Different Packaging Scales: From Small Bags to Ton Bags
Packaging scales ensure accurate product weight and efficient packaging processes. From small-scale operations to large-scale industrial facilities, packaging scales come in various types, each designed to meet specific needs. Packaging scales supplier Bincen will give a deep introduction to the different types of packaging scales, their unique characteristics, and their applications across various industries. We will also explore the key factors to consider when selecting the right packaging scale for your specific requirements.
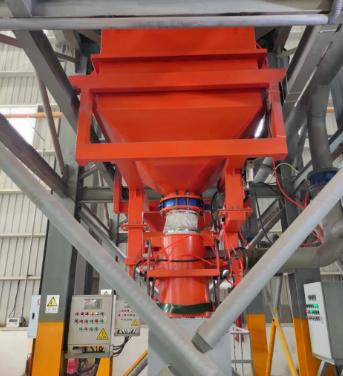
Characteristics and Applications of Various Packaging Scales
Packaging scales are designed to accurately weigh and dispense products into packages of predetermined quantities. By ensuring precise measurements, packaging scales enhance production efficiency, reduce material waste, and maintain product quality, ultimately contributing to overall operational success. Packaging scales can be categorized based on various factors, including the type of material being packaged, the desired package size, and the level of automation.
Quantitative Packaging Machine
Quantitative packaging machines are precision instruments designed to accurately measure and dispense specific quantities of products into various packaging formats. They are essential tools in industries where precise weight control is paramount, ensuring product quality, regulatory compliance, and customer satisfaction.
Key Features and Benefits
- High Precision: These machines employ advanced weighing technologies to deliver accurate measurements, minimizing product giveaway and ensuring consistent quality.
- High Efficiency: Automated processes and optimized design enable high-speed packaging, reducing labor costs and increasing overall productivity.
- Versatility: Quantitative packaging machines can handle a wide range of products, from fine powders to coarse granules and liquids, accommodating diverse industry needs.
- Adaptability: These machines can be configured to accommodate various packaging formats, including bags, pouches, bottles, and cartons, offering flexibility in packaging design.
- Reduced Waste: Precise dosing and efficient material handling minimize product waste, contributing to cost savings and environmental sustainability.
Applications
- Food Industry: Packaging of snacks, cereals, spices, and other food products.
- Pharmaceutical Industry: Packaging of medicines, tablets, capsules, and powders.
- Chemical Industry: Packaging of chemicals, fertilizers, and other industrial products.
- Cosmetic Industry: Packaging of creams, lotions, and powders.
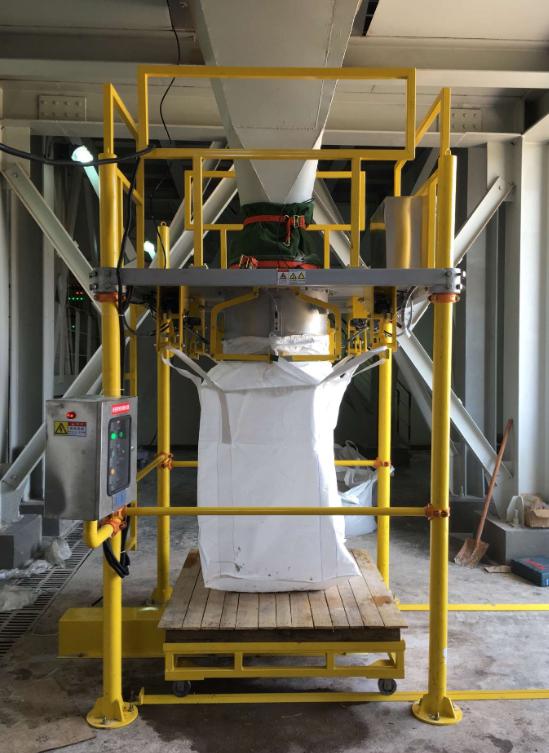
Ton Bag Packaging Machine
Ton bag packaging machines are industrial equipment designed to efficiently fill and seal large, flexible intermediate bulk containers (FIBC) or ton bags. These machines are commonly used in industries that handle large quantities of bulk materials, such as chemicals, minerals, and agricultural products.
Key Features and Benefits
- High Capacity: Ton bag packaging machines can handle large volumes of material, significantly reducing packaging time and labor costs.
- Automation: Advanced automation features, including automatic bag placement, filling, and sealing, minimize human intervention and improve efficiency.
- Flexibility: These machines can accommodate a wide range of bag sizes and materials, providing versatility in packaging operations.
- Durability: Robust construction and high-quality components ensure long-term reliability and durability in demanding industrial environments.
- Safety: Integrated safety features, such as emergency stop buttons and interlocks, protect operators and minimize accidents.
Applications
- Chemical Industry: Packaging of chemicals, fertilizers, and other industrial products.
- Mining Industry: Packaging of minerals, ores, and other mining products.
- Agricultural Industry: Packaging of grains, seeds, and fertilizers.
- Construction Industry: Packaging of cement, sand, and other construction materials.
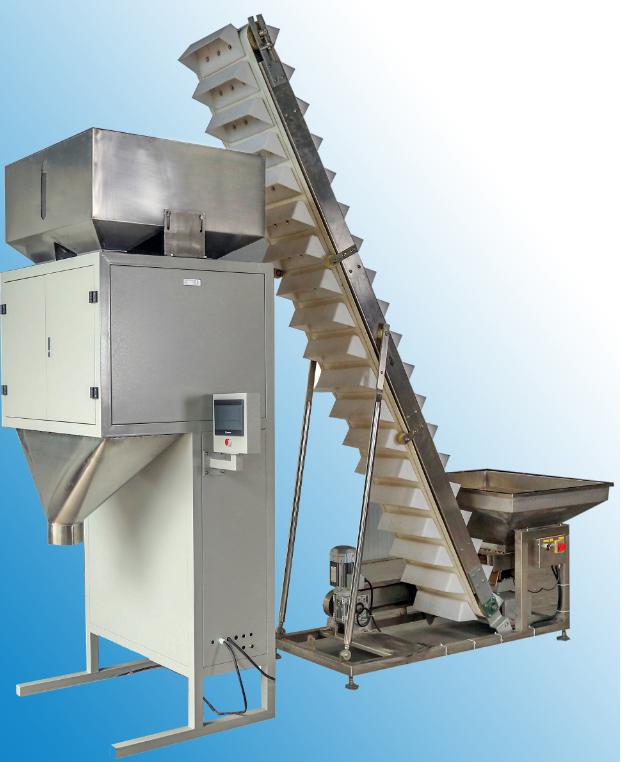
Compound Fertilizer Packaging Machine
Compound fertilizer packaging machines are specialized equipment designed to accurately and efficiently package compound fertilizers. These machines are crucial in the agricultural industry, ensuring the precise delivery of nutrients to crops.
Key Features and Benefits
- Corrosion Resistance: The machines are constructed with materials that can withstand exposure to corrosive substances commonly found in fertilizers, such as acids and salts.
- Moisture Resistance: The equipment is designed to prevent moisture ingress, which can degrade fertilizer quality and lead to caking.
- Wear Resistance: Components that come into contact with abrasive fertilizers are made of durable materials to minimize wear and tear.
- Precise Dosing: Advanced weighing and dispensing systems ensure accurate dosing of fertilizers, optimizing nutrient application and maximizing crop yields.
- Efficient Operation: Automated processes and streamlined design minimize labor requirements and increase productivity.
- Flexibility: These machines can handle various types of compound fertilizers, including granular, powdered, and liquid formulations.
Applications
- Package fertilizers in various formats: Bags, sacks, or bulk containers.
- Ensure accurate dosing: To optimize nutrient application and prevent over- or under-fertilization.
- Protect fertilizer quality: By preventing moisture ingress and contamination.
- Improve operational efficiency: Through automation and streamlined processes.
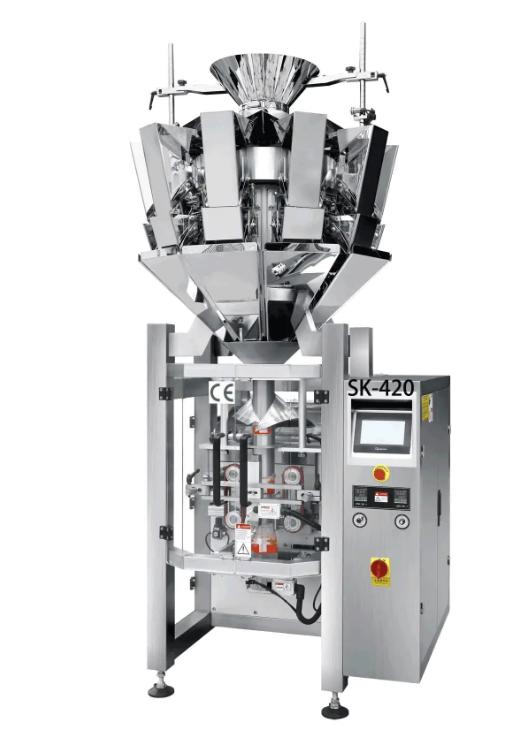
Double Spiral Feeding Hopper-less Packaging Machine
Double spiral feeding hopper-less packaging machines are innovative pieces of equipment designed to efficiently and accurately package a wide range of materials. They are especially well-suited for industries that require precise dosing and high-speed packaging, such as the food and chemical sectors.
Key Features and Benefits
- Compact Design: These machines have a compact footprint, making them ideal for applications with limited space.
- Hopper-less Operation: The absence of a traditional hopper eliminates the risk of material bridging and ensures consistent product flow.
- Wide Material Adaptability: Double spiral feeding systems can handle a variety of materials, including powders, granules, and flakes, with different flow characteristics.
- High Precision: Advanced weighing and dosing systems ensure accurate filling, reducing product waste and meeting stringent quality standards.
- Gentle Product Handling: The spiral feeding mechanism minimizes product damage, preserving the integrity of delicate materials.
- Easy Cleaning and Maintenance: The hygienic design and easily accessible components facilitate cleaning and maintenance, ensuring product safety and operational efficiency.
Applications
- Food Industry: Packaging of spices, seasonings, powdered milk, and other food ingredients.
- Chemical Industry: Packaging of fine chemicals, pigments, and additives.
- Pharmaceutical Industry: Packaging of pharmaceutical powders and granules.
- Cosmetic Industry: Packaging of powders and other cosmetic ingredients.
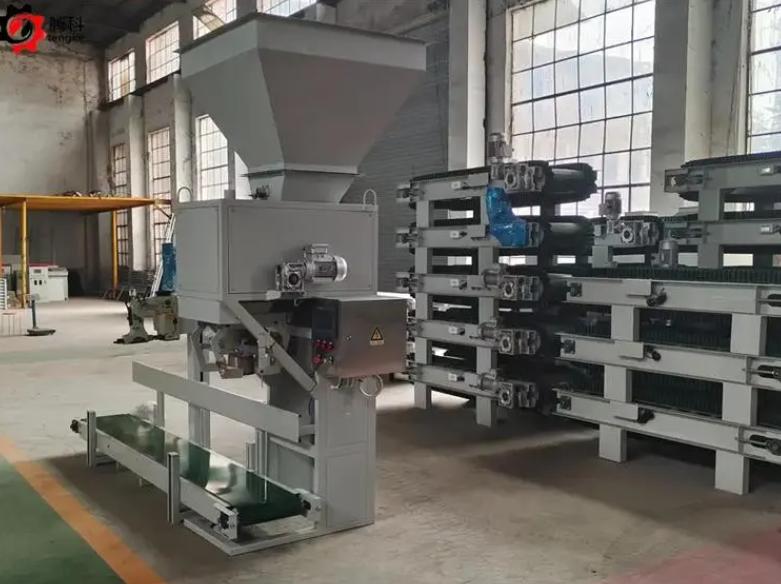
15L Small Bag Powder Packaging Machine
15L small bag powder packaging machines are specialized pieces of equipment designed to accurately and efficiently fill small bags with powdered materials. These machines are commonly used in industries that require precise dosing and high-speed packaging of small quantities of products.
Key Features and Benefits
- High Precision: These machines employ advanced weighing technologies to ensure accurate filling of each bag, minimizing product waste and meeting stringent quality standards.
- High Speed: Automated processes and optimized design enable high-speed packaging, increasing productivity and reducing labor costs.
- Compact Design: These machines are often compact and space-saving, making them suitable for small-scale operations or integration into existing production lines.
- Versatility: Many models can accommodate a variety of bag sizes and materials, offering flexibility in packaging design.
- Easy Operation: User-friendly interfaces and intuitive controls simplify operation and reduce training requirements.
- Gentle Product Handling: The packaging process is designed to minimize product damage, preserving the quality of delicate powders.
Applications
- Food Industry: Packaging of food additives, spices, and other powdered ingredients.
- Pharmaceutical Industry: Packaging of pharmaceutical powders and intermediates.
- Chemical Industry: Packaging of fine chemicals and powders.
- Cosmetic Industry: Packaging of cosmetic powders and pigments.
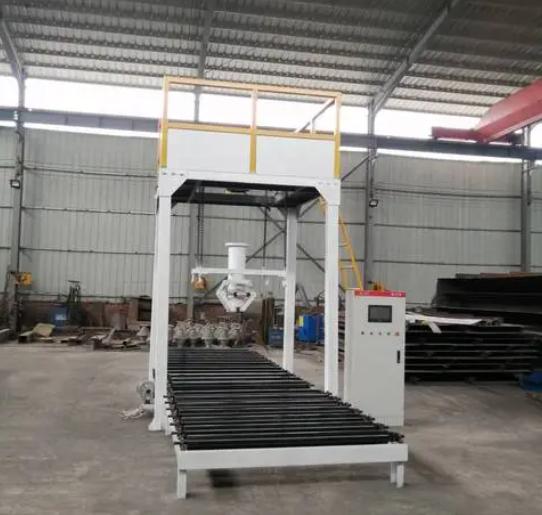
Factors to Consider When Selecting a Packaging Scale
Factor 1: Material Characteristics
- Density: The density of the material will determine the type of feeder and weighing system required. For example, high-density materials may require a more robust feeder, while low-density materials may require a gentler approach.
- Flowability: The flowability of the material will affect the choice of feeder and dosing system. Free-flowing materials can be handled by simpler feeders, while cohesive or sticky materials may require more complex systems, such as vibratory feeders or screw feeders.
- Particle Size: The particle size of the material will influence the choice of screening and sifting equipment, as well as the design of the dosing system.
Factor 2: Packaging Specifications
- Bag Size and Shape: The dimensions and shape of the packaging bags or containers will determine the size and configuration of the packaging machine.
- Material: The material of the packaging (e.g., paper, plastic, foil) will influence the type of sealing mechanism required.
- Closure Type: The type of closure (e.g., heat seal, adhesive seal, tie-off) will determine the appropriate sealing system.
Factor 3: Production Requirements
- Capacity: The required production rate will determine the speed and capacity of the packaging machine. High-speed packaging lines will require machines with higher throughput.
- Accuracy: The desired level of accuracy will influence the choice of weighing system and the number of checkweighers.
- Automation: The degree of automation required will depend on factors such as labor costs and the complexity of the packaging process.
Factor 4: Budget Constraints
- Initial Investment: The cost of the packaging machine will vary depending on its features and capabilities.
- Operating Costs: Consider ongoing costs such as maintenance, spare parts, and energy consumption.
- Return on Investment: Evaluate the potential return on investment based on the expected increase in productivity and efficiency.
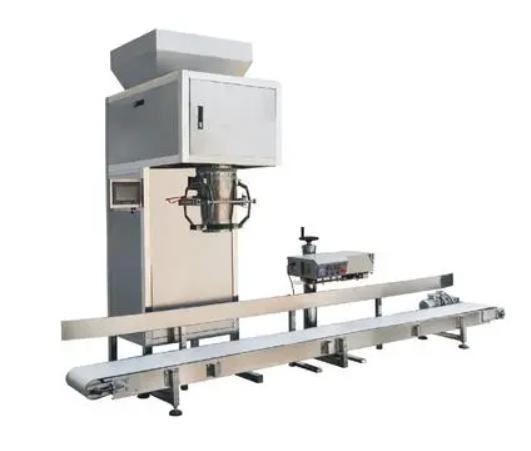
In Closing
Packaging scales are important for businesses across various industries. With different types of packaging scales and their respective applications, businesses can optimize their packaging processes, reduce costs, and improve product quality. Following the introduction provided by packaging scales supplier Bincen, when selecting a packaging scale, it is essential to consider factors such as material characteristics, packaging specifications, production requirements, and budget constraints.