How Batching Control Systems Work?
Batching control systems play a vital role in industries that rely on precise and consistent mixing or blending of ingredients. From food production to pharmaceuticals, these systems automate and optimize the batching process, guaranteeing quality and efficiency. This article delves into the core components of batching control systems, explores the automation process, examines their applications across various industries.
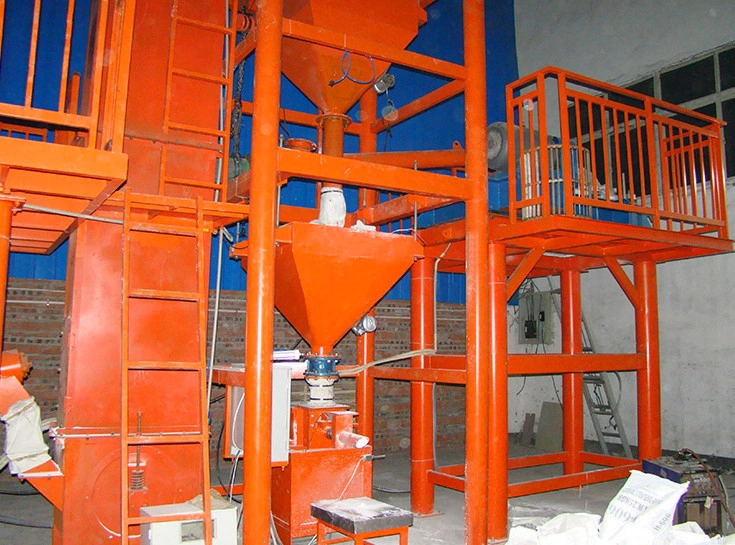
The Core Components of a Batching Control System
The success of a batching control system hinges on the seamless interaction of its key components. Let’s explore each component in more detail and understand its role in ensuring a precise and efficient batching process:
1. Sensors
- Load Cells: These are the workhorses of batching systems, precisely measuring the weight of ingredients being added to the batch. They are typically placed under storage vessels or directly on conveyor belts. Modern load cells are highly accurate and can handle a wide range of weight capacities.
- Flowmeters: For liquid ingredients or materials dispensed by volume, flowmeters track the flow rate and total volume dispensed. Different types of flowmeters are suited for various liquids (e.g., positive displacement, mass flowmeters, Coriolis meters).
- Level Sensors: These sensors monitor the fill level of ingredient storage vessels, alerting the system when a refill is necessary. They can be ultrasonic, optical, or pressure-based, depending on the material and container type.
- Temperature Sensors: For processes where temperature is critical (e.g., chemical reactions, food preparation), temperature sensors monitor ingredient or mixture temperature. This allows the system to adjust parameters or initiate corrective actions if the temperature deviates from the recipe.
Control Unit (PLC)
The PLC (Programmable Logic Controller) acts as the brain of the batching system. It receives real-time data from sensors, compares it to the pre-programmed recipe, and issues control commands to actuators and valves. Modern PLCs are powerful and flexible. They can store numerous recipes, perform complex calculations, and even adapt the process based on real-time sensor data for optimized control.
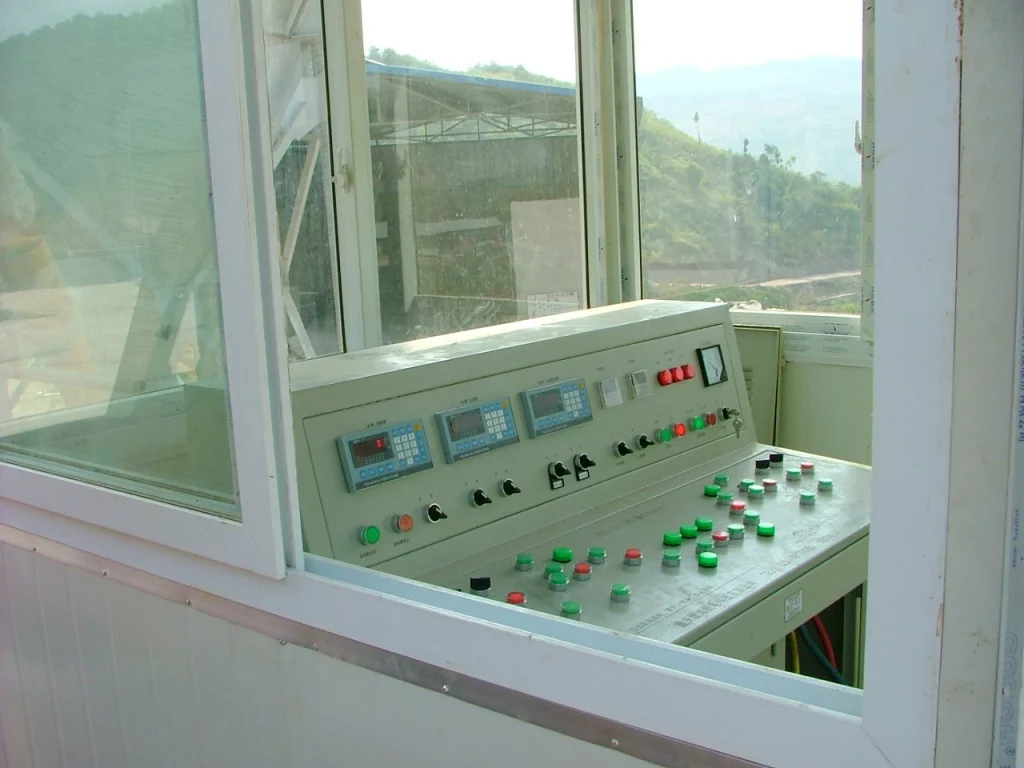
3. Human Machine Interface (HMI)
The HMI serves as the primary interface between the operator and the batching control system. It typically features a touchscreen display that allows for:
- Recipe Selection and Management: Operators can choose a pre-programmed recipe or create new ones by entering ingredient quantities and other parameters.
- Process Monitoring: The HMI displays real-time data from sensors, providing a clear view of the batching progress. Operators can monitor ingredient levels, flow rates, and other critical parameters.
- Alarm Management: The HMI displays alerts and alarms if any deviations from the recipe occur, allowing operators to take corrective action.
- Data Logging and Reporting: The HMI can record and store batching data for analysis and reporting purposes. This data can be used for quality control, process optimization, and troubleshooting.
4. Valves and Actuators
Valves control the flow of ingredients into the batching vessel. They can be solenoid valves, pneumatic valves, or butterfly valves, depending on the material properties and desired control level.Actuators convert electrical signals from the PLC into mechanical movement, operating the valves. They can be pneumatic actuators, hydraulic actuators, or electric actuators, chosen based on the force required and available power source.
5. Storage Vessels
Storage vessels hold the various ingredients used in the batching process. They can be tanks, silos, or hoppers, and their design depends on the material properties (e.g., liquid vs. solid, temperature sensitivity).
Some storage vessels may have built-in agitation systems to prevent settling or ensure proper material flow during dispensing.
The Batching Control Process with Automation
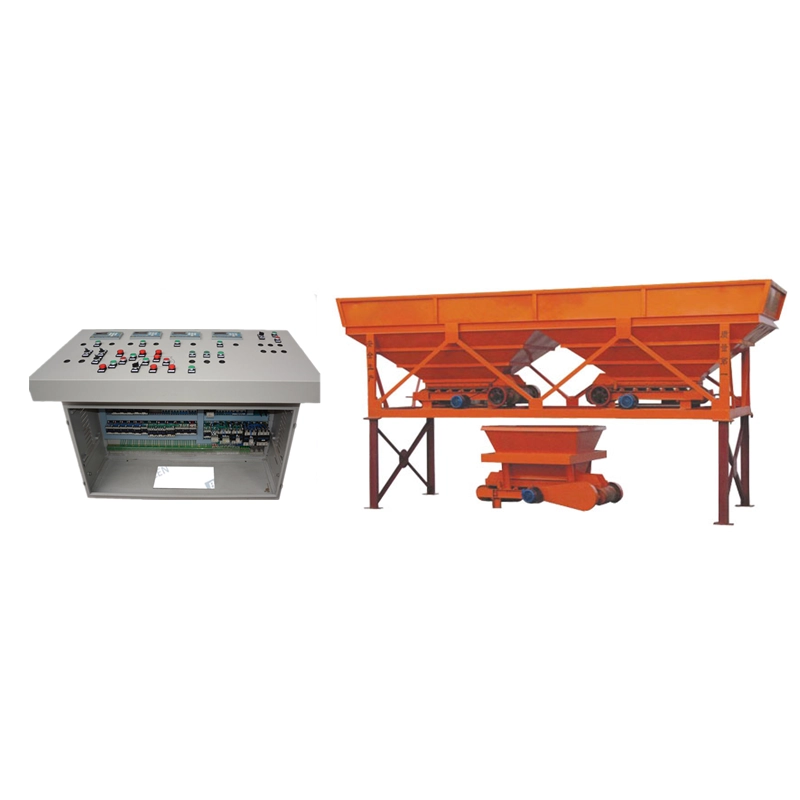
The magic of a batching control system lies in its ability to automate the entire process, ensuring precision and efficiency. Here’s a closer look at how automation streamlines the batching process:
1. Recipe Selection and Pre-programming
Instead of manually measuring each ingredient, operators simply select a pre-programmed recipe on the HMI. This recipe, created by experienced personnel or based on established formulas, specifies the exact type and quantity of each ingredient needed for the desired product. The recipe can also include parameters for mixing times and speeds, ensuring a consistent final product.
2. Precise Dosing and Ingredient Control
Once the recipe is chosen, the PLC takes center stage. It receives the ingredient information and sends commands to the valves and actuators. These components meticulously control the flow of each ingredient into the batching vessel. Here’s where the magic of sensors comes in. Load cells mounted on the storage vessels or directly under the hoppers precisely measure the weight of each ingredient being added. Similarly, flowmeters can be used for liquids, ensuring the exact volume is dispensed. The PLC continuously monitors the sensor data and compares it to the recipe specifications. If any deviation occurs, the system can automatically adjust the valve positions to ensure the correct amount is added.
3. Mixing and Blending Automation
After all the ingredients are accurately added, the PLC activates the mixing equipment. This could involve agitators, mixers, or blenders, depending on the specific application. The system can control the mixing speed and duration based on the recipe requirements, ensuring a homogenous blend is achieved every time.
4. Real-time Data Recording and Monitoring
Throughout the batching process, the system meticulously records all the data. This includes the weight or volume of each ingredient added, the mixing times and speeds, and any deviations that might have occurred. This data is invaluable for maintaining quality control, troubleshooting any issues, and optimizing future batches. Operators can monitor the process in real-time on the HMI, allowing them to intervene if necessary.
5. Integration with Quality Control
For added assurance, batching control systems can be integrated with quality control equipment. This allows for automatic analysis of the final product during or after the batching process. By comparing the results to pre-defined specifications, the system can identify any inconsistencies or potential quality issues. This real-time feedback allows for immediate corrective actions to be taken, preventing defective products from reaching production.
Generally, automation transforms the batching process from a manual, error-prone task to a precise and efficient operation. By automating ingredient dosing, mixing control, and data recording, batching control systems ensure consistent product quality, minimize waste, and streamline production for a wide range of industries.
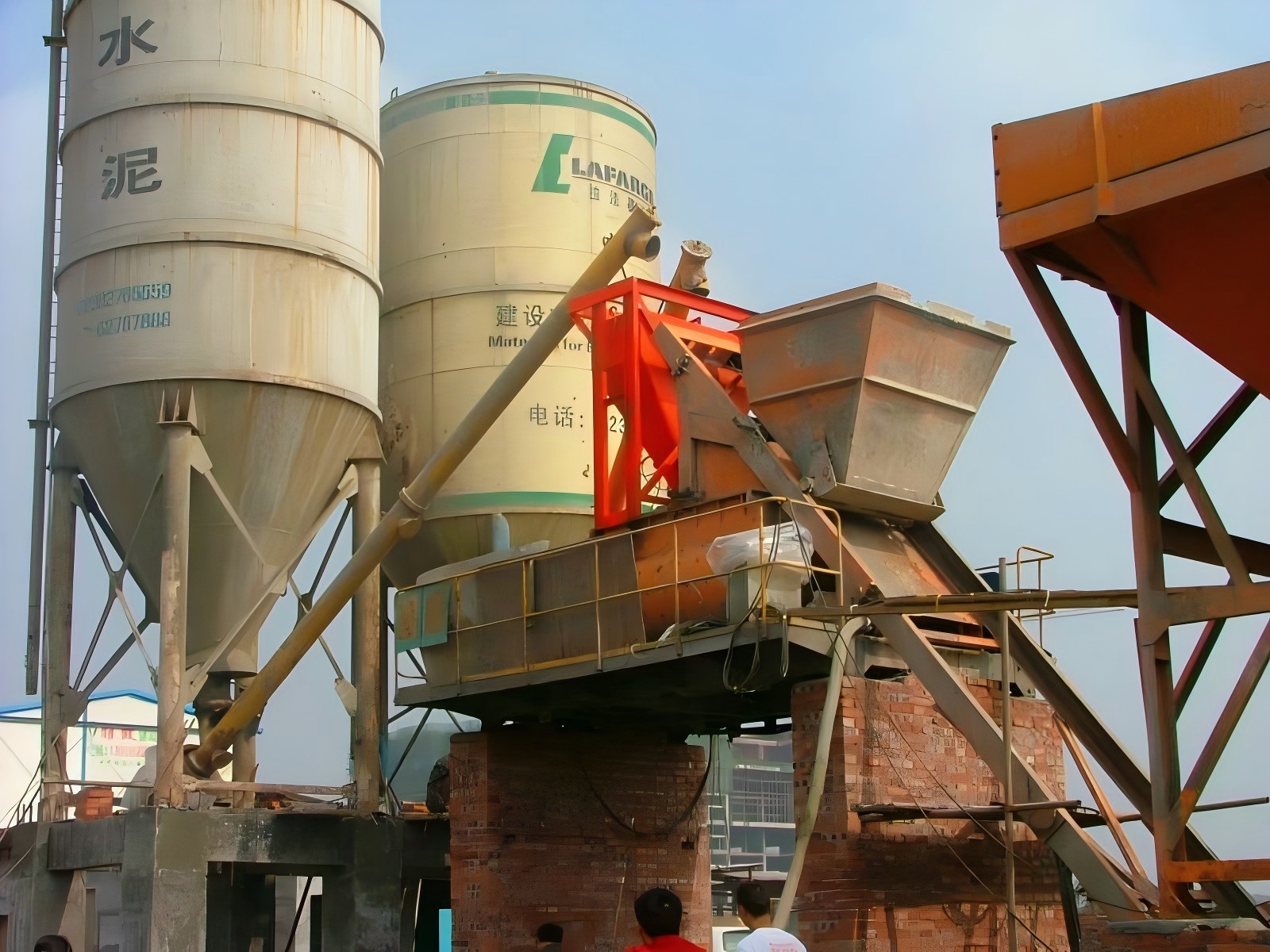
Applications of Batching Control Systems Across Industries
Batching control systems are a cornerstone of efficiency and quality control in a wide range of industries. Here’s a deeper look at how these systems benefit various sectors:
Food and Beverage
Batching control systems play a crucial role in the food and beverage industry by precisely measuring ingredients for dough, beverages, sauces, and other products. This ensures consistent quality, reduces waste due to inaccurate measuring, and allows for easy recipe scaling for increased production. Furthermore, by automating the addition of ingredients like spices, flavorings, and preservatives, batching control systems minimize the risk of human error and potential contamination.
Chemical and Pharmaceutical
In the highly regulated world of chemicals and pharmaceuticals, precision and accuracy are paramount. Batching control systems become vital tools for ensuring consistent product quality and adherence to strict safety protocols. These systems precisely measure and combine various chemicals for products like fertilizers, detergents, and medications. The ability to record all batching data allows for complete traceability, facilitating compliance with regulatory requirements and ensuring product safety. Additionally, batching control systems can be integrated with quality control equipment to analyze the final product in real-time, allowing for immediate adjustments if necessary.
Plastics and Rubber
The properties of plastic and rubber products are highly dependent on the precise combination of materials used. Batching control systems ensure consistent material properties by accurately measuring resins, fillers, and additives during the production process. This not only leads to predictable product performance but also minimizes the risk of product defects and costly rework. By automating the dosing of ingredients, batching control systems also improve production speed and efficiency in plastics and rubber manufacturing.
Paints and Coatings
A consistent and high-quality paint or coating requires a precise blend of pigments, binders, and solvents. Batching control systems excel at ensuring this consistency by accurately measuring each component according to the chosen formulation. This translates to paints and coatings with reliable color matching, optimal viscosity, and consistent application properties. Additionally, by optimizing ingredient usage, batching control systems can help reduce production costs and minimize waste in the paint and coating industry.
Concrete Production
The strength and durability of concrete depend on the accurate mixing of sand, gravel, cement, and water. Batching control systems guarantee high-quality concrete mixes by precisely measuring and blending these essential ingredients. This not only ensures the structural integrity of buildings and infrastructure but also allows for customizing concrete mixes for specific applications. By automating the batching process, these systems also improve efficiency and reduce production time in concrete plants.
Bincen Batching Control Systems
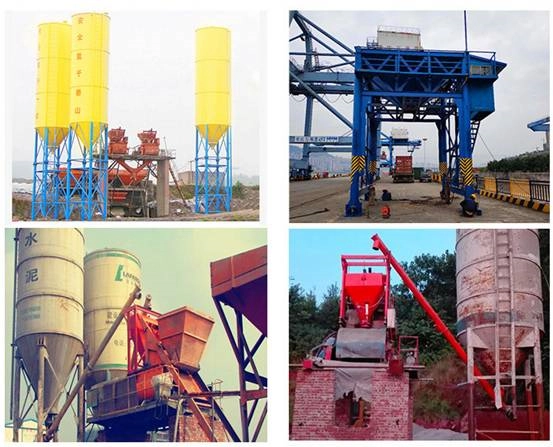
Bincen stands out in the field of batching control systems by offering a range of advanced solutions designed to cater to the specific needs of various industries. Our commitment to user experience is evident in the design of our systems, which boast intuitive Human Machine Interfaces (HMI) that make operation and recipe management a breeze. Whether you’re running a small-scale batching operation or a large-scale production facility, Bincen has a scalable system that can seamlessly adapt to your specific requirements.
But Bincen’s offerings go beyond user-friendliness and scalability. We understand the crucial role data plays in modern manufacturing. That’s why our batching control systems are equipped with robust data analytics tools. These tools empower you to gain valuable insights into your batching processes, allowing you to identify areas for improvement and optimize your recipes for consistent product quality. By leveraging the power of data analytics, Bincen systems empower you to make data-driven decisions that enhance efficiency, minimize waste, and ultimately ensure the consistent quality of your products.
Bincen’s commitment to innovation extends beyond the core functionalities of our batching control systems. We are constantly exploring new technologies and advancements in the field of automation. This ensures that our systems remain at the forefront of the industry, offering cutting-edge features and seamless integration with other automation technologies. By choosing Bincen, you’re not just investing in a batching control system, you’re partnering with a company dedicated to providing future-proof solutions that can grow and adapt alongside your business.