How to Improve Product Quality Control in Manufacturing?
Product quality directly impacts customer satisfaction, brand reputation, and ultimately, a company’s bottom line. This article explores key strategies to enhance product quality control within the manufacturing sector. We will delve into the establishment of a robust quality management system, the importance of strictly controlling the production process, and the critical role of industrial weighing scales in various stages, from material handling to final product inspection. We will also discuss the significance of employee training, feedback mechanisms, and continuous improvement initiatives in achieving and maintaining superior product quality.
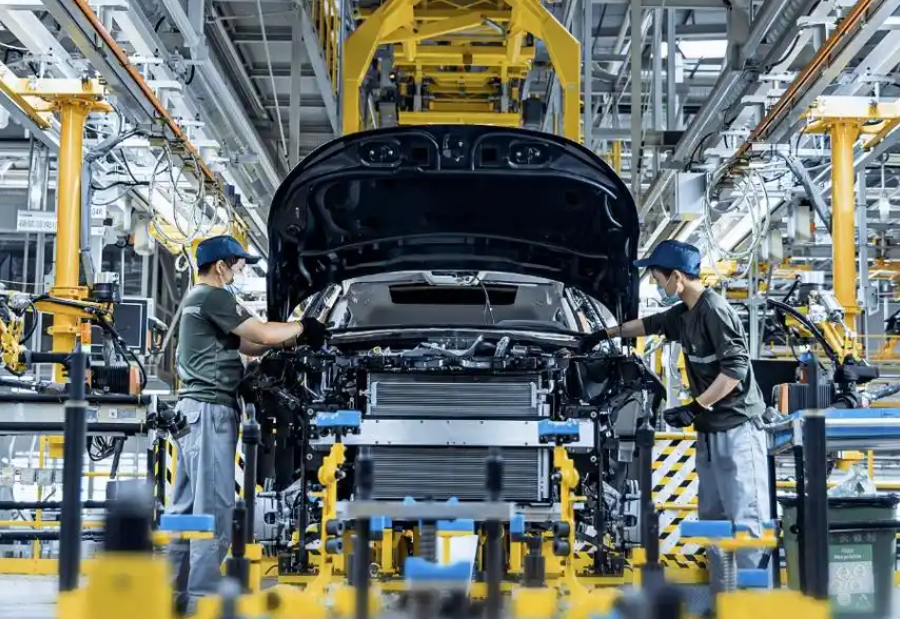
Establish a Quality Management System
Establishing a comprehensive quality management system is fundamental to ensuring product quality. This entails formulating detailed quality standards and inspection specifications. It is necessary to clarify the operational steps and standards for each production link so as to ensure that all workers carry out their tasks in accordance with unified standards.
For example, in a car manufacturing factory, for every part from the engine to the smallest screw, there should be specific quality criteria. The inspection specification should clearly define how to measure the size, hardness, and performance of these parts. Workers are required to strictly follow the standard operating procedures when assembling, welding, or painting these parts to guarantee that each part meets the overall quality requirements of the vehicle.
Strictly Control the Production Process
During the production process, multiple inspection points should be set up to conduct real-time detection on products, so as to detect and solve problems in a timely manner. This includes raw material inspection, process inspection, standardization of operations, and real-time monitoring measures. By doing so, nonconforming products can be ensured that they do not flow into the next production process.
In the electronics manufacturing industry, when producing circuit boards, raw materials such as copper foil, resistors, and capacitors need to be inspected strictly. The thickness of the copper foil, the resistance value of the resistors, and the capacitance value of the capacitors must meet the specified standards. During the process of soldering components onto the circuit board, the operation should be standardized, and real-time monitoring of the soldering quality should be carried out.
Any soldering joints that do not meet the quality requirements, such as cold soldering or short circuit problems, should be detected immediately and corrected to prevent defective circuit boards from entering the subsequent assembly process.
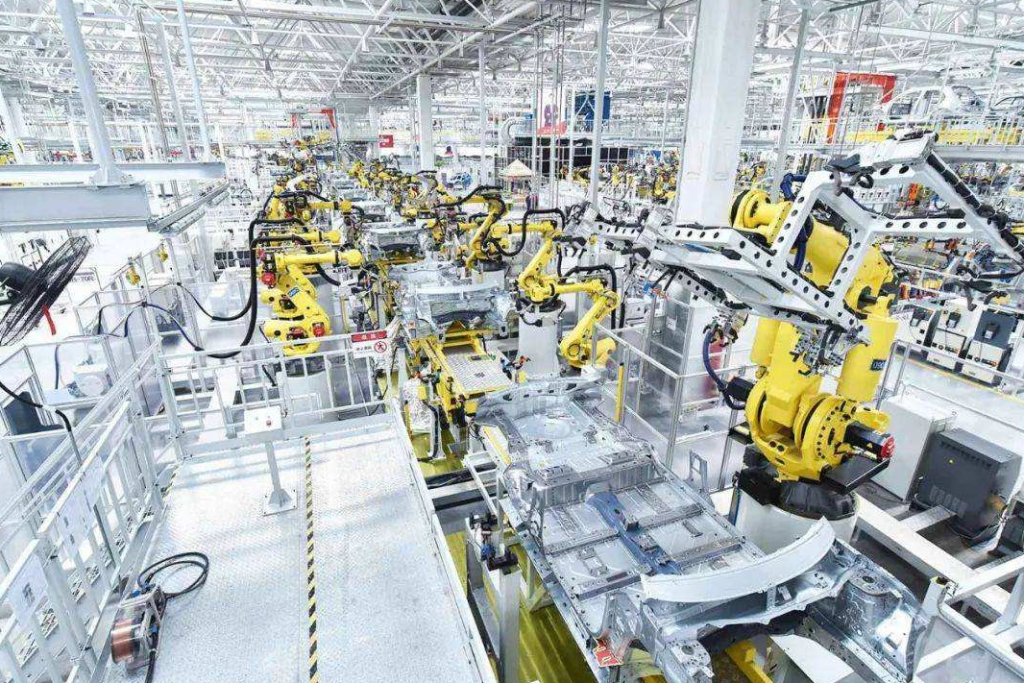
Application of Industrial Weighing Scales
The application of industrial weighing scales in the manufacturing industry is very extensive, mainly including the following aspects:
1. Material Handling on the Production Line
On the production line, industrial electronic weighing scales are widely used for material handling and weighing. For example, in industries such as chemical, food, and pharmaceutical industries, the addition of raw materials, the measurement of semi-finished products, and the weighing of finished products all rely on electronic weighing scales. Through the electronic weighing scale, the operator can quickly and accurately know the weight of the material, thereby ensuring the stability of production and the quality of products.
2. Warehouse Management
Warehouse is an important part of industrial production, and the electronic weighing scale plays a vital role in it. Warehouse managers can use handheld electronic weighing scales to quickly and accurately record the quantity and type of goods in and out of the warehouse.
In addition, through combination with management systems such as ERP, the electronic weighing scale can also realize real-time inventory management, effectively reducing inventory costs and improving the operational efficiency of the warehouse.
3. Product Quality Control
The industrial electronic weighing scale is one of the important tools for product quality control. During the production process, operators can use the weighing scale to monitor the addition of materials in key processes, ensuring that the weight parameters in the production process meet the process requirements.
This can not only improve the consistency of product quality but also avoid waste caused by excessive or insufficient addition of materials. Moreover, through combination with automated equipment, the weighing scale can also realize the automation and intelligence of the production process.
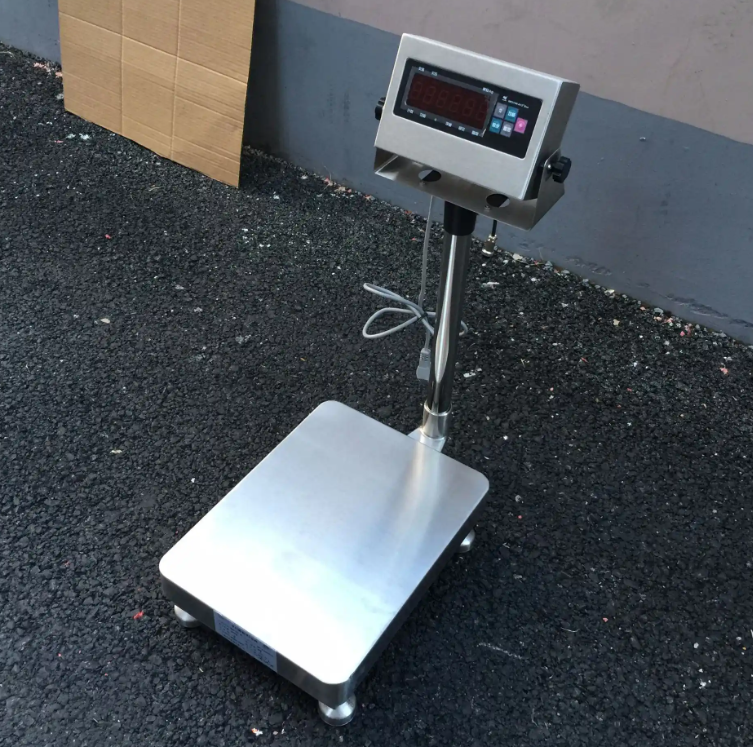
Employee Training and Consciousness Enhancement
Employees are crucial assets in manufacturing enterprises, and their professional qualities and skill levels directly influence product quality. Therefore, manufacturing enterprises should strengthen employees’ skill training and quality-oriented education, enhance their quality awareness, and make them understand that quality is the cornerstone of an enterprise’s survival and development so that they can consciously improve the quality of their work.
For example, manufacturing enterprises can organize regular training courses on production techniques and quality control for employees. These courses can cover new manufacturing technologies, advanced quality inspection methods, and safety production regulations.
Establishment of Feedback and Traceability Mechanisms
Establish an effective feedback mechanism to timely feedback and handle product defects, preventing problems from getting worse. Meanwhile, establish a product traceability system to record and manage every link in the production process, ensuring that when quality problems occur, the source can be quickly traced and the problems can be solved.
For instance, in the food manufacturing industry, for each batch of products, relevant information such as raw material sources, production dates, production lines, and quality inspection results should be recorded. When a food safety problem is found, through the traceability system, it can be determined which batch of raw materials is the problem source, which production line has potential risks, and which quality inspection link may have missed the defect.
Continuous Improvement and Optimization
Encourage employees to put forward improvement opinions and suggestions, continuously optimize production processes and operation methods, and improve product quality and production efficiency. Regularly supervise and evaluate the quality management system, and discover and improve problems in a timely manner.
For example, enterprises can set up an incentive mechanism for employees’ improvement suggestions. If an employee’s suggestion can effectively reduce production costs, improve product quality, or increase production efficiency, the enterprise will give corresponding rewards.
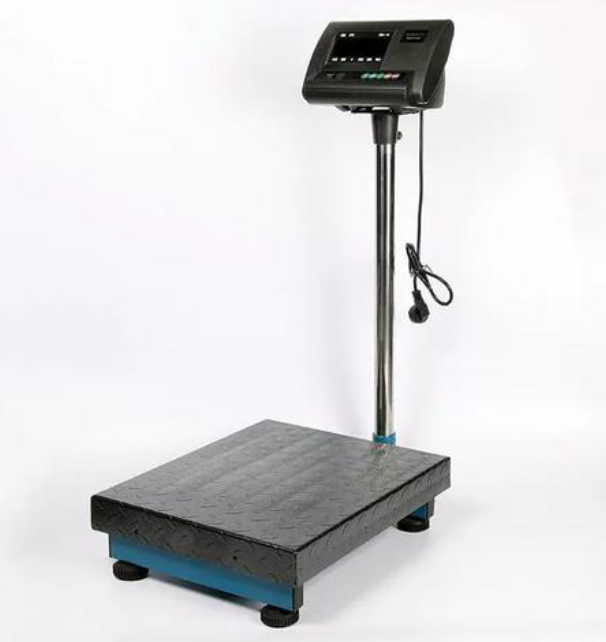
Unlocking Quality Success
By implementing a comprehensive approach to product quality control, manufacturers can significantly enhance their competitiveness, reduce costs associated with defects and rework, and build lasting customer relationships. This involves a multi-faceted strategy encompassing a robust QMS, stringent process control, effective utilization of industrial weighing scales, and a strong emphasis on employee training and continuous improvement. Embrace these principles and foster a culture of quality within the organization, and manufacturers can ensure consistent delivery of high-quality products that meet and exceed customer expectations in today’s demanding market.