How Do Industrial Batching Scales Enhance Your Production Line?
In today’s competitive manufacturing landscape, precision and efficiency are paramount. Industrial batching scales play a crucial role in achieving these goals by ensuring accurate and consistent measurement of ingredients for your production line. But how exactly do these systems function, and what benefits do they offer? Let’s delve deeper.
System Components of Industrial Batching Scales?
A typical industrial batching scale system is a crucial component in various manufacturing processes, ensuring precise measurement and control of ingredients for consistent product quality. While configurations may vary based on specific needs and industry requirements, these systems generally comprise several key components.
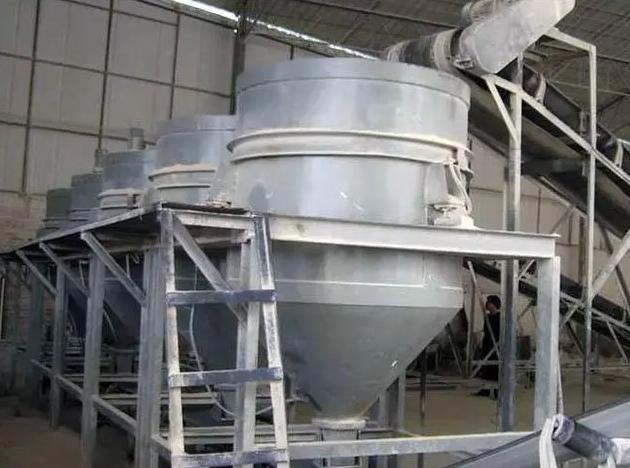
1. Weighbridge
At the heart of the batching scale system lies the weighbridge, often referred to as the platform or scale. This robust structure provides the surface where ingredients are placed for weighing. Constructed from durable materials such as steel or reinforced concrete, the weighbridge is designed to withstand heavy loads and harsh industrial environments. Depending on the application, weighbridges can vary in size, shape, and weight capacity, accommodating the diverse needs of different industries and production processes.
2. Load Cells
Serving as the essential sensing elements, load cells are responsible for converting the weight of the ingredients placed on the weighbridge into an electrical signal. These precision instruments are strategically positioned beneath the weighbridge, directly bearing the load and responding to even the slightest changes in weight. Load cells come in various types, including strain gauge, hydraulic, and pneumatic, each offering unique advantages depending on factors such as accuracy requirements, environmental conditions, and cost considerations.
3. Weighing Indicator
The weighing indicator, also known as the display unit or controller, serves as the interface between the operator and the batching scale system. This digital device provides real-time feedback on the weight of the ingredients being measured, allowing operators to monitor and adjust the process as needed. Modern weighing indicators offer advanced features such as tare functionality, which enables the system to compensate for the weight of containers or packaging materials, ensuring accurate measurement of the actual product. Additionally, some indicators may incorporate data logging capabilities, allowing operators to record and analyze weight data over time for quality control and regulatory compliance purposes.
4. Control System
The control system acts as the brain of the batching scale system, orchestrating the entire operation from start to finish. It receives signals from the load cells, processes the data, and communicates with the weighing indicator to display the measured weight accurately. In more advanced setups, the control system may also interface with other components of the production line, such as automated dispensing systems or conveyor belts, to facilitate seamless material handling and batch processing. Furthermore, the control system often includes built-in algorithms and calibration routines to ensure optimal performance and calibration accuracy, minimizing errors and maximizing productivity.
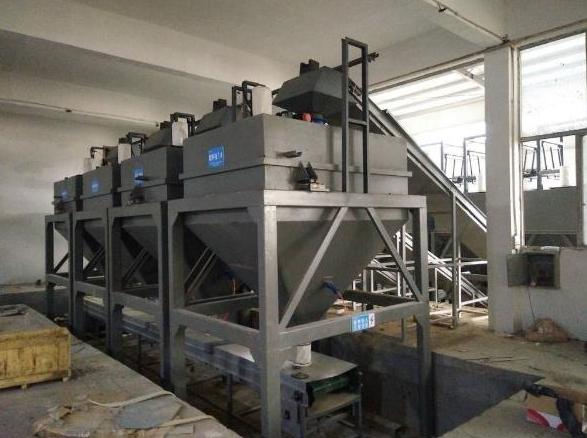
5 Ways Industrial Batching Scales Enhance Production Lines
Industrial batching scales play a crucial role in achieving these goals by ensuring accurate and consistent measurement of ingredients for your production line. But how exactly do these systems function, and what benefits do they offer? Let’s delve deeper into the five key ways industrial batching scales enhance production lines:
1. Increased Accuracy and Reduced Waste
- Eliminating Human Error: Manual weighing methods are inherently susceptible to human error, such as misreadings, incorrect calculations, or fatigue-induced mistakes. Industrial batching scales remove this human element from the equation. Load cells provide highly accurate weight measurements, and digital displays clearly show the weight in real time, eliminating any room for misinterpretation.
- Minimized Material Waste: Even minor inaccuracies in manual weighing can lead to significant material waste over time. Batching scales ensure precise measurement of each ingredient down to the gram, minimizing overfills and underfill. This translates directly to cost savings on raw materials and reduces the environmental impact of your production process.
- Reduced Rejects and Reworks: Inconsistent ingredient measurements can lead to product defects that require rejection or rework. Batching scales promote consistent product quality by ensuring each batch adheres to the exact recipe specifications. This minimizes the number of rejects and reworks, saving time and money.
2. Improved Efficiency and Throughput
- Automated Weighing: Batching scales automate the weighing process, significantly reducing the time and labor required compared to manual methods. Operators simply need to place the container on the weighbridge, and the system takes care of the rest. This frees up valuable labor for other tasks and streamlines the production workflow.
- Faster Production Cycles: The automation offered by batching scales translates to faster production cycles. Ingredients can be weighed quickly and accurately, eliminating the delays associated with manual weighing. This allows for increased production output and the ability to meet higher customer demands.
- Integration with Automated Dispensing Systems: Some advanced batching scale systems can integrate with automated dispensing systems. Once the weight is measured and confirmed, the system can trigger the release of the precise amount of ingredients into the mixing vessel, further reducing manual intervention and accelerating production.
3. Enhanced Inventory Control and Cost Management
- Real-Time Data on Ingredient Usage: Modern batching scales often come equipped with data logging capabilities. This allows for real-time tracking of ingredient usage on a per-batch basis. Production managers can access this data to gain valuable insights into material consumption trends.
- Improved Inventory Management: By knowing exactly how much of each ingredient is being used, production managers can optimize inventory levels. This helps prevent stockouts that can disrupt production and minimizes the need to store excess inventory, reducing carrying costs.
- Proactive Ordering and Cost Reduction: Data analysis from batching scales can help identify areas for optimizing material usage. Production managers can use this information to negotiate better deals with suppliers or explore alternative ingredients that may be more cost-effective.
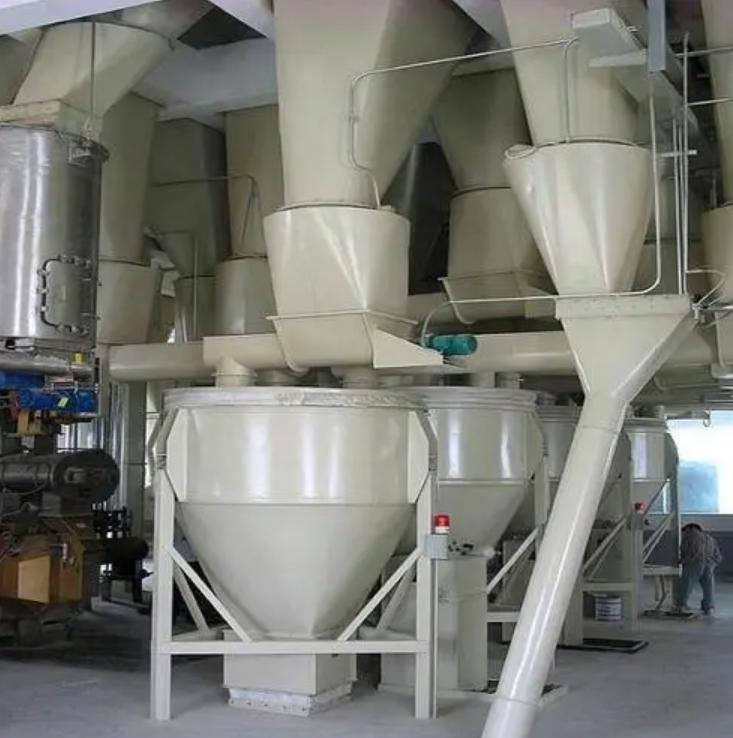
4. Boosted Product Quality and Consistency
- Precise Recipe Adherence: As mentioned earlier, batching scales ensure precise measurement of every ingredient. This allows for consistent product quality across every batch. Without precise measurements, even minor variations in ingredient quantities can lead to inconsistencies in taste, texture, functionality, or even safety concerns. Batching scales eliminate this risk, ensuring your products meet the highest quality standards.
- Reduced Risk of Defects: Inaccurate measurements can lead to product defects. For example, underfilling a key ingredient in a food product might compromise its taste or texture. Batching scales minimize this risk by ensuring every ingredient is present in the correct quantity, leading to fewer defects and improved product quality.
5. Streamlined Data Integration and Reporting
- Automated Data Collection: Many advanced batching scales integrate seamlessly with production management software. This allows for automated data collection on various aspects of the production process, including ingredient usage, production times, and machine performance. This eliminates the need for manual data entry, reducing errors and saving valuable time.
- Improved Decision-Making: The data collected by batching scales can be used to generate detailed reports on production efficiency, ingredient usage trends, and potential areas for improvement. This empowers you to make informed decisions about production processes, resource allocation, and overall operational optimization.
Industrial batching scale systems offer a multitude of benefits that go beyond just accurate measurement. They can streamline your entire operation, minimize waste, ensure consistent product quality, and ultimately contribute to a more profitable and efficient production environment.
Conclusion
Industrial batching scales are more than just weighing equipment; they are powerful tools for optimizing production efficiency, minimizing waste, and ensuring consistent product quality. By incorporating these systems into your production line, you can gain a significant competitive edge and achieve operational excellence. Consider investing in industrial batching scales and experience the difference for yourself.