How Does Automatic Weighbridge Work?
In this fast-paced world, efficiency is crucial for industries that rely on cargo transportation. The emergence of automatic weighbridge allows us to simplify the weighing process, saving time and greatly improving efficiency. Let’s take a look at how it works.
What is an Automatic Weighbridge?
First, we must know what is an automatic weighbridge.
An automatic weighbridge is a sophisticated, high-precision weighing system designed to measure the weight of vehicles and their cargo efficiently and accurately without manual intervention. Unlike traditional weighbridges, which require human operators to record weights and manage data, automatic weighbridges leverage advanced technology to streamline the entire process.
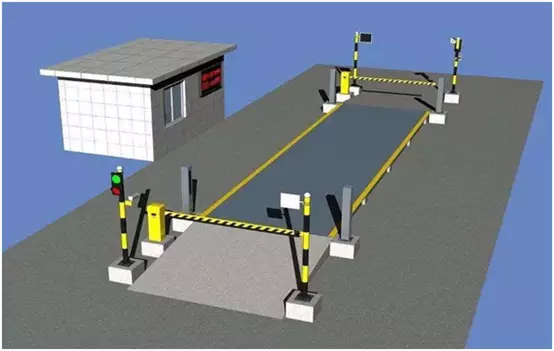
These systems are equipped with automated vehicle identification (AVI) technologies, such as RFID tags and license plate recognition cameras, which identify and log vehicles as they approach the weighbridge. The integration of sensors, load cells, and software allows for real-time data processing, ensuring that weights are recorded instantly and accurately.
Automatic weighbridges are especially valuable in high-traffic industries like logistics, mining, transportation, and manufacturing, where speed and accuracy are crucial. By eliminating human error and reducing labor costs, these systems enhance operational efficiency, provide reliable data for regulatory compliance, and improve overall productivity.
Key Components of an Automatic Weighbridge
Automatic weighbridges are changing how we measure weight. Behind the scenes, various components work together seamlessly. Let’s explore their crucial roles:
- Weighbridge Deck: This is the robust platform that bears the brunt of the weight. It’s typically constructed from strong, reinforced concrete or modular steel decks, designed to withstand the heavy loads of trucks and other vehicles. The surface is often textured to prevent slippage and ensure safe passage.
- Load Cells: These are the heart of the weighbridge system. Strategically positioned beneath the deck, these high-precision sensors convert the weight of the vehicle into an electrical signal. They come in various capacities and configurations to suit different weighbridge sizes and weight ranges. There are several types of load cells commonly used, each with its advantages:
- Shear Beam Load Cells: These are known for their compact size and affordability, making them suitable for many applications.
Bending Beam Load Cells: Offering high accuracy and stability, they are ideal for heavy-duty weighbridges.
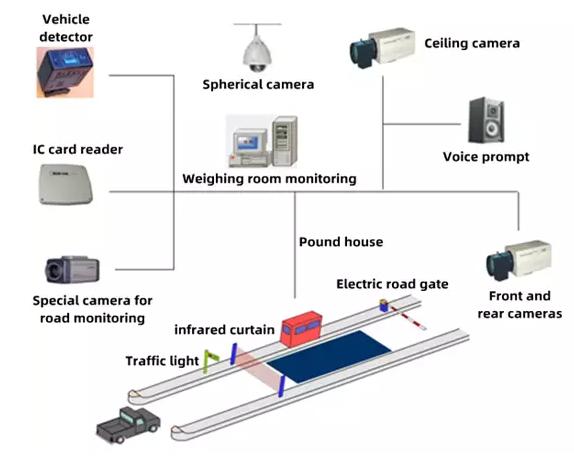
Canister Load Cells: These are known for their durability and resistance to harsh environments.
- Control System (Weighbridge Indicator): This acts as the brain of the operation. It receives the electrical signals from the load cells, converts them into weight readings, and displays them on a digital screen. Modern control systems are often housed in weatherproof enclosures and boast a range of features:
- Data Processing and Recording: The system can perform calculations like axle weights and gross vehicle weight, and store the data along with timestamps and vehicle identification for future reference.
- Connectivity: Many systems offer options for connecting to printers for weight tickets, or to networks for centralized data management.
- User Interface: The user interface should be intuitive and easy to navigate, allowing for quick weight retrieval and configuration changes.
- Automatic Vehicle Identification (AVI): This technology eliminates the need for manual data entry, saving time and minimizing errors. There are two main AVI technologies used:
- License Plate Recognition (LPR) Cameras: These high-resolution cameras capture images of license plates as vehicles enter the weighbridge. Using advanced software, the system automatically identifies the vehicle and retrieves relevant information.
- Radio Frequency Identification (RFID) Tags: These tags are attached to vehicles and emit a radio signal when they come within range of the weighbridge reader. This allows for quick and contactless identification.
- Traffic Control System: This system ensures a smooth flow of traffic and promotes safety around the weighbridge. It typically includes:
- Traffic Lights: These guide vehicles onto, off of, and through the weighbridge in a controlled manner.
- Barriers: These prevent unauthorized access and ensure vehicles are properly positioned for weighing.
- Signage: Clear signage provides drivers with instructions and weight limitations.
By working together seamlessly, these key components transform a simple platform into a powerful tool for efficient and accurate weight measurement.
How Does an Automatic Weighbridge Work?
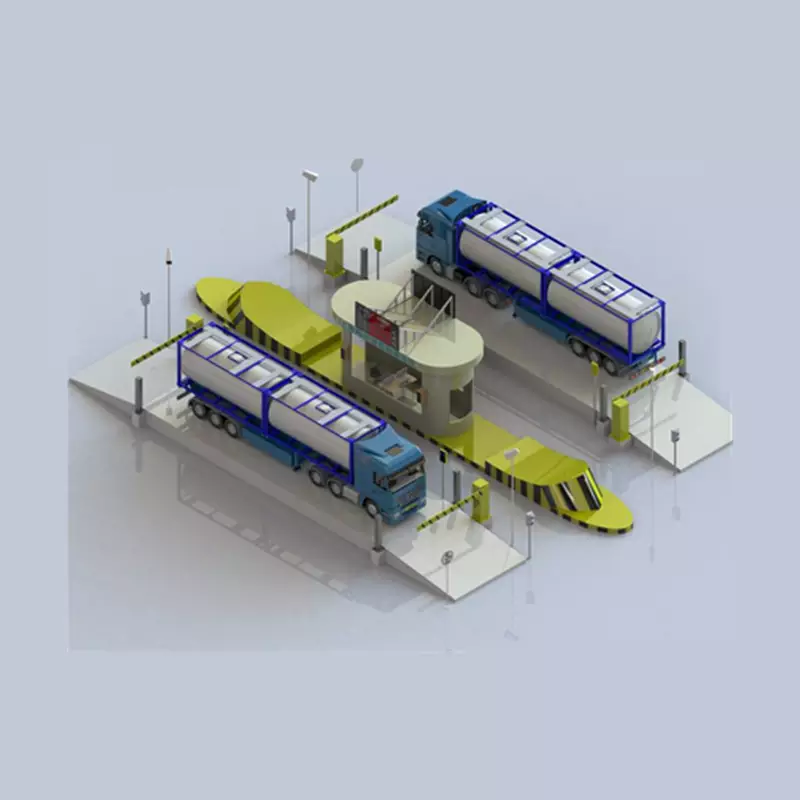
Automatic weighbridges make industrial processes much more efficient. They transform the act of weight measurement into a symphony of efficient data collection. Let’s delve deeper into the meticulously choreographed sequence that underpins this remarkable technology.
- Initiating the Weighing Sequence:
Sensor Activation: As a vehicle approaches the weighbridge, strategically placed in-ground loop detectors or other sensors sense its presence. This triggers a cascade of automated actions.
Traffic Light Management: The traffic light system seamlessly switches from red to green, granting the vehicle safe passage onto the weighbridge deck. - Automatic Vehicle Identification (AVI):
Automatic weighbridges leverage two primary AVI technologies for swift and accurate identification:
License Plate Recognition (LPR) System: High-resolution cameras capture a clear image of the vehicle’s license plate as it enters the designated zone. Advanced character recognition software then extracts the plate number, meticulously searches a database of authorized vehicles, and retrieves pertinent information such as vehicle classification, weight limitations, and associated accounts.
Radio Frequency Identification (RFID) Technology: Vehicles equipped with RFID tags are effortlessly identified as they pass by a strategically positioned reader near the weighbridge entrance. The reader transmits a radio signal, prompting the tag to transmit its unique identification code. The system then retrieves pre-programmed data linked to the specific RFID tag. - The Weighing Process:
The vehicle proceeds onto the weighbridge deck, and the true essence of the system unfolds:
Load Cell Activation: The vehicle’s weight exerts a precisely measured pressure on the weighbridge deck, meticulously registered by the load cells positioned beneath.
Signal Conversion: Each load cell transforms the physical pressure into a corresponding electrical signal with unwavering accuracy.
Data Transmission: The electrical signals from all the load cells are transmitted seamlessly to the control system, forming the foundation for weight determination. - Data Processing and Weight Calculation:
The control system takes center stage, orchestrating the data analysis and weight calculation:
Signal Analysis: The control system meticulously receives the data stream from the load cells and converts it into digital weight readings with the utmost precision.
Advanced Weight Calculations: The system can perform sophisticated calculations, determining individual axle weights, gross vehicle weight, and even weight distribution across axles. This provides invaluable insights for tasks such as ensuring compliance with weight regulations or calculating freight costs with pinpoint accuracy.
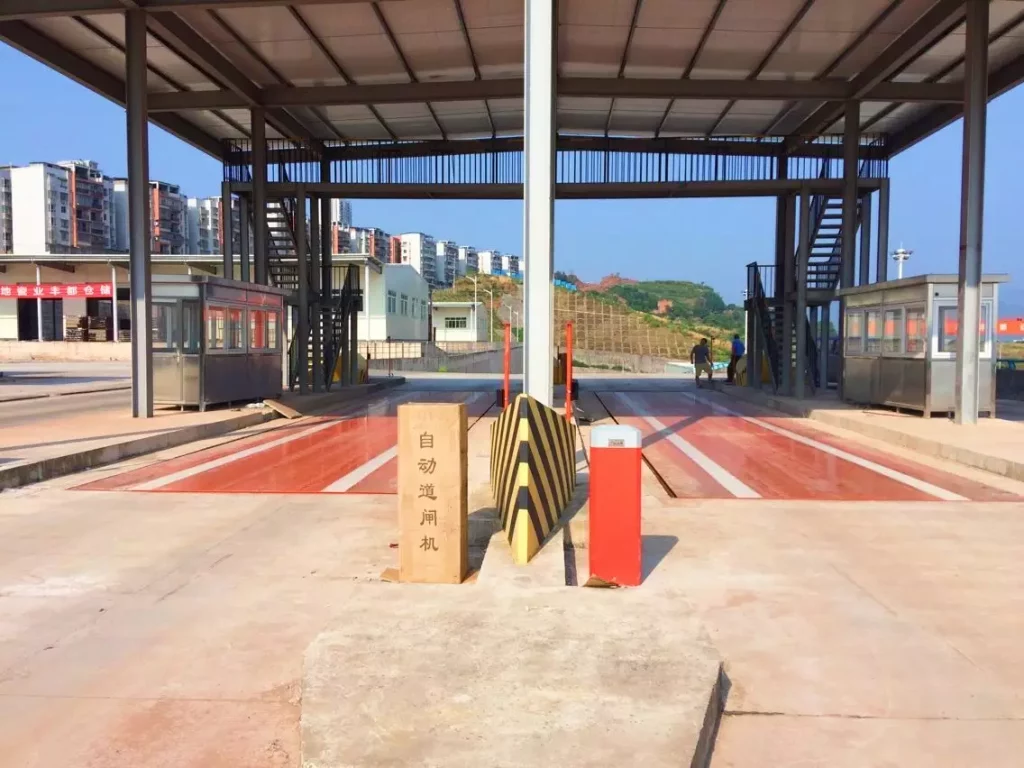
- Weight Display and Recording:
Weight Display: The processed weight information is displayed on a large, high-resolution digital screen clearly visible to the driver. This instantaneous feedback eliminates the need for manual recording and ensures transparency.
Data Recording: The weight data, along with the corresponding timestamp and vehicle identification details retrieved from the AVI system, are automatically stored in the weighbridge’s internal memory or a connected database. This creates a permanent and auditable record for future reference, reporting, and in-depth analysis. - Efficient Exit:
Once the weighing process is complete and the weight is displayed, the traffic light system efficiently signals the driver to proceed off the weighbridge. This ensures a smooth flow of traffic and minimizes wait times, optimizing overall operational efficiency.
By meticulously choreographing these steps, automatic weighbridges stand as a testament to modern engineering ingenuity. They significantly enhance efficiency, minimize human error, and empower businesses with valuable data to make informed decisions and optimize their operations.
How to Choose A Weighbridge Manufacturer
Selecting the right weighbridge manufacturer is crucial for ensuring the efficiency and longevity of your weighing system. Here are key factors to consider:
- Experience and Reputation: Choose manufacturers with extensive industry experience and positive customer reviews. A solid track record indicates a deep understanding of sector-specific needs and reliable products.
- Product Quality: Ensure weighbridge components, like platforms and load cells, are made from high-quality materials such as steel or concrete. Advanced technology in load cells and indicators enhances accuracy and efficiency, so look for manufacturers that prioritize innovation.
- Customization Options: Opt for manufacturers that offer customization to meet your specific operational requirements. Flexibility in design, including platform sizes and software features, is essential for maximizing efficiency and productivity.
- Support and Service: Comprehensive installation services, staff training, and ongoing maintenance support are vital. A strong warranty also indicates confidence in the product’s quality and reliability.
- Cost and Value: Balance cost with quality and longevity. Consider the total cost of ownership, including installation, maintenance, and operational costs. A higher initial investment may lead to long-term savings.
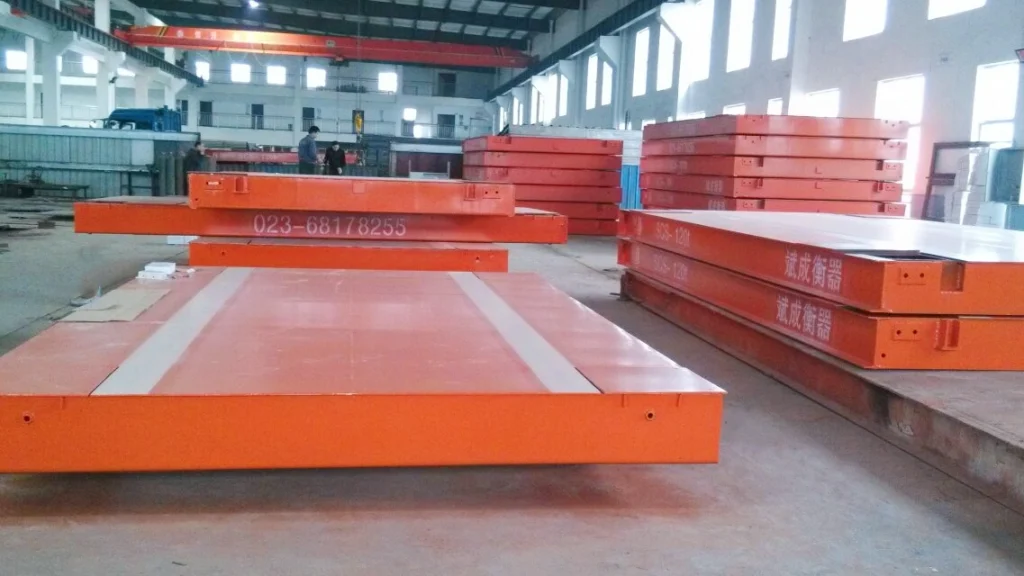
Bincen is a trusted weighbridge manufacturer known for its extensive experience and commitment to quality. With a strong reputation built on customer satisfaction and innovative products, Bincen offers high-quality weighbridges made from durable materials and equipped with advanced technology. They provide customized solutions to meet specific operational needs, ensuring flexibility and efficiency. Bincen also excels in support and service, offering comprehensive installation, training, and maintenance services.
Conclusion
Automatic weighbridges represent a significant advancement in weighing technology, offering accuracy, efficiency, and cost savings over traditional systems. By understanding their key components, how they operate, and the advantages they offer, businesses can make informed decisions about integrating automatic weighbridges into their operations. Choosing Bincen as your weighbridge manufacturer ensures that you receive a reliable and effective system tailored to your needs. Embrace the benefits of automatic weighbridges to enhance your operational efficiency and stay ahead in a competitive market.