Belt Scales: A Comprehensive Guide to Boosting Productivity
In today’s competitive industrial landscape, maximizing efficiency and minimizing waste are critical considerations. Accurate material measurement is essential for achieving these goals. This is where belt scales come in. These ingenious devices continuously weigh and monitor the flow of materials on conveyor belts, providing critical real-time data for optimizing manufacturing processes. This article delves into the world of belt scales, examining their various types and applications in various industries. We’ll teach you how to choose the best belt scale for your specific needs, taking into account material properties, capacity requirements, and conveyor belt compatibility. Finally, we’ll walk you through the necessary maintenance procedures to keep your belt scale running smoothly for many years.
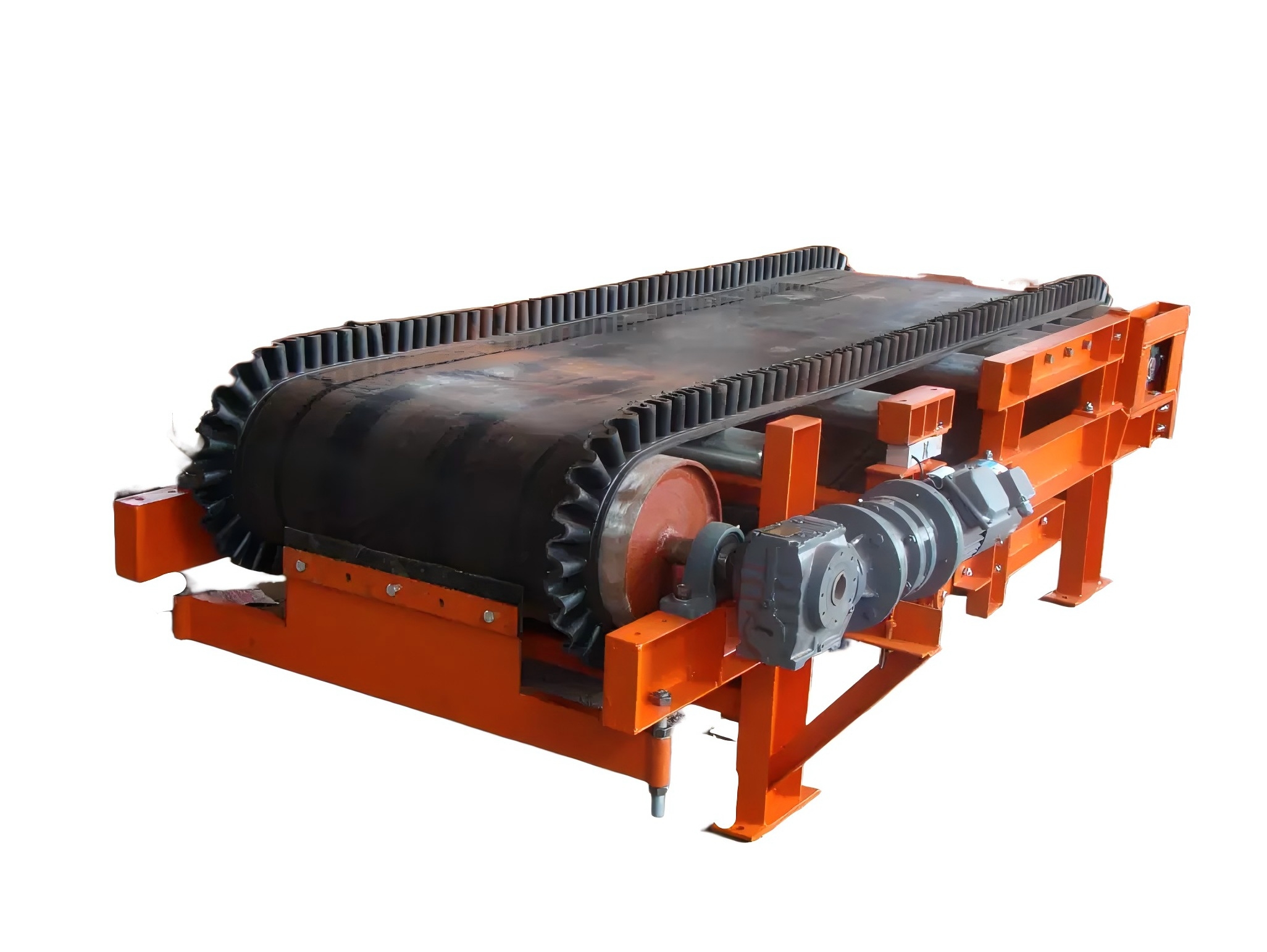
What Are the Different Types of Belt Scales?
Belt Scale
- Measuring Belt Scale: This is the most basic type, which continuously measures material flow rate along a conveyor belt. It’s ideal for applications that need real-time monitoring and production control.
- Quantitative Belt Feeder: This type accurately regulates and measures material flow at a predetermined rate. It is ideal for situations requiring consistent material feeding, such as manufacturing processes.
- Weigh Belt Feeder: Similar to a quantitative feeder, it accurately measures and controls the material weight being fed. Frequently used in conjunction with mixing or blending operations.
- Speed Regulating Belt Scale: This type maintains a constant belt speed despite variations in material load. This ensures uniform material flow and precise measurement, especially for lightweight materials.
Ancillary Equipment
Screw feeders can work alongside belt feeders for even more precise material handling in specific applications. Screw feeders are particularly effective at metering very fine powders or materials that do not flow well on conveyor belts.
Control Systems
Centralized and Decentralized Control System for Weighing and Conveying. The Centralized Control System manages and monitors multiple belt scales from a single location. Provides effective data collection, analysis, and control for large-scale operations. They also use a decentralized control system. Each belt scale has its separate control unit. This is easier to set up, but it may not have the same data management capabilities as a central system.
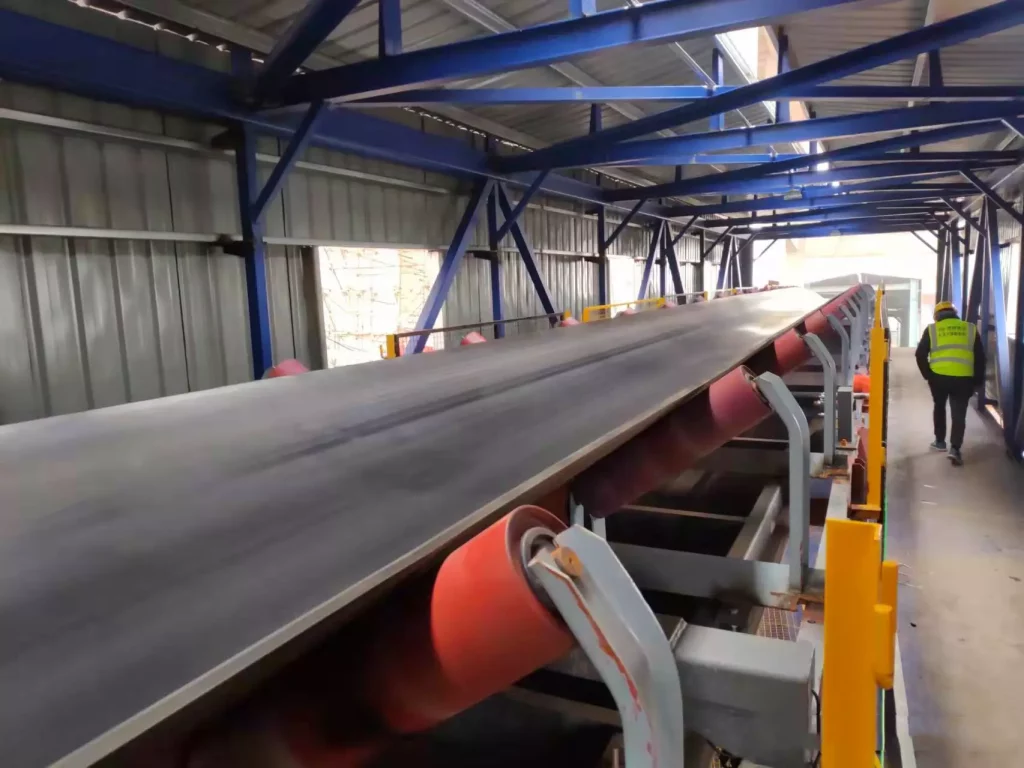
Applications of Belt Scales in Different Industries
Belt scales play a crucial role in optimizing production and streamlining processes across various industries. Here’s a closer look at how belt scales are utilized in different sectors:
Manufacturing
Belt scales are used in manufacturing plants to precisely measure incoming raw materials such as grain, powders, and chemicals. This accuracy leads to consistent product quality and less material waste. Quantitative belt feeders precisely control ingredient weight and flow rate, resulting in accurate mixing and blending. This is especially important in industries such as pharmaceuticals, food processing, and chemicals, where precise recipe adherence is essential. Real-time data from belt scales enables manufacturers to track material usage and maintain optimal inventory levels. This reduces the risk of stockouts and overstocking, resulting in higher production efficiency and cost savings.
Mining
Belt scales are used to continuously monitor the weight and flow rate of extracted minerals such as coal, iron ore, and copper. This data enables mining operations to optimize extraction processes and ensure efficient transportation to processing facilities. Belt scales precisely measure material loaded onto stockpiles, enabling mining companies to keep accurate inventory records and optimize loading operations. Belt scales are capable of detecting overload and potential damage in conveyor belt systems transporting mined materials. This helps to avoid equipment failures and costly downtime.
Agriculture
Belt scales are commonly used in grain elevators and processing facilities to precisely measure incoming and outgoing grain shipments. This ensures fair pricing for farmers and efficient grain management at processing plants. Quantitative belt feeders precisely control the application rate of fertilizers and seeds during planting, resulting in increased crop yield and less waste. Belt scales are used on farms to track the weight and movement of bulk materials such as animal feed or harvested crops, allowing for more accurate inventory control and decision-making.
Recycling
Belt scales that are integrated with sorting systems help to accurately weigh and categorize various recyclable materials. This information aids in optimizing sorting processes and maximizing the value of recovered materials. Belt scales monitor the flow rate of materials entering and exiting recycling facilities, enabling effective process control and optimization. Accurate data on incoming and processed recyclables enables recycling plants to maintain optimal inventory levels and ensure efficient material handling.
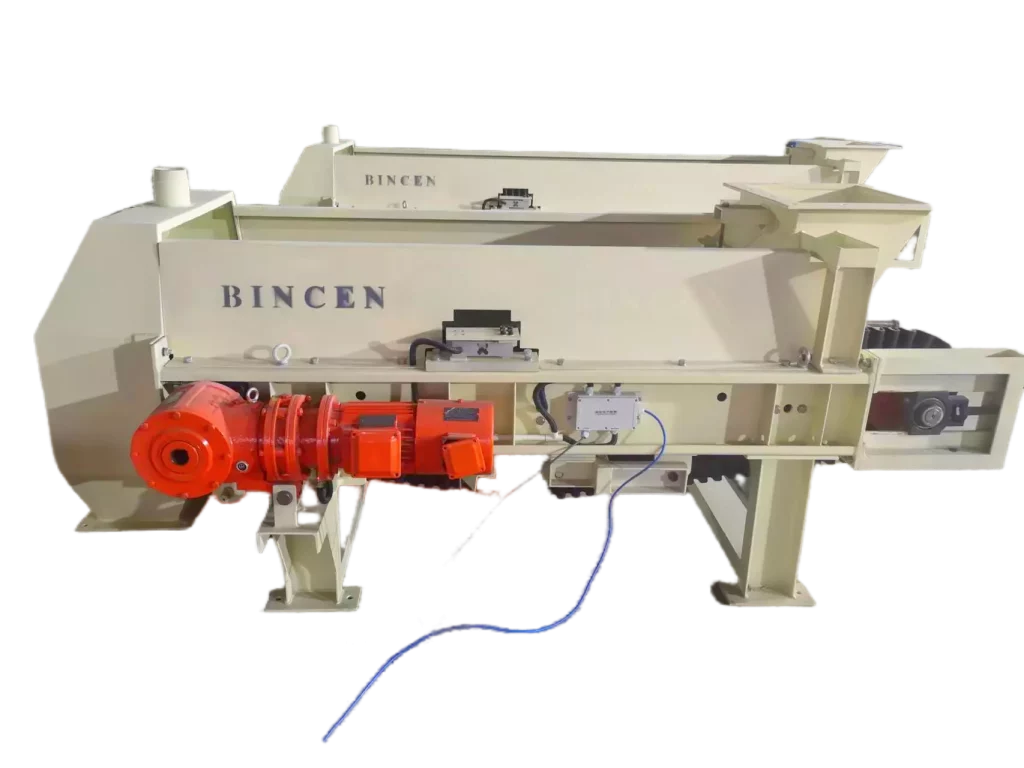
Factors to Consider When Choosing a Belt Scale
Selecting the optimal belt scale for your needs requires careful consideration of various factors. Here’s a detailed breakdown of the key aspects to evaluate before making your decision:
Material Characteristics
Understanding the material you will be weighing is critical. Belt scales are suitable for a wide range of materials, including free-flowing powders and large, chunky rocks. However, certain materials may necessitate specialized belt scale features. Consider how the material moves along a conveyor belt. Does it flow easily or tend to bridge or clump? Belt scale design may require adjustments for materials that do not flow uniformly. To ensure accurate measurement of coarse or irregularly shaped materials, special weighbridge designs may be required.
Capacity Requirements
Determine the belt scale’s maximum weight capacity per unit time. Choosing a scale with insufficient capacity may result in inaccurate measurements and equipment damage. If you need to measure very low material flow rates, consider the scale’s minimum weight sensitivity. Some belt scales excel at detecting even minor weight differences.
Belt Conveyor Characteristics
Make sure the belt scale you choose is compatible with your conveyor belt’s width and speed. Mismatched sizes can result in inaccurate measurements and possible equipment wear. Consistent belt tension is essential for accurate measurements. The belt scale must be compatible with the tensioning system on your conveyor. The spacing between conveyor idlers and the overall support structure can have an impact on belt scale performance. Consult your belt scale supplier to ensure compatibility.
Selecting the right belt scale requires expertise. Consulting with a qualified belt scale manufacturer is highly recommended. They can evaluate your specific requirements, analyze your conveyor system, and recommend the best belt scale for your situation. Look for a supplier with a proven track record, excellent customer service, and prompt after-sales support.
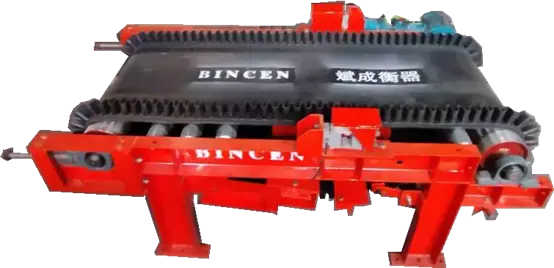
Maintaining Belt Scales for Optimal Performance
Belt scales are vital tools for accurate material measurement and efficient production. To ensure they deliver optimal performance and reliable data, a proper maintenance plan is crucial. Here’s a breakdown of key maintenance practices for belt scales:
Regular Inspections
Conduct regular visual inspections of the belt scale system. Check for any signs of wear and tear on the weighbridge, belt wipers (if applicable), and overall structure. Loose fasteners, damaged components, or material buildup should be addressed promptly. Ensure the conveyor belt tracks properly over the weighbridge to maintain accurate measurement. Misalignment can lead to inaccurate readings. Perform periodic calibration verification to confirm the accuracy of the belt scale. This typically involves introducing known test weights and comparing the measured weight with the actual weight. The frequency of verification depends on the scale’s usage, accuracy requirements, and regulatory guidelines in your industry.
Cleaning and Maintenance Procedures
Develop a cleaning schedule based on the material being conveyed and the operating environment. Material buildup on the weighbridge or belt can affect accuracy. Regularly clean these components according to the manufacturer’s recommendations. For materials prone to sticking or building up, consider installing belt-cleaning systems like scrapers or brushes. These can help maintain clean belt surfaces for optimal performance.
Conclusion
Installing belt scales is a strategic investment in operational efficiency. Their ability to provide accurate and reliable material measurement data translates to numerous advantages. Belt scales benefit a wide range of industries, from optimizing production processes and reducing waste to ensuring consistent product quality and improving inventory management. Understanding the various types of belt scales available and their suitability for specific applications is critical to making an informed decision. Implementing a comprehensive maintenance plan will ensure that your belt scale operates at peak performance throughout its lifespan, maximizing your return on investment.