A Guide to Installing, Calibrating, and Mastering Your Batching Scale
The batching process of the batching scale is the key link. This guide will answer your questions: The ingredient scale has arrived, and what are the installation requirements? How to increase the weighing accuracy? How to establish a weighing ingredient model? Batching is a process of accurately weighing different kinds of raw materials according to the requirements of the formula by using a special batching device. The quality of the batching controller and the structural design of the batching scale directly affect the accuracy of the batching results. When using an electronic batching scale, people often use batching accuracy to evaluate the performance of batching scale. The weighing accuracy is the approximate degree between the weighing result and the true value, that is, the reflection of the weighing system error and the random error. Most enterprises use microcomputer control in the batching process, which can automatically compensate for the batching error and ensure batching accuracy. At the same time, through the microcomputer keyboard and display, it is convenient to conduct man-machine dialogue, complete parameter settings, check and modify process settings, monitor the batching process, and give an alarm in case of any fault. The company’s unique technology uses single-chip technology to call the management program, through the established model to achieve the automatic control of the symmetric weight batching system. It can reduce the consumption of raw materials, improve product quality, and realize the scientific management of the production process.
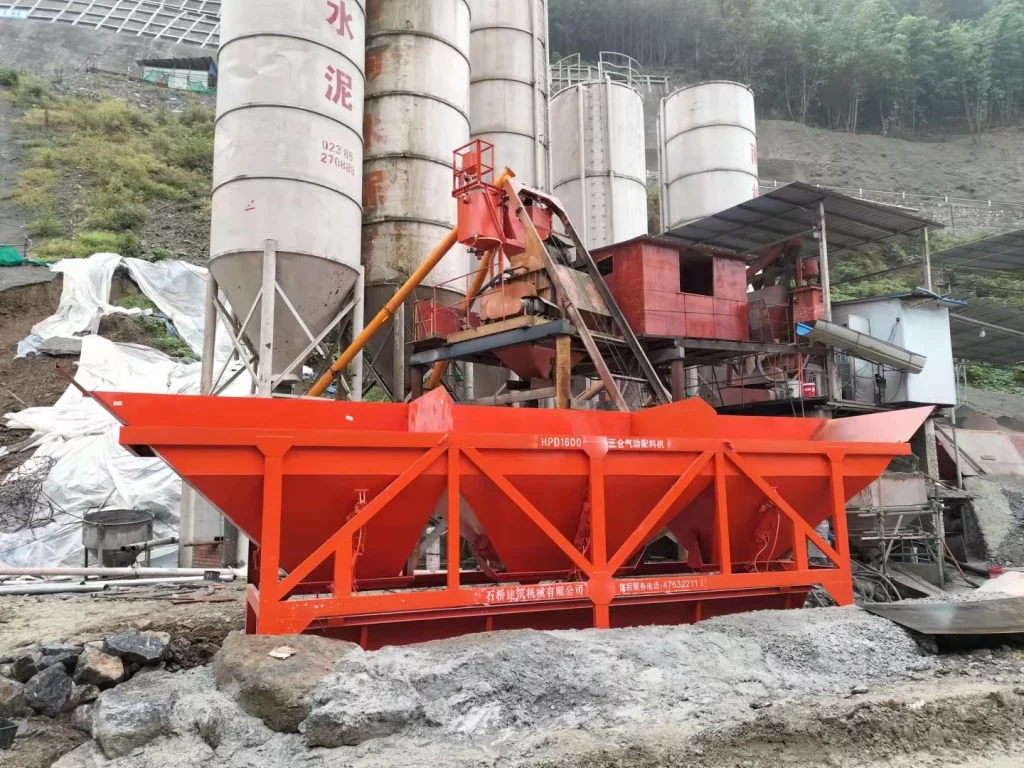
Process Requirements of Batching Scale in Batching System
1. Process requirements
To ensure good batching effect, the general requirements for batching device during design and use are:
- It has good stability and can weigh weight quickly and accurately
- On the premise of ensuring batching accuracy, it should have the characteristics of simple structure, reliable use, easy maintenance, etc.
- With strong adaptability, it can not only adapt to the changes of multiple varieties and proportions but also adapt to various process forms and environmental requirements.
2. Measurement performance analysis of batching scale
In industry, batching scales are widely used weighing instruments. Practice shows that it is necessary to meet not only the basic performance requirements of the weighing apparatus but also the requirements of its production process. Measurement performance can be divided into static performance and dynamic performance.
Static metering performance refers to the metering performance of the electronic batching scale in the nonautomatic weighing state, which is essentially the metering performance of the batching scale itself. When the static metering performance of the batching scale is in the nonautomatic weighing state, it, like all nonautomatic weighing, requires basic metering performance, such as correctness, sensitivity, stability, repeatability, etc. However, there are often many differences in the specific description of the above performance characteristics for electronic batching scales that use weighing sensors to achieve automatic weighing. The accuracy of the weighing device is an accurate and reliable feature of the weighing system in the process of force transmission and conversion. The electronic batching scale, refers to the accuracy and reliability of the electromechanical conversion of the weighing sensor and the weighing result processing. The correctness of the weighing result is expressed by the correctness, which is the size of the system error. The correctness of the batching scale is the integration of the system error of the weighing sensor and the measuring display instrument.
Momentum property refers to a kind of momentum property displayed in the automatic weighing process, that is, the momentum property of the electronic batching scale and its auxiliary equipment under the working state. In the working state, the most important thing about the electronic batching scale is the metering performance of the automatic weighing process. However, the basic performance of the electronic batching scale itself often has different effects on the metering performance, and its manifestations are also different. The dynamic metering performance of the electronic batching scale is mainly reflected in the batching accuracy. The accurate material level reflects the characteristics of the electronic material level scale and its auxiliary equipment, such as accuracy, sensitivity, stability and reliability. Material precision is expressed by material precision. This refers to the difference between the actual mass value of materials weighed in the scale bucket and the theoretical mass value of materials weighed in the batching system. The difference between the two values is the composition error in production practice. The component error reflects the sum of systematic error and random error produced by the component system in operation. In the automatic weighing process, the weighing accuracy of the electronic weighing scale is mainly reflected in the stability of material supply, the accuracy of one weighing, the correctness of cumulative weighing, and the reliability of weighing action. The stability of material supply is the premise of realizing weighing accuracy and the key to the dynamic measurement process. The feeding characteristics are as follows: multiple materials are fed successively through the corresponding feeders, the operation and completion of the feeding process of each feeder is controlled by the computer, and the feeding value of each feeder is continuously accumulated with the change of the feeding amount. The feeding weighing process is a continuous feeding process in stages. The static results show that the “empty column” generated by the complex dynamic process accumulated many times is an important part of the feeding error, and the implementation of fast and slow feeding procedures is the basic means to reduce or eliminate such random errors.
The correctness of the accumulated weighing reflects the comprehensive performance of the measuring display instrument. This accumulation can be the weighing result of a material in different batches; the Accumulation of weighing the quality of different materials in the same batch; Or the accumulation of weighing error and batching errors. The accuracy of accumulation is shown not only in the accuracy, sensitivity, and stability of the meter itself but also in the coordination between the meter and the sensor. This coordination relationship shows that the weighing quality signal can correctly display the results and eliminate various external interference (such as mechanical vibration, power fluctuation, external electromagnetic field, ambient temperature, etc.). The reliability of the weighing action reflects the rationality of the whole batching system structure and process, the correctness of the manufacturing device, and the coordination of the weighing action. The batching system consists of a set of mechanical and electrical equipment. The structure and working mode of the feeder, the structure and working capacity of the scale, the structure of the control mechanism of the bottom gate, the self-locking mechanism, and the interlock mechanism of the unloading, weighing, and unloading links must be considered in the design. The assembly quality of various mechanical devices and the correct installation of scales and weighing sensors are the keys to ensuring the normal operation of the batching system. The feeder can realize fast and slow secondary feeding, adjust the feeding speed, ensure the weighing time, and orderly control the batching process, which is an important means to improve batching accuracy.
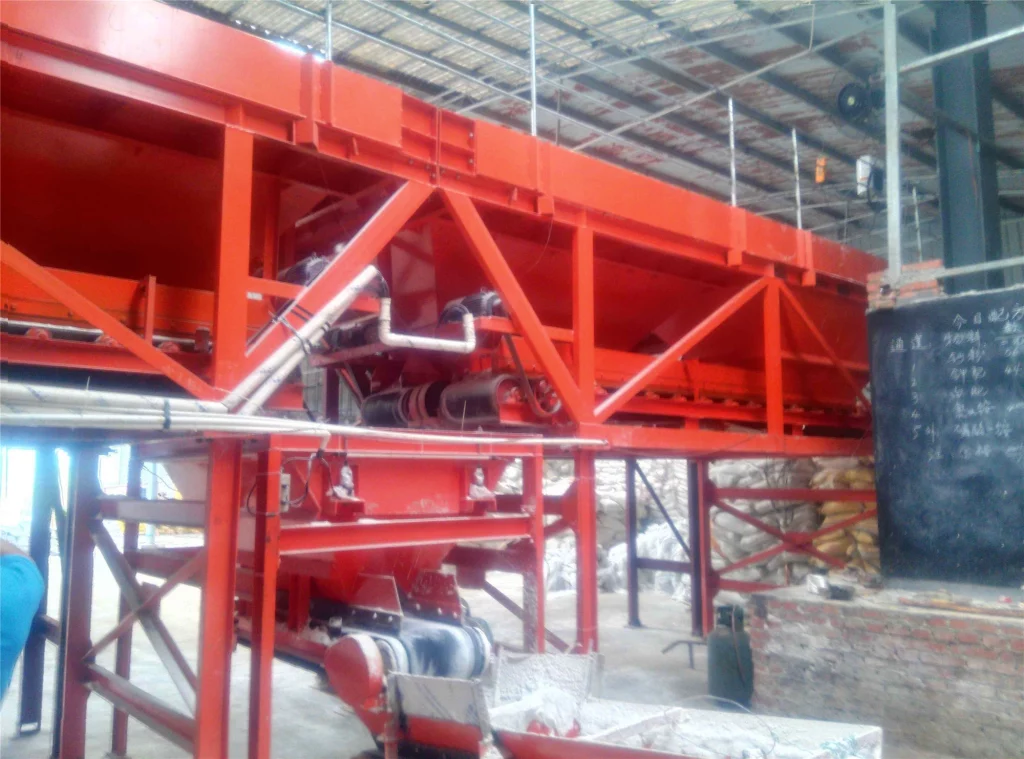
Basic Idea and Model Establishment of Batching Scale Produced By Chongqing Bincheng Electromechanical Technology Co., Ltd. in Batching System
1. Basic idea of improving the accuracy of batching system
In order to improve production efficiency and weighing accuracy, fast and slow scales shall be set. The discharge flow of fast weighing silo is large, while that of slow weighing silo is small. In order to compensate zero drift of the sensor and preamplifier, it is necessary to track the zero of the electronic scale. When weighing ingredients, the actual weighing value often deviates from the required target value. When the positive deviation is greater than a certain value, the supersymmetry is generated. Therefore, during unloading, it is necessary to reduce the amount of material to limit the actual ratio error within the allowable range. When the negative deviation is greater than a certain value, the system will continue to weigh to make up for the shortage. The linear error tracking method is adopted to automatically correct the advance of the next weighing to improve the accuracy of the next weighing.
Because the mixing and discharging time is relatively long, in order to further improve the productivity, the next weighing will start when the mixer enters the mixer. Different kinds of materials are stored in silos and scales, which is easy to cause caking and material retention. Therefore, it is necessary to monitor the flow of materials prone to caking. When the flow is insufficient, arch breaking and shaking will occur, and an alarm will be given at the same time.
2. Establishment of weighing model
(1) Incremental weighing model
The weighing process refers to the continuous feeding process in the weighing bucket. When the weighing value of various materials is equal to the closed weighing value, the feeding is stopped. After a period of delay, after all the weighing values enter the weighing bucket, the actual weighing value is measured, and the weighing error is calculated at the same time, so that the next weighing can be automatically corrected.
(2) Cumulative weighing model
Since different materials share the same scale bucket, at the end of each material weighing, the target value and the closing value for continuous weighing shall be corrected according to the weighing value and closing value of the next material, and the actual weighing value and weighing error of each material shall be calculated.
A certain feed is made by mixing 8 kinds of materials. According to the process requirements, the first feed is prepared first, and then the first feed is stopped. Then add the second material… until the last one. After the batching is completed, the computer will detect the mixer, and after receiving the feeding signal, it will instruct the solenoid valve and conveyor to send the materials to the mixer. At this time, the corresponding indicator on the simulation screen will be on, and a batching cycle will end. The computer repeats the above workflow. During batching, the computer can automatically compensate several other materials in proportion to ensure that the ratio remains unchanged because the unexpected conditions of some materials exceed the specified range.
(3) Reduced discharge weighing model
After weighing the materials, first calculate the closing value of the reduced unloading of various materials, and then open the weighing hopper in a certain time sequence for unloading. When the weight of the materials left in the weighing hopper is equal to the closing value, stop unloading, measure the actual unloading value and the unloading weighing error, and deal with them respectively according to the error range. When weighing thunder, a material has an overweight scale When unloading, it is unloaded in the way of weight reduction, so that a part of the material stays in the scale, limiting the actual unloading amount to the allowable range of error, which is called overbalance processing. The materials left in the weighing bucket are used as the preweighing for the next measurement. Among them, the incremental weighing module and the decrement weighing module are respectively applicable to the batching system of one bin and one scale, and the cumulative weighing module is applicable to the batching system of multiple bins and one scale.
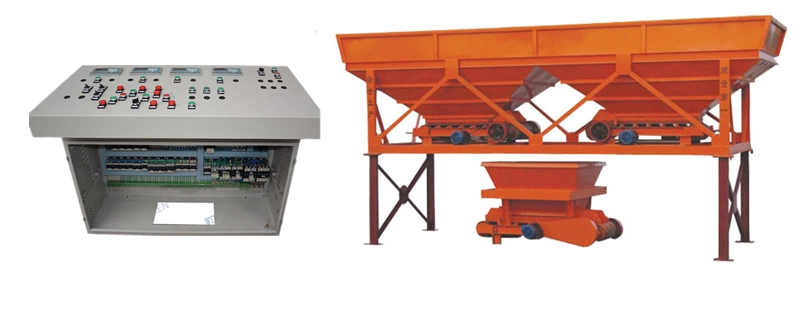
Other Measures to Improve the Weighing Accuracy and Reliability of Batching Scale
1. Variable speed weighing method
Reducing the flow rate of materials is one of the effective methods to improve the weighing accuracy, but it will prolong the weighing time of the system and reduce the weighing efficiency. Therefore, the method of variable speed weighing can not only improve production efficiency but also improve weighing accuracy. The variable speed weighing method is to adopt the high-speed feeding method at the beginning of the feeder. When the material in the feeder reaches a certain value, the equipment will turn to the low-speed feeding method.
2. Dynamic lead tracking
After each weighing, compare the measured value of the material weight in the weighing bucket with the required target value, and calculate the error to compensate for the counterweight value generated during the next weighing. There are many factors that affect the weighing accuracy, which are directly related to the structure of the weighing device, the level of material, the material fluidity, the pressure change of the pneumatic door closing device, and the fatigue degree of the electromechanical equipment. However, if the above factors change slowly, the lead tracking method is still the most effective.
3. The sampling frequency is an integral multiple of the power frequency
Each time of sampling, keep the synchronous relationship with the power frequency voltage, so that the power frequency interference size is fixed, and take this as the zero point of weighing, which can effectively eliminate the power frequency interference. If the preamplifier and A/D conversion board are powered separately, the precision-regulated power supply can eliminate power frequency interference better. But consider the cost-performance ratio.
4. Multi power supply
The digital interface circuit can share a group of DC power supply, and the preamplifier and A/D conversion board can be powered separately, which can avoid mutual influence caused by the fluctuation of power load.
5. A/D conversion function
Make full use of the voltage range of A/D conversion, increase the voltage magnification of the preamplifier as much as possible, and make the analog voltage be converted as large as possible, to reduce the relative error of A/D conversion.
6. Check the weighing value several times
When the weighing value is greater than or equal to the door closing value, the value shall be verified repeatedly. If the results are the same for three consecutive times, judge whether the weighing is effective, to avoid interference due to errors.
7. Power off protection measures
When the power grid is cut off, the computer will input the main parameters into the disk. After the phone is connected, the computer will automatically execute the program according to the characteristics of the parameters.
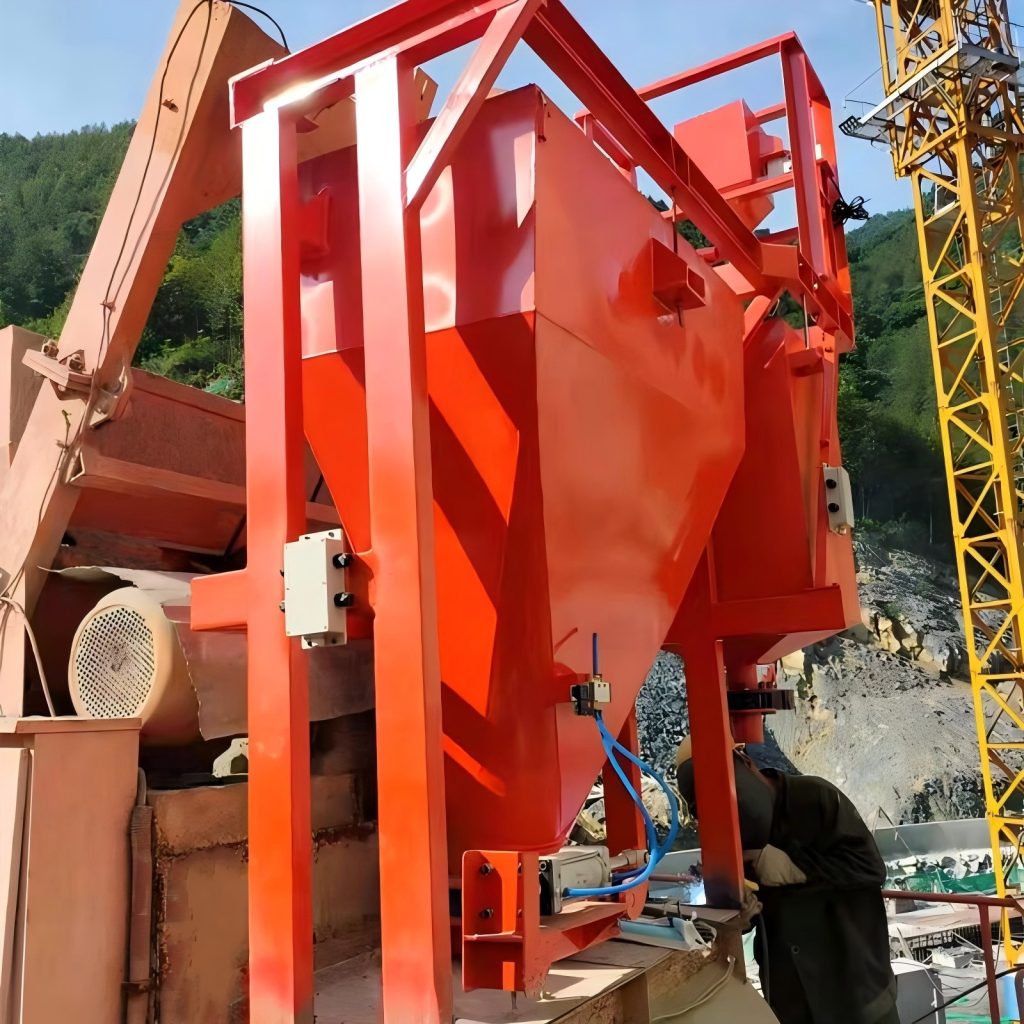
Concluding remarks
The weighing control model is established by using microcomputer and single chip microcomputer technology to realize the automatic compensation of weighing error, ensure the weighing accuracy, monitor the weighing process, and give an alarm in case of failure. The control of a symmetrical reconfiguration system is automatically completed by the model establishment. Precision control methods such as automatic compensation, advance tracking, zero point tracking, multiple vibrations feeding successive approximation, and super and less weighing processing are adopted to achieve high-precision control, enhance the adaptability of the system to the changing industrial site, and improve the reliability of the system.