Batching Scales: Boosting Efficiency and Quality in the Food Industry
Precision, efficiency, and quality are essential in today’s fast-paced and fiercely competitive food industry. To meet these demands, food manufacturers use a wide range of specialized equipment, including batching scales. Bincen, a supplier of batching scales, will discuss the key applications of these scales in the food industry, as well as the numerous benefits they provide, and the specific requirements that these scales must meet in order to deliver optimal performance. Understanding the significance of batching scales allows food manufacturers to make informed decisions about their equipment investments and improve their operations.
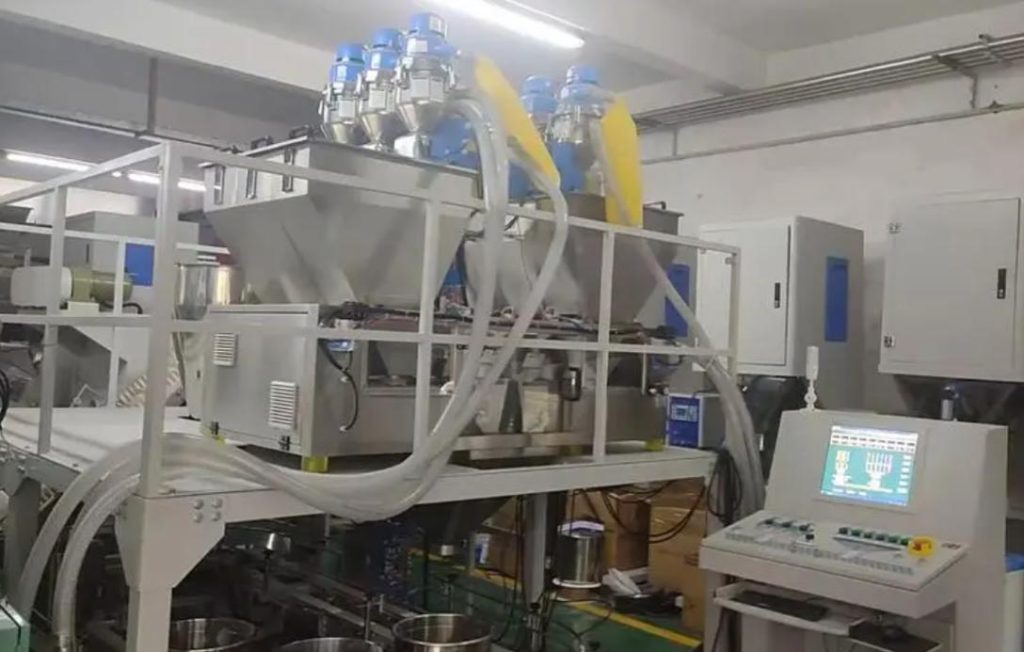
Key Applications of Batching Scales in the Food Industry
Fresh Produce Distribution | Accurate portioning | Batching scales ensure that each portion of produce, such as tomatoes, meets precise weight requirements, minimizing customer complaints and reducing waste. |
Reduced labor costs | Automated weighing systems streamline the packaging process, decreasing the need for manual labor. | |
Automated Production Lines | Increased throughput | Multi-head weighers, a type of batching scale, can simultaneously weigh multiple items, significantly boosting production rates. |
Improved consistency | By integrating with computer control systems, these scales ensure that each product meets exact weight specifications. | |
Quality Control | Product uniformity | Automatic checkweighers continuously monitor product weight, identifying any deviations from set standards and preventing underfilled or overfilled packages. |
Regulatory compliance | These scales help food manufacturers comply with strict quality and safety regulations. | |
Sorting and Distribution | Efficient sorting | Intelligent sorting scales can automatically identify different types of produce and weigh them accurately, streamlining the sorting process. |
Inventory management | Integrated with inventory management systems, these scales provide real-time data on stock levels. | |
Diverse Product Handling | Versatility | Batching scales can accommodate a wide range of products, from delicate items to heavy bulk materials. |
Specialized features | Many scales offer features like waterproofing and shatterproof construction to suit specific product requirements. | |
Data Management and Analysis | Traceability | Batching scales can record detailed weighing data, facilitating traceability and compliance with food safety regulations. |
Process optimization | By analyzing weighing data, manufacturers can identify trends and optimize production processes. |
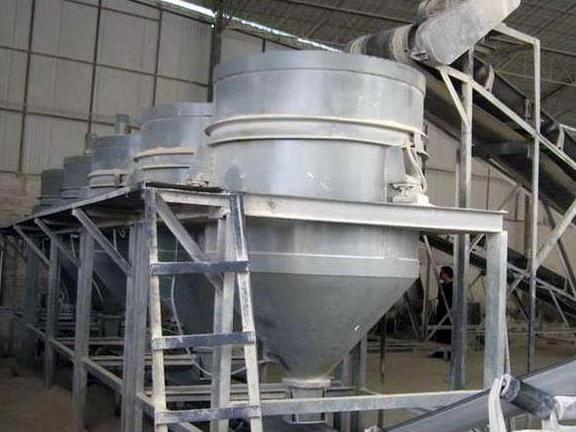
Benefits of Using Batching Scales in the Food Industry
Batching scales, precision instruments designed to weigh large amounts of material, provide significant benefits to food manufacturers. By automating and refining the weighing process, these scales help to improve efficiency, product quality, waste reduction, traceability, and regulatory compliance.
1. Enhanced Efficiency:
- Reduced labor costs: Automated weighing systems significantly reduce the need for manual labor, leading to lower labor costs and increased productivity.
- Increased throughput: Batching scales can handle large volumes of materials quickly and accurately, boosting production rates and meeting higher demand.
- Streamlined operations: By integrating with other production equipment, batching scales can streamline the entire manufacturing process, minimizing bottlenecks and delays.
2. Improved Product Quality:
- Consistent portioning: Precise weighing ensures that each product meets exact weight specifications, preventing underfilling or overfilling and maintaining product quality.
- Reduced waste: Accurate portioning minimizes the use of excess materials, reducing waste and improving profitability.
- Enhanced customer satisfaction: Consistent product quality leads to satisfied customers and a stronger brand reputation.
3. Reduced Waste:
- Minimized overfilling: Batching scales prevent overfilling of products, reducing material waste and costs.
- Optimized inventory management: Accurate weighing data helps food manufacturers maintain optimal inventory levels, preventing stockouts or excessive stockpiles.
- Reduced packaging costs: By minimizing waste, batching scales can contribute to lower packaging costs.
4. Enhanced Traceability:
- Detailed data recording: Batching scales can record detailed weighing data, including time, date, and product information.
- Product recall support: In case of product recalls, detailed weighing data can help identify affected batches and facilitate investigations.
- Quality assurance: Traceability data can be used to monitor product quality trends and identify potential issues.
5. Regulatory Compliance:
- Industry standards: Batching scales help food manufacturers comply with industry standards and regulations related to product weight, labeling, and safety.
- Audits and inspections: Accurate weighing records can be used to support audits and inspections conducted by regulatory authorities.
- Consumer confidence: Adherence to regulations demonstrates a commitment to food safety and quality, building consumer trust.
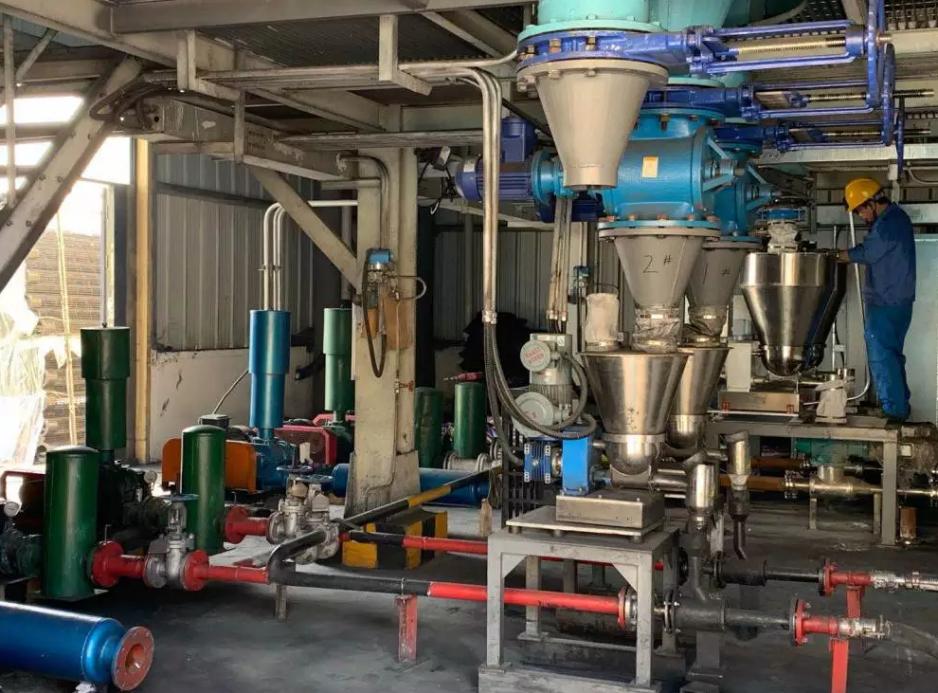
Specific Requirements for Batching Scales in the Food Industry
Batching scales, which are precision industrial weighing scale designed to weigh large quantities of material, are essential in the food industry. To meet the stringent requirements of food production, these scales must have a distinct set of characteristics that ensure precise, sanitary, and efficient operations.
1. Precision:
- Accurate measurements: Batching scales must deliver highly accurate measurements to ensure product consistency and meet regulatory requirements. For instance, scales with a readability of 0.1g or 0.2g are commonly used in the food industry to guarantee precise weighing.
- Traceability: Accurate weighing data is essential for traceability, enabling manufacturers to track products from raw materials to finished goods. This enhances food safety and quality, as it allows for rapid identification and recall of products in case of any issues.
2. Hygiene:
- Food-grade materials: Batching scales used in food processing must be constructed from food-grade materials, such as stainless steel, to prevent contamination and comply with hygiene regulations. These materials are resistant to corrosion, bacteria, and other contaminants, ensuring a safe and sanitary production environment.
- Easy cleaning: The design of these scales should facilitate thorough cleaning and sanitization to maintain a hygienic production environment. Features like smooth surfaces, removable parts, and water-resistant seals can contribute to easy cleaning and maintenance.
3. Stability:
- Vibration resistance: Batching scales must be resistant to vibrations to ensure accurate measurements, especially in dynamic production environments. Vibrations can cause fluctuations in weight readings, leading to inaccurate measurements and product inconsistencies.
- Robust construction: Durable construction is essential to withstand the rigors of industrial use and minimize downtime. Sturdy frames, high-quality components, and proper installation can contribute to the stability and longevity of batching scales.
4. Automation:
- Integration with production lines: Batching scales should seamlessly integrate with existing production lines, enabling automated weighing and data capture. This reduces manual labor, increases efficiency, and minimizes the risk of human error.
- User-friendly interfaces: Intuitive interfaces and controls simplify operation and reduce the risk of errors. User-friendly features, such as touchscreens and clear displays, can make it easier for operators to use the scales effectively.
5. Maintenance:
- Modular design: Modular components facilitate easy maintenance and repair, minimizing downtime. A modular design allows for individual components to be replaced or repaired without the need to dismantle the entire scale.
- Accessibility: Easily accessible components allow for quick inspections and cleaning. This reduces maintenance time and costs, and helps to ensure that the scale remains in optimal working condition.
6. Adaptability:
- Customization: Batching scales should be customizable to meet specific production requirements, such as different product weights, packaging formats, and production rates. This ensures that the scale can be tailored to the unique needs of each manufacturing process.
- Flexibility: The ability to accommodate various products and processes enhances the versatility of the scale. This flexibility is essential in food manufacturing environments, where production can vary widely.
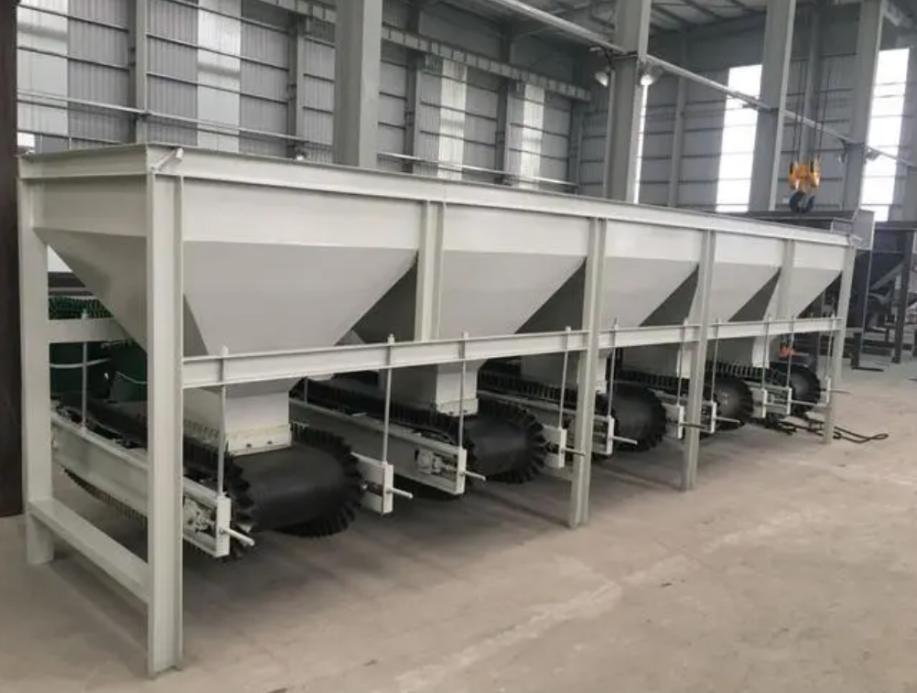
The Indispensable Role of Batching Scales
Batching scales have become an indispensable tool in the modern food industry. These scales help food manufacturers succeed by providing precise weighing, increasing efficiency, and ensuring product quality. As technology advances, we can expect to see more innovative batching scale solutions emerge. These advancements will enhance food manufacturers’ capabilities and help them meet the industry’s ever-changing demands.
For more latest news about batching scale, you can follow the news released by scale expert Bincen.