Maximizing Batching Scale Accuracy and Reliability
Accuracy and reliability of batching scales directly impact product quality, process efficiency, and overall operational costs. However, batching scales may experience malfunctions that compromise their performance. This article by Bincen will tell the common issues that can arise with batching scales, including sensor malfunctions, battery problems, zero point drift, accidental key presses, and platform imbalances. It also explores essential factors to consider when using and maintaining these scales, such as environmental conditions, electromagnetic interference, and software updates. By understanding these potential pitfalls and implementing appropriate solutions, you can significantly enhance the accuracy and reliability of your batching scales, ensuring optimal performance in your operations.
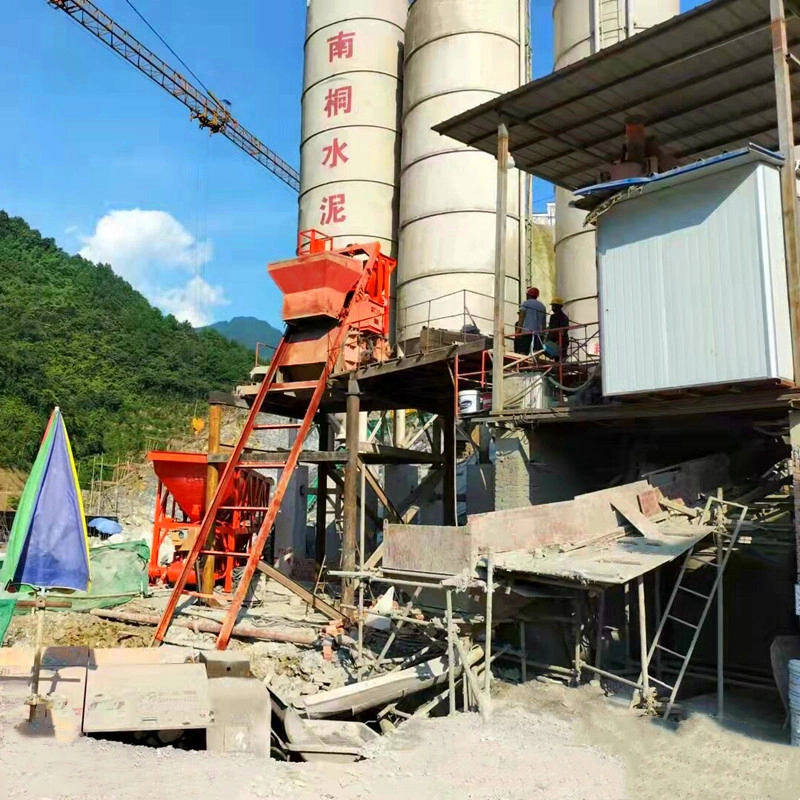
Common Malfunctions of Batching Scales and Their Solutions
1. Sensor Malfunction
The sensor, a critical component of a batching scale, directly feeds back the weight of the material being weighed. When the sensor experiences drift, overload, aging, or other malfunctions, it can lead to inaccurate weighing by the batching scale. This can be caused by factors such as physical damage to the sensor, electrical interference, or simply the sensor reaching the end of its lifespan. Regular calibration and inspection can help identify and address sensor-related issues before they significantly impact weighing accuracy.
2. Insufficient Battery Power
If the batching scale’s battery is running low, it can cause an unstable current, thereby affecting weighing accuracy. In such cases, the battery should be promptly replaced to ensure the equipment operates correctly. Additionally, consider using rechargeable batteries or a direct power source to eliminate the need for frequent battery replacements.
3. Zero Point Drift
Zero point drift is often caused by the unstable placement of the batching scale’s sensor or the bending of the sensor suspension components. Typically, this issue can be resolved by recalibrating the zero point. However, if the drift persists, it may indicate a more serious problem, such as a damaged sensor or a mechanical issue with the scale.
4. Accidental Sensor Keypress
Excessive sensitivity of the sensor keys or frequent key usage can lead to accidental keypresses and erroneous operations, resulting in inaccurate weighing. To address this, consider adjusting the key sensitivity or using a protective cover to prevent accidental activation. In some cases, replacing the sensor keys may be necessary.
5. Unbalanced Weighing Platform
An unbalanced or unstable weighing platform can adversely affect the accuracy of batching. To resolve this issue, the platform should be adjusted and the scale recalibrated. Regular inspections of the platform and its supporting structure can help prevent imbalances from occurring in the first place.
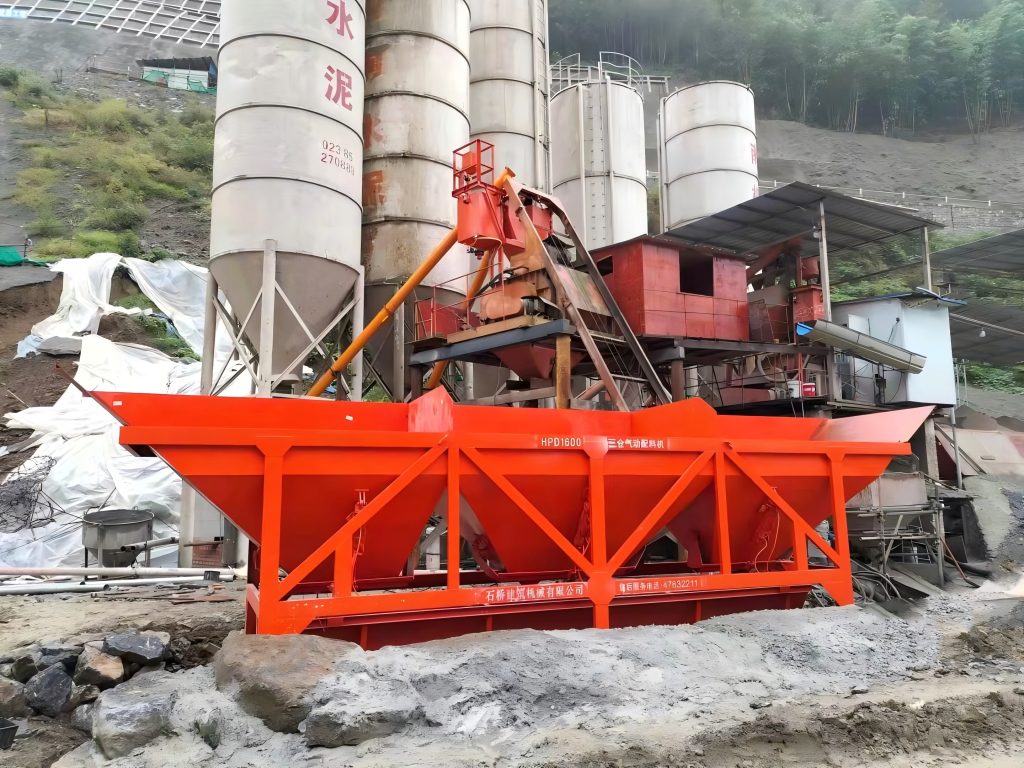
Factors to Consider When Using and Maintaining a Batching Scale
Environmental Factors
- Temperature fluctuations: Extreme temperature variations can cause dimensional changes in the scale’s components, leading to inaccuracies. Maintain a stable operating environment within the recommended temperature range specified by the manufacturer.
- Humidity: High humidity can affect the scale’s electronics and sensors. Ensure the scale is installed in a well-ventilated area to prevent moisture buildup. Consider using dehumidifiers or climate-controlled enclosures if necessary.
- Vibrations: Mechanical vibrations from nearby equipment can disrupt the scale’s readings. Isolate the scale from vibration sources by using vibration-damping pads or mounting it on a stable platform.
Electromagnetic Interference (EMI)
- Nearby equipment: Interference from other electronic devices, such as radio transmitters, motors, or power lines, can cause electrical noise that affects the scale’s sensors.
- Shielding: Consider using shielded cables and enclosures to protect the scale from EMI. Maintain a safe distance between the scale and potential sources of interference.
Software Glitches
- Outdated firmware: Outdated software may contain bugs or vulnerabilities that can impact the scale’s accuracy. Regularly check for and install software updates provided by the manufacturer.
- Data corruption: Power outages or other unexpected events can corrupt data stored on the scale’s internal memory. Implement regular data backup procedures to safeguard your weighing records.
- User errors: Incorrect configuration settings or improper operation can lead to inaccurate results. Ensure that operators are properly trained and follow the manufacturer’s guidelines.
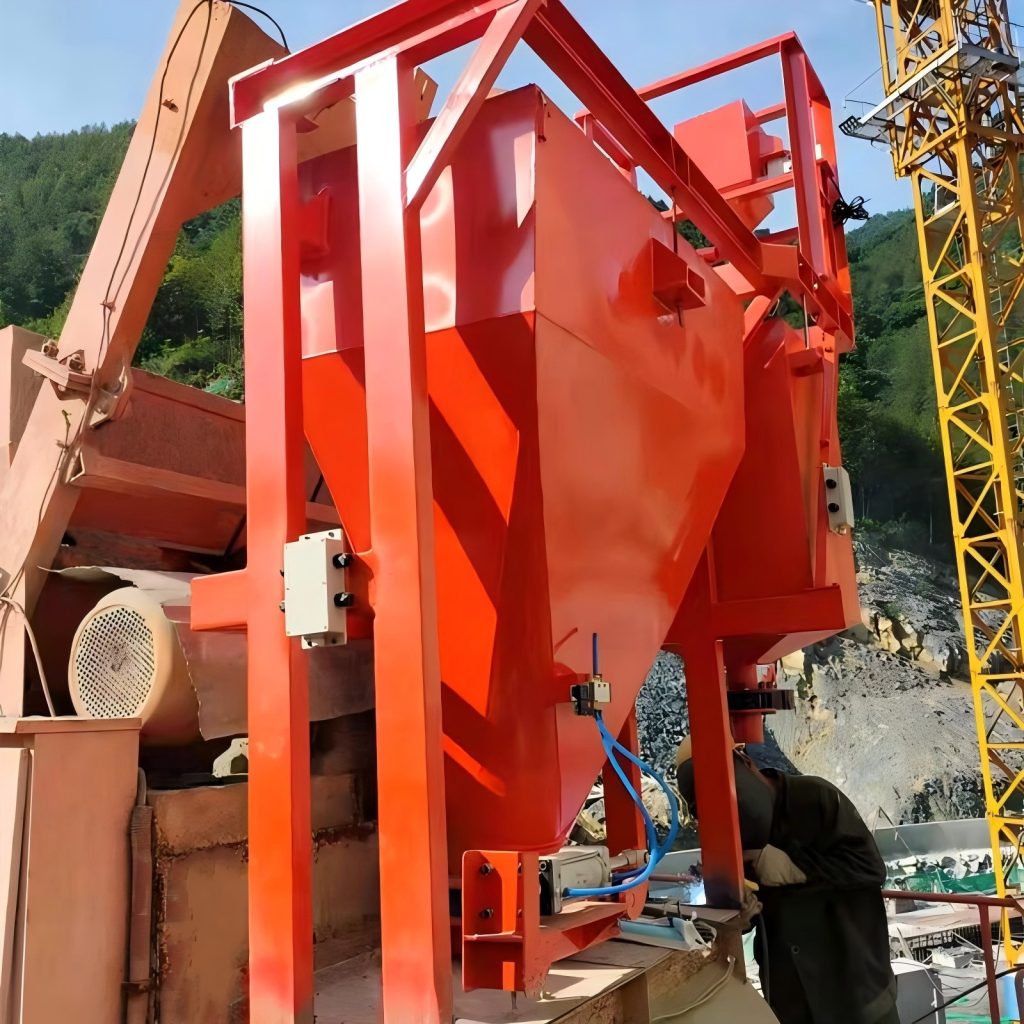
Enhance Your Batching Scale Performance Now!
Addressing common malfunctions, taking environmental factors into account, mitigating electromagnetic interference, and ensuring proper software maintenance can all significantly improve the accuracy and reliability of your batching scales. Regular inspections, calibration, and preventative maintenance can extend the life of critical equipment and reduce downtime. Investing in the proper care and maintenance of your batching scales not only protects your operations from costly errors but also helps to create a more efficient and productive workflow. By following the guidelines outlined in this article and selecting a reputable batching scale supplier like Bincen as your partner, you can maximize the performance of your batching scales and ensure their continued contribution to your business’s success.