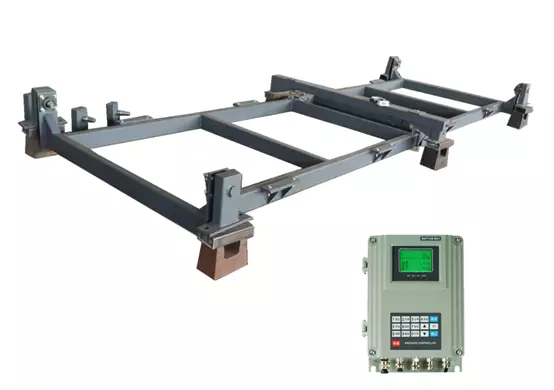
What are the Main Types of Belt Scales?
Belt scales come in a variety of configurations, each catering to specific needs and offering distinct advantages. Here’s a closer look at the main types of belt scales:
- Weigh Roller Belt Scales: These are the most common type, offering a good balance of accuracy, versatility, and affordability. They feature rollers supported by load cells. The belt rides on these rollers, and the load cells measure the weight exerted by the material on the belt. Weigh roller scales are suitable for a wide range of materials, from light and fluffy powders to heavy and abrasive aggregates. They come in various capacities and can be easily integrated into existing conveyor structures.
- Weigh Bridge Belt Scales: These robust scales are designed for heavy-duty applications involving high capacities. They utilize a rigid bridge structure supported by multiple load cells. The conveyor belt passes over this bridge, and the load cells capture the weight of the material. Weigh bridge scales offer exceptional accuracy and stability even under heavy loads. They are ideal for industries like mining and quarrying where large volumes of bulk materials like coal or ore need to be weighed precisely. However, their larger footprint and higher cost compared to weigh roller scales make them less suitable for space-constrained applications.
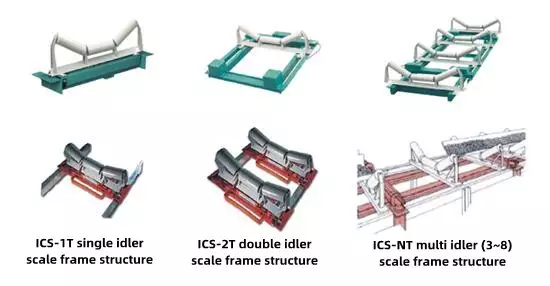
- In-Line Belt Scales: Perfect for retrofitting existing conveyor systems or where space is a premium, in-line belt scales offer a compact and cost-effective solution. These scales integrate directly into the conveyor structure, typically replacing a section of the existing conveyor belt with a weighbridge section supported by load cells. This minimizes space requirements while maintaining good accuracy. However, in-line scales may have lower capacity limitations compared to weigh roller or weighbridge designs.
- Single Idler Belt Scales: These are a simple and economical option for measuring flow rates of lower-value materials on shorter conveyor belts. They utilize a single weigh idler, a roller equipped with load cells, integrated into the conveyor frame. The belt rides on this weigh idler, and the load cell measures the weight. While less expensive than other types, single idler scales offer lower accuracy due to the limited weighing area. They are best suited for applications where a general idea of material flow is sufficient.
- Multi-Idler Belt Scales: Building upon the concept of single-idler scales, multi-idler belt scales incorporate multiple weigh idlers along the conveyor belt. This increases the weight span and improves the accuracy of weight measurement compared to single-idler designs. They are a good compromise between cost and accuracy for applications requiring more precise flow rate data. Common configurations include dual idler, triple idler, and quad idler belt scales, with each additional weigh idler further enhancing accuracy.
- Catenary Belt Scales: These specialized scales are designed for use on conveyors with significant dips or curves where traditional belt scale designs might not be suitable. They utilize a section of the conveyor belt that operates in a catenary curve (a hanging U-shape) between two weigh points. The weight of the material creates a tension difference in the belt, which is measured by the load cells. Catenary belt scales are particularly useful in applications like mobile crushing plants where the conveyor has a non-linear path.
What’s the Application of Belt Scales?

Belt scales transcend numerous industries, acting as silent sentinels ensuring accurate material flow measurement and efficient operations. Let’s delve deeper into their diverse applications across various sectors:
- Mining and Quarrying: In the rugged world of mines and quarries, belt scales are essential for:
- Production Monitoring: They continuously monitor the extraction and transportation of coal, ore, limestone, and other bulk materials. This data is crucial for optimizing production processes, ensuring efficient use of resources, and meeting quotas.
- Inventory Control: Belt scales enable accurate tracking of stockpiles, preventing over or under-excavation. This helps maintain a consistent flow of materials to processing plants and avoids costly delays.
- Loading and Billing: When trucks are loaded with extracted materials, belt scales provide precise weight measurements. This ensures fair billing practices and eliminates discrepancies between miners and buyers.
- Food Processing: Within the fast-paced environment of food production lines, belt scales play a vital role in:
- Ingredient Dosing: Accurate control of ingredients like flour, sugar, and grains is essential for consistent product quality. Belt scales ensure precise ingredient measurement, safeguarding recipe integrity and final product taste.
- Production Line Efficiency: By monitoring the flow of raw materials and finished products, belt scales help optimize production line speed and prevent bottlenecks. This translates to increased output and reduced production costs.
- Inventory Management: Tracking the flow of ingredients and finished goods allows for efficient inventory control. This minimizes waste, avoids stockouts, and ensures a smooth flow of materials throughout the production process.
- Chemical Processing: In the intricate world of chemical processing, belt scales guarantee:
- Accurate Material Blending: Precise measurement of various powders, granules, and chemicals is essential for creating homogenous mixtures. Belt scales ensure accurate blending ratios, maintaining product consistency and quality.
- Process Control: Monitoring the flow of materials throughout the chemical process allows for real-time adjustments and optimization. This helps maintain efficient production and ensures adherence to safety protocols.
- Inventory Tracking: Belt scales enable meticulous tracking of chemical stockpiles, preventing overstocking or understocking of critical components. This optimizes storage space utilization and ensures timely replenishment of materials.
- Construction: The world of construction relies on belt scales for:
- Aggregate Measurement: Accurate measurement of sand, gravel, and crushed rock is vital for efficient concrete production and asphalt mixing. Belt scales ensure precise material quantities, leading to structurally sound construction projects.
- Inventory Control: Tracking stockpiles of construction materials like sand, gravel, and cement allows for better inventory management. This minimizes waste, prevents project delays, and optimizes material costs.
- Load Verification: When trucks deliver construction materials to the site, belt scales provide accurate weight verification. This ensures contractors receive the correct quantities and avoids billing disputes.
- Waste Management: Belt scales play a crucial role in:
- Waste Stream Monitoring: They track the flow of waste materials in recycling facilities and waste disposal sites. This data is essential for optimizing waste processing methods and ensuring efficient waste management.
- Resource Recovery: In recycling plants, belt scales help monitor the flow of recyclable materials like paper, plastic, and metals. This accurate measurement allows for efficient sorting and processing, maximizing resource recovery efforts.
- Emissions Monitoring: In some cases, belt scales can be integrated with dust collection systems to monitor the amount of dust generated during material handling. This helps ensure compliance with environmental regulations.
By understanding these diverse applications, it’s evident that belt scales are not merely measuring devices; they are silent partners in ensuring efficient operations across numerous industries. Their ability to provide accurate and reliable data empowers informed decision-making, optimizes resource utilization, and ultimately contributes to a smoother, more efficient flow of materials in today’s dynamic world.
Summary
Belt scales are versatile and reliable tools for continuous material flow measurement on conveyor belts. Understanding their components, working principles, different types, and extensive applications empowers you to select the most suitable belt scale for your specific needs. From ensuring production efficiency to optimizing inventory control, belt scales play a vital role in various industries, keeping operations running smoothly and efficiently.