How to Choose an Industrial Weighing Scale?
Industrial weighing scales across various industries, including manufacturing, logistics, food processing, and pharmaceuticals. They are crucial for ensuring accuracy, efficiency, and adherence to quality standards. Given the wide array of scales available, selecting the right one can be challenging. This guide will help you navigate the complexities of industrial weighing scale selection, ensuring you choose the optimal solution for your specific needs.
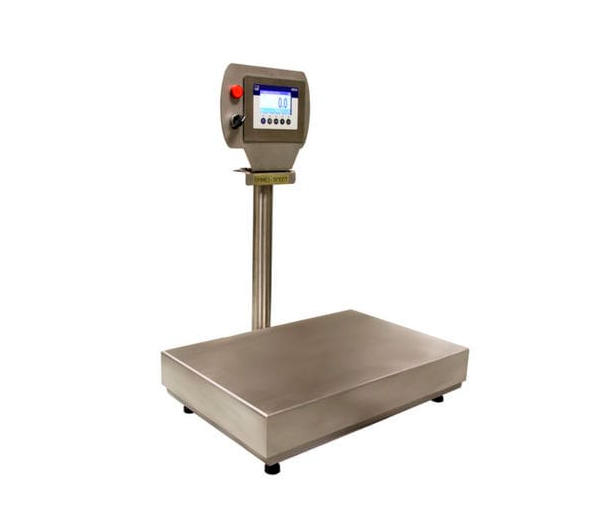
Key Factors to Consider When Choosing an Industrial Weighing Scale
Factor 1: Capacity
- Maximum Load: Determine the heaviest weight the scale will need to measure.
- Future-Proofing: Consider potential future weight increases and select a scale with a capacity that can accommodate future needs.
Factor 2: Readability
- Clear Display: Ensure the scale has a clear and easy-to-read display, especially in low-light conditions or from a distance.
- Precision Level: Choose a scale with a suitable level of precision. High-precision scales are ideal for applications requiring accurate measurements, while lower-precision scales are suitable for general-purpose weighing.
Factor 3: Accuracy
- Calibration: Assess the scale’s calibration requirements and frequency. Regular calibration ensures accurate and reliable measurements.
- Environmental Factors: Consider the impact of temperature, humidity, and vibration on the scale’s accuracy. Select a scale that is designed to minimize the effects of these factors.
Factor 4: Durability
- Harsh Environments: Choose a scale that is built to withstand harsh industrial environments, including exposure to dust, dirt, moisture, and temperature extremes.
- Sturdy Construction: Look for scales with robust construction and durable materials to ensure long-lasting performance.
Factor 5: Features
- Essential Features: Identify specific features that are essential for your application, such as data logging, printing, or connectivity options.
- Automation and Integration: Consider the level of automation and integration required. Some scales can be integrated with other systems, such as inventory management software or production control systems.
Factor 6: Compliance
- Industry Standards: Ensure the scale complies with relevant industry standards and regulations, such as OIML (International Organization of Legal Metrology) standards.
- Legal-for-Trade: If the scale will be used for commercial transactions, it must be legal-for-trade certified. This ensures that the scale meets specific accuracy and reliability requirements.
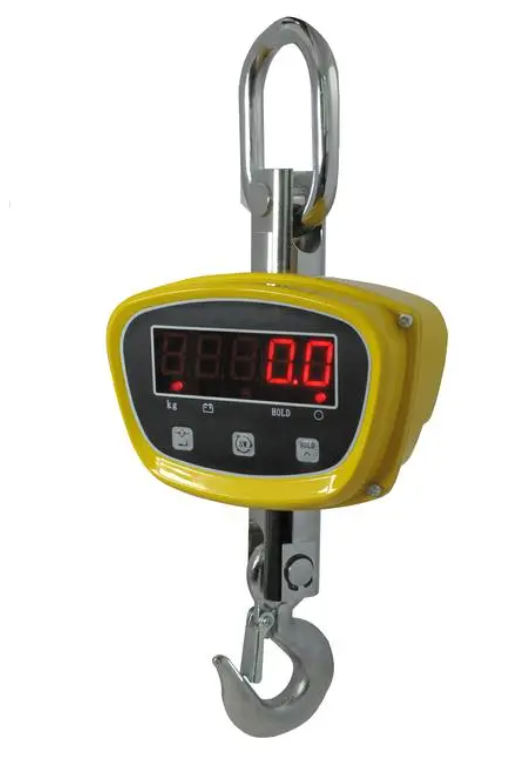
Types of Industrial Weighing Scales
Platform Scales
Platform scales are versatile weighing solutions that come in various sizes and configurations. They are widely used in industries such as manufacturing, warehousing, and logistics. There are types of platform scales:
- Bench Scales: Compact and portable, bench scales are ideal for weighing smaller items in laboratory or workshop settings.
- Floor Scales: Larger and more robust, floor scales are designed for weighing heavier loads, such as pallets, boxes, and crates.
- Pallet Scales: Specifically designed for weighing pallets, these scales are often integrated into warehouse systems for efficient inventory management.
Crane Scales
Crane scales are essential tools for weighing heavy loads in industrial settings. They are typically attached to cranes or hoists and used to measure the weight of materials being lifted or moved. Crane scales are critical for ensuring safe and efficient operations, preventing overloading of equipment and potential accidents. There are key considerations for crane scales:
- Safety: Crane scales must be regularly calibrated and inspected to ensure accurate and reliable measurements.
- Capacity: The scale’s capacity should be sufficient to handle the heaviest loads that will be lifted.
- Environmental Factors: The scale should be designed to withstand harsh industrial environments, including exposure to moisture, dust, and extreme temperatures.
Counterbalance Scales
Counterbalance scales are mechanical weighing devices that use a counterweight to balance the weight of the object being measured. They are relatively simple and reliable, but their accuracy can be affected by factors such as temperature and humidity. While counterbalance scales are still used in some industries, digital scales have largely replaced them due to their superior accuracy, precision, and ease of use.
Digital Weighing Scales
Digital weighing scales offer numerous advantages over analog scales, including:
- High Accuracy: Digital scales provide precise measurements, reducing errors and improving efficiency.
- Data Logging: Many digital scales have built-in data logging capabilities, allowing users to track and analyze weighing data.
- Connectivity: Digital scales can be connected to computers and other devices, enabling remote monitoring and control.
- User-Friendly Interfaces: Digital scales often have intuitive user interfaces, making them easy to operate.
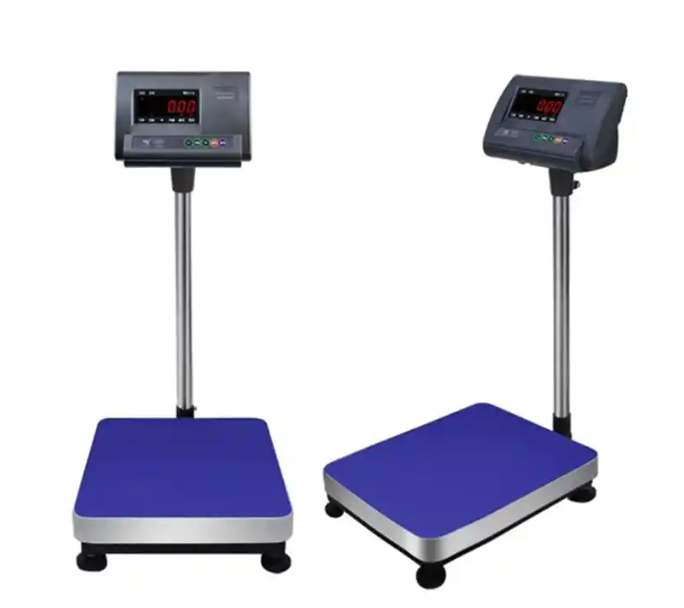
Maintenance and Calibration of Industrial Weighing Scales
Industrial weighing scales are essential tools for accurate measurement in various industries. Regular maintenance and calibration are crucial to ensure their reliability and precision. This article will delve into the importance, frequency, and best practices for maintaining and calibrating industrial weighing scales.
Importance of Maintenance and Calibration
- Accuracy: Regular maintenance and calibration guarantee that your scales provide accurate measurements, preventing errors and ensuring product quality.
- Compliance: Many industries have strict regulations regarding weighing equipment accuracy. Proper maintenance and calibration help you comply with these standards.
- Efficiency: Well-maintained scales operate smoothly, reducing downtime and increasing productivity.
- Cost-Effectiveness: Preventive maintenance can identify and address potential issues before they escalate, saving you money on repairs and replacements.
Maintenance Schedule
A comprehensive maintenance schedule should be tailored to your specific scale type and usage frequency. However, some general guidelines include:
Daily Inspection | Visually inspect the scale for damage, dirt, or debris. Clean the scale and its components as needed.Check for any unusual noises or vibrations. |
Weekly Inspection | Verify the scale’s level and adjust if necessary.Check the battery level (for battery-powered scales).Test the scale’s functionality with known weights. |
Monthly Inspection | Thoroughly clean the scale and its components.Lubricate moving parts as recommended by the manufacturer. Perform a more detailed functional test, including checking zero point stability and linearity. |
Annual Calibration | Schedule professional calibration by a certified technician.This involves adjusting the scale’s internal settings to ensure accurate measurements. A calibration certificate will be issued, documenting the scale’s performance. |
Best Practices for Maintenance and Calibration | Follow Manufacturer’s Guidelines: Always refer to the manufacturer’s instructions for specific maintenance and calibration procedures.Use High-Quality Cleaning Agents: Avoid harsh chemicals that could damage the scale’s components. Train Your Staff: Ensure that your employees are trained on proper scale handling, cleaning, and basic troubleshooting.Keep Detailed Records: Maintain a log of all maintenance and calibration activities, including dates, technician information, and any issues identified. Choose a Reputable Calibration Service: Select a calibration provider that is accredited and uses traceable standards. |
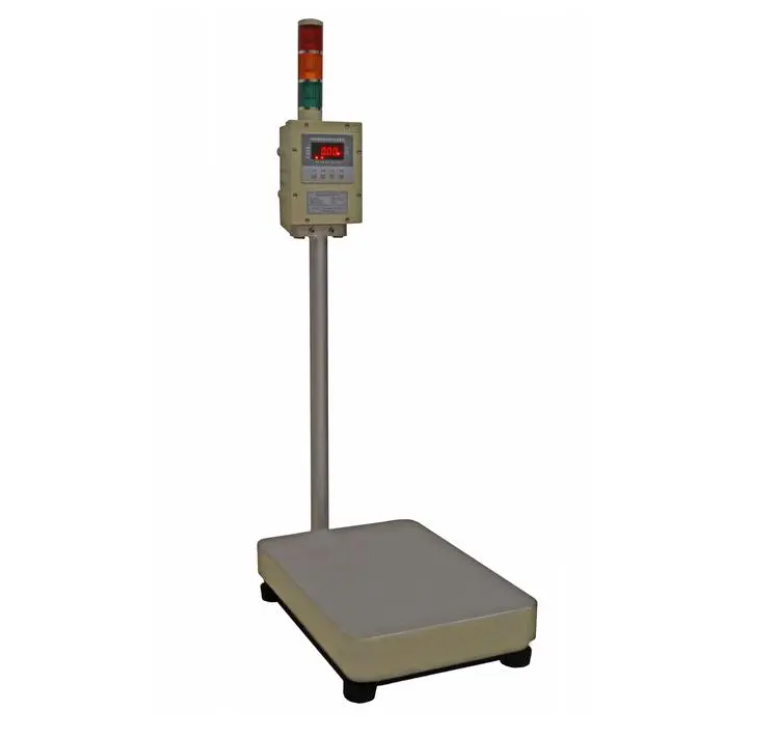
Choosing the Right Industrial Scale
Selecting the right industrial weighing scale is paramount to ensuring accurate measurements and efficient operations. Key factors to consider include the scale’s capacity, readability, accuracy, durability, and additional features. It’s essential to choose a scale that not only meets your specific needs but also complies with relevant industry standards. For complex applications or customized solutions, consulting with industrial scale manufacturer Bincen can provide valuable guidance and help you make informed decisions.