Key Factors & Best Practices for Belt Scales Accuracy
The accuracy of belt scales can be compromised by various factors, leading to errors in production processes and financial losses. To ensure reliable and accurate measurements, it is crucial to understand the key factors affecting belt scale performance and implement effective maintenance and calibration strategies. Professional belt scale supplier Bincen will give the critical factors that influence belt weigh scale accuracy, including material properties, installation and alignment, environmental conditions, and belt speed variations. Additionally, we will discuss the importance of regular calibration and maintenance in preserving the scale’s accuracy and reliability. By understanding these factors and implementing best practices, you can optimize the performance of your belt scale and enhance the efficiency and accuracy of your operations.
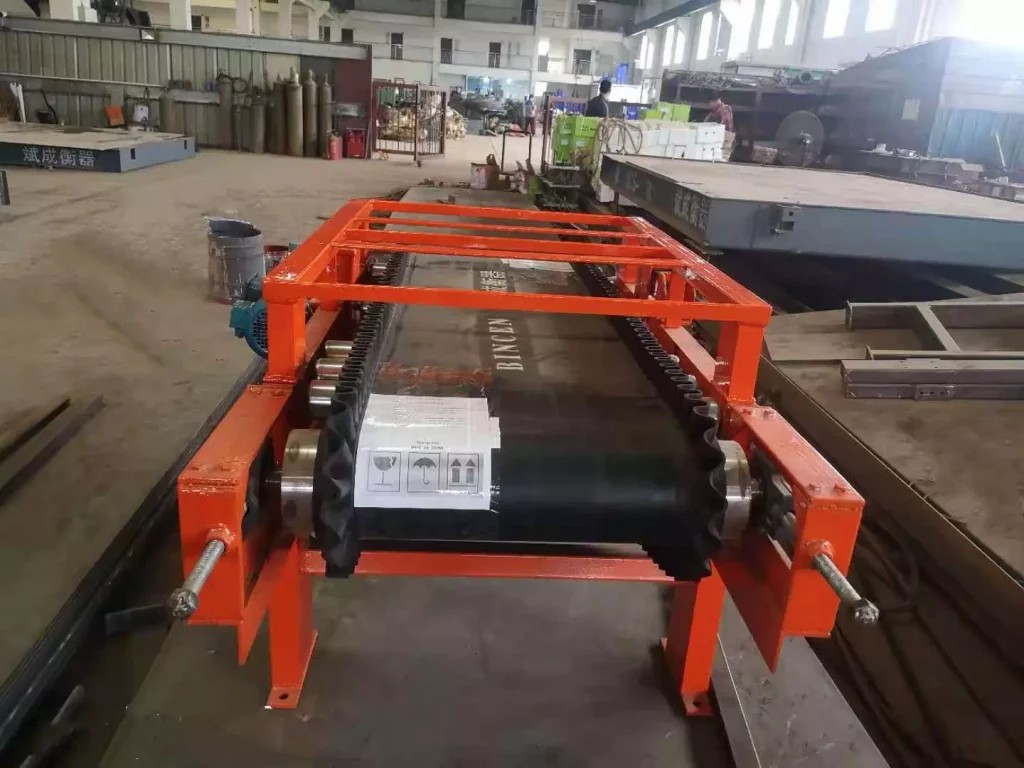
What Factors Affect Belt Scale Accuracy?
Belt scales are precision instruments used to measure the mass flow rate of materials conveyed on a belt. Their accuracy is crucial in various industries, from mining and manufacturing to food processing and pharmaceuticals. Here are some key factors that can influence belt weigh scales accuracy:
1. Belt Speed Variations
Belt speed variations significantly affect belt scale accuracy because they directly influence the mass flow rate calculation. The mass flow rate is determined by multiplying the weight of material on the belt by its speed. If the belt speed fluctuates, even slightly, it can lead to errors in the calculated mass flow rate. Additionally, inconsistent belt speeds can cause material buildup or slippage, further impacting the accuracy of the scale.
2. Material Properties
Material properties play a crucial role in belt scale accuracy because they directly influence the bulk density and flow characteristics of the material being conveyed. Different materials have varying densities, particle sizes, and moisture contents, which can affect their weight and how they interact with the belt. For example, a material with a higher density will have a greater mass per unit volume, while a material with a larger particle size may have a lower bulk density. These variations can impact the scale’s ability to accurately measure the weight of the material and calculate the mass flow rate.
3. Installation and Alignment
Installation and alignment are critical factors affecting belt scale accuracy because they directly influence the scale’s ability to measure weight and speed accurately. Improper installation can lead to misalignment of the load cells, which are responsible for measuring the weight of the material on the belt. Misalignment can cause inaccurate weight readings. Additionally, if the belt is not properly aligned, it can cause material buildup or slippage, which can further affect the scale’s accuracy. Proper installation and alignment ensure that the scale operates as intended, providing accurate and reliable mass flow rate measurements.
4. Environmental Conditions
Environmental conditions can significantly impact belt scale accuracy due to their influence on the scale’s components and the material being conveyed. Extreme temperatures can affect the scale’s calibration and the material’s properties. High humidity can lead to corrosion and other issues, affecting the scale’s functionality. Vibrations can interfere with the scale’s measurements and cause inaccuracies. Exposure to corrosive substances can damage the scale’s components.
5. Maintenance and Calibration
Maintenance and calibration are critical factors affecting belt weigh scale accuracy because they help to prevent and address issues that can lead to inaccuracies. Regular maintenance ensures that the scale’s components are in good working condition and free from damage or wear. This includes cleaning the belt and rollers, inspecting and tightening bolts and connections, and checking the load cells and speed sensors for proper functioning. Belt scale calibration ensures that the scale is providing accurate measurements by verifying and adjusting its settings. Neglecting maintenance and calibration can result in gradual deterioration of the scale’s performance, leading to inaccurate measurements and potential process inefficiencies.
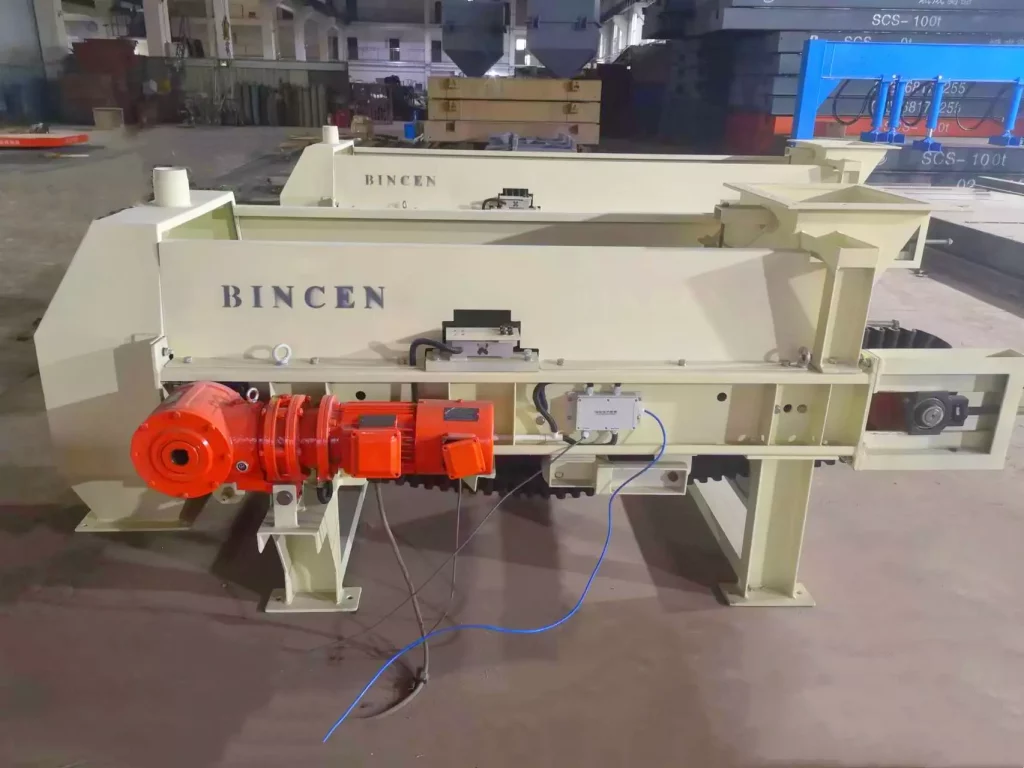
How Often Should a Belt Scale Be Calibrated?
Factors Influence the Frequency of a Belt Scale
- Material Properties: Materials with varying densities, particle sizes, and moisture contents can affect the scale’s accuracy over time. If you’re handling materials that are particularly susceptible to changes in these properties, more frequent calibration may be necessary.
- Operating Conditions: Harsh operating environments, such as extreme temperatures, high humidity, or exposure to corrosive substances, can accelerate wear and tear on the scale’s components. In such cases, more frequent calibrations are recommended to ensure continued accuracy.
- Regulatory Requirements: Many industries have specific regulations regarding the frequency of calibration for weighing and measuring equipment. Compliance with these regulations is essential to avoid penalties and maintain product quality.
- Historical Data: Analyzing historical data from previous calibrations can help identify trends and determine if the current calibration frequency is adequate. If you notice significant deviations or increasing errors over time, it may be necessary to increase the belt scale calibration frequency.
General Recommendations
While the specific calibration frequency may vary, a common guideline is to perform annual or semi-annual calibrations for most belt scale applications. However, it’s important to consider the factors mentioned above and adjust the calibration schedule accordingly.
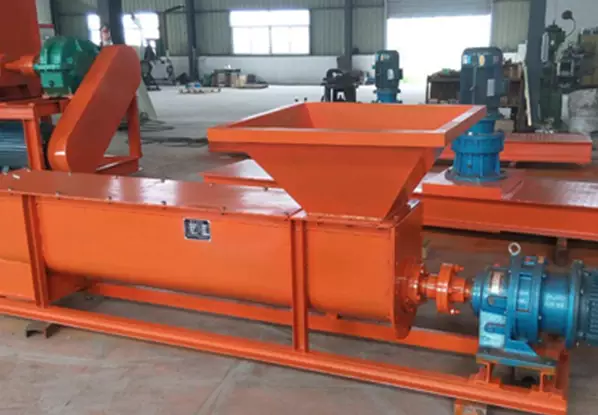
How Can Regular Maintenance Improve Belt Scale Accuracy?
Regular maintenance is crucial for ensuring the accuracy and reliability of conveyor belt scales. Here’s a breakdown of how each maintenance task contributes to improved performance:
- Clean the belt and rollers to prevent material buildup. Material buildup on the belt and rollers can interfere with the scale’s ability to accurately measure weight. Buildup can cause uneven weight distribution and affect the belt’s speed, leading to inaccurate mass flow rate calculations. Use appropriate cleaning methods, such as brushes, scrapers, or compressed air, to remove material buildup without damaging the belt or rollers.
- Inspect and tighten bolts and connections. Loose bolts and connections can compromise the scale’s structural integrity and lead to misalignment or vibrations. These factors can affect the accuracy of weight measurements. Conduct regular inspections to identify and tighten any loose bolts or connections. This helps maintain the scale’s structural stability and ensures accurate measurements.
- Check the load cell for damage or misalignment. Load cells are critical components for measuring the weight of material on the belt. Damage or misalignment can lead to inaccurate weight readings. Conduct regular visual inspections to check for any signs of damage, such as cracks, corrosion, or physical deformation. Verify the alignment of the load cells to ensure they are properly positioned and calibrated.
- Verify the speed sensor’s accuracy. The speed sensor is essential for calculating the mass flow rate by measuring the belt’s speed. An inaccurate speed sensor can lead to errors in the mass flow rate calculation. Regularly calibrate the speed sensor to ensure it is providing accurate readings. Perform periodic tests to verify its accuracy and identify any issues.
- Perform routine calibration checks. Calibration involves verifying the scale’s offset (zero point) and span (range of measurement). Regular calibration ensures that the scale is providing accurate measurements across its entire operating range. Calibration is often required by industry regulations to ensure the accuracy of weighing and measuring equipment. The frequency of calibration depends on factors like material properties, operating conditions, and regulatory requirements. Generally, annual or semi-annual calibrations are recommended.
By diligently performing these maintenance tasks, you can significantly improve the accuracy and reliability of your belt scale, leading to better process control and product quality.
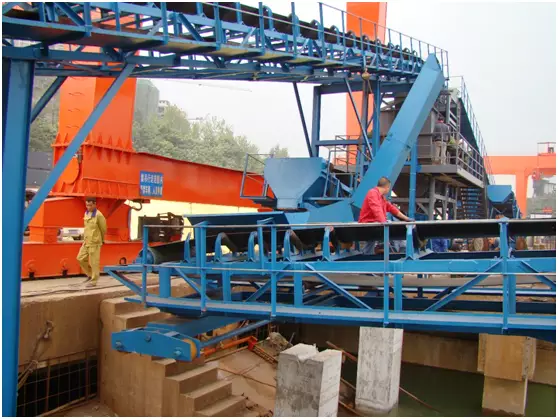
Maintain Your Belt Scale Today
The key factors influencing belt weigh scale performance as well as implementing best practices for maintenance and calibration, can significantly improve the accuracy and reliability of measurements. Regular inspections, cleaning, and calibration are essential for maintaining the scale’s optimal condition. You can increase the efficiency and accuracy of your operations by investing in proper belt scale maintenance and calibration. And if you have any other questions welcome to consult us.