Packaging Scales: From Ton Bags to Small Pouches
Efficient and reliable packaging is crucial for businesses of all sizes. But with such a wide array of products, finding the right packaging solution can be a challenge. Bincen lists the specific packaging scales, exploring different types of machines designed to meet your specific needs. We’ll answer key questions about quantitative packaging machines, ton bag packaging machines, double spiral feeding hopperless packaging machines, and 15L small bag powder packaging machines. From delicate spices to heavy-duty fertilizers, discover how these specialized scales can streamline your packaging process and ensure consistent, high-quality results.
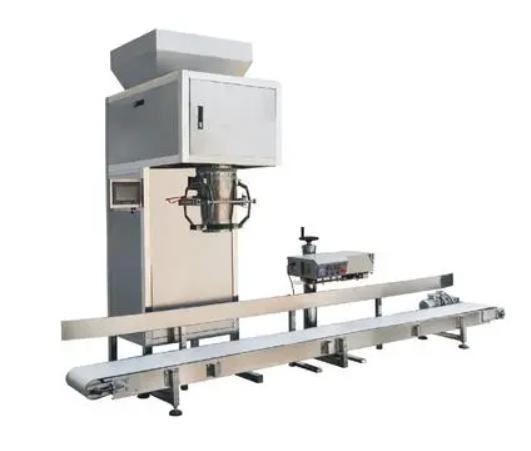
Quantitative Packaging Machines
Suitable Products for Quantitative Packaging Machines
Quantitative Packaging Machines excel at handling granular and free-flowing products. Here’s a breakdown of what these terms mean and why they’re important:
- Granular: These products consist of individual particles that are relatively large enough to be seen and handled individually. Examples include rice, nuts, coffee beans, candy, and pellets.
- Free-flowing: These products move easily without clumping or sticking together. This allows the machine to accurately measure and dispense the product consistently. Examples include dry grains, beans, and some types of hardware like screws and nuts.
Capacity Range of Quantitative Packaging Machines
The capacity of Quantitative Packaging Machines varies depending on the model and its design. Here’s a breakdown of the typical range:
- Low-capacity models: These can handle very small quantities, often starting from a few grams. They are ideal for packaging spices, herbs, or small candy pieces.
- Mid-range models: These are the most common type and can handle from a few hundred grams up to several kilograms per bag. This range covers products like coffee beans, rice, nuts, and pet food.
- High-capacity models: These are designed for heavy-duty applications and can handle large quantities, sometimes exceeding 10 kilograms per bag. They are suitable for packaging products like fertilizer, plastic pellets, and some types of building materials.
The capacity can vary depending on the model, but they typically handle from grams up to several kilograms per bag. Factors Affecting Capacity:
- Number of Weighing Heads: Some machines have multiple weighing heads that operate simultaneously, increasing the overall filling speed and capacity.
- Type of Filling Mechanism: Different mechanisms like volumetric cups, auger fillers, or weigh belts can have different capacity limitations.
- Product Density: Denser products require smaller volumes to reach the same weight compared to lighter products.
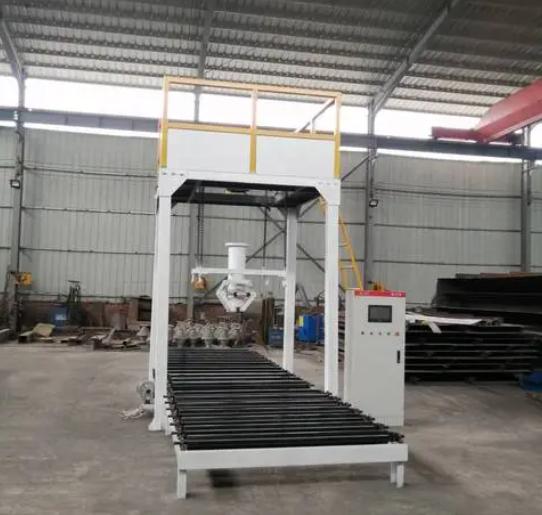
Ton Bag Packaging Machines
Applications of Ton Bag Packaging Machines
Ton bag packaging machines, also known as jumbo bag fillers or bulk bag fillers, are specifically designed to tackle high-volume packaging of:
- Heavyweight Products: These machines excel at handling products with significant weight, often exceeding hundreds or even thousands of kilograms. Examples include fertilizers, chemicals, sand, gravel, and minerals.
- Bulky Products: Ton bag machines can efficiently package products that take up a large volume but may not necessarily be extremely heavy. Examples include plastic pellets, wood pellets, animal feed, and shredded materials.
Weight Capacity of Ton Bag Packaging Machines
The weight capacity of ton bag machines is truly impressive, typically exceeding 1000 kg (1 ton). Here’s a deeper look at this capacity:
- 1 Ton Minimum: As the name suggests, ton bag machines are designed to handle at least 1 ton (1000 kg) of material. This makes them ideal for applications where large quantities need to be packaged efficiently.
- Exceeding 1 Ton: Many ton bag machines can handle weights significantly exceeding 1 ton. The specific maximum capacity will vary depending on the model and its construction. Some industrial models can handle weights exceeding 2 tons or even 5 tons.
- Matching Bag Capacity: Ton bag machines are designed to work in conjunction with specific sizes of ton bags, also known as jumbo bags. These bags typically have capacities ranging from 500 kg to 2000 kg, ensuring compatibility with the machine’s weight capabilities.
Factors Affecting Ton Bag Packaging Machines Weight Capacity
- Machine Construction: The overall strength and design of the machine play a crucial role in determining the weight it can handle.
- Filling System: The type of filling system used, such as auger feeders or gravity flow systems, can influence the maximum weight that can be handled efficiently.
- Bag Material and Size: The weight capacity of the ton bag itself needs to be compatible with the machine’s capabilities to ensure safe and proper operation.
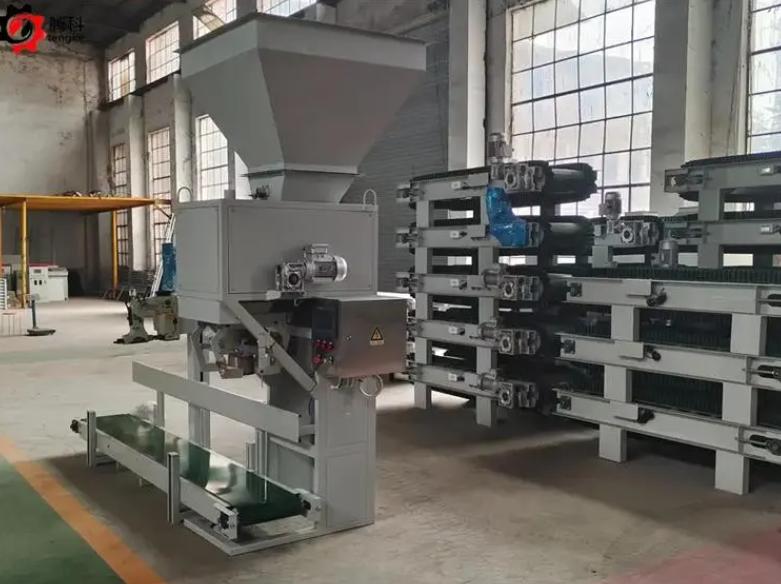
Double Spiral Feeding Hopper Less Packaging Machines
Double Spiral Advantage
- Improved Filling Efficiency: The double spiral design creates a more consistent flow of product, minimizing product channeling and ensuring each bag receives the accurate amount of material. This translates to faster filling speeds and reduced product waste.
- Reduced Product Segregation: Segregation occurs when different components of a mix separate during the filling process. The double spiral design helps maintain a uniform mix by gently blending the product as it travels down the spirals. This is particularly important for products with varying particle sizes or densities, ensuring consistent quality in each package.
Hopper-Less Design Benefits
- Minimized Material Hold-up: Traditional hoppers can have product residue accumulate within them. This can lead to inconsistencies in the filling process and potential product degradation over time. The hopper-less design eliminates this issue, ensuring a fresher product and more consistent filling.
- Simplified Cleaning: Cleaning a traditional hopper can be time-consuming and require dismantling parts. The hopper-less design removes this complexity. Cleaning becomes a quicker and easier process, minimizing downtime and promoting good hygiene practices.
Suitable Products for Double Spiral Feeding Hopper Less Packaging Machines
Double spiral feeding hopper-less packaging machines are ideal for dry products with good flowability. Here’s a breakdown of suitable product types:
- Powders: This includes products like flour, spices, coffee powder, cocoa powder, and detergents. The double spiral design ensures these fine materials flow smoothly and consistently.
- Flakes: Products like breakfast cereal flakes, potato flakes, and pet food flakes benefit from the gentle mixing action of the double spirals, preventing breakage and maintaining product integrity.
- Other Dry Products: This category can include items like dehydrated vegetables, small pasta shapes, and certain types of granular products with good flow properties.
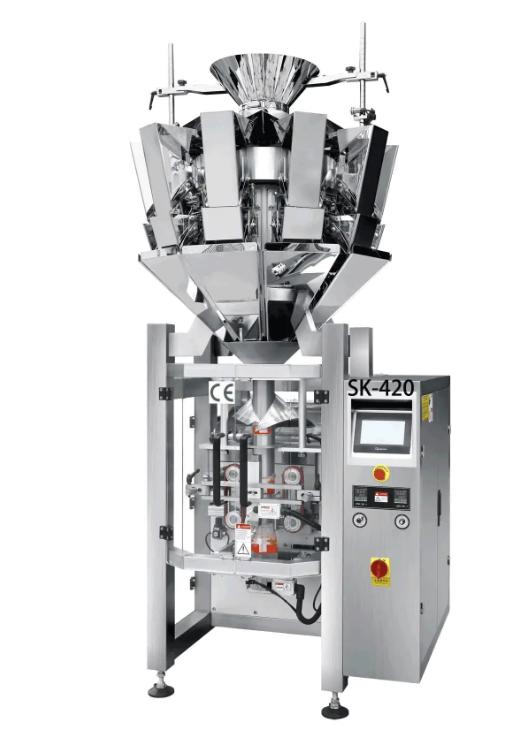
15L Small Bag Powder Packaging Machines
Machine Capacity of 15L Small Bag Powder Packaging Machines
The 15L designation refers to the volumetric capacity of the machine, not necessarily the weight. Here’s a breakdown of what this means:
- 15 Liters: This translates to approximately 15,000 cubic centimeters (cm³). It indicates the maximum volume of powder the machine can handle in a single filling cycle.
- Weight Capacity Variation: Since different powders have varying densities, a 15L machine won’t always fill bags with exactly 15 kg of product. For example, a light powder like cocoa powder will fill a 15L bag to capacity with less weight compared to a denser powder like flour.
Suitable Powders for 15L Small Bag Powder Packaging Machines
15L small bag powder packaging machines are ideal for packaging a variety of powders with good flow properties. Here’s a closer look at suitable product types:
- Good Flowability: The machine excels at handling powders that move easily without clumping or sticking. This ensures accurate filling and minimizes product waste. Examples include spices, coffee powder, flour, cocoa powder, and some types of powdered detergents.
- Particle Size Considerations: While the machine can handle a range of particle sizes, powders with very large or irregular particles might require further investigation. In some cases, such powders may not flow smoothly through the filling mechanism, potentially impacting accuracy or causing blockages.
Tips for Choosing Powders
- Density: Consider the density of your powder to estimate the weight a 15L bag can hold. You can find the product’s density information from the supplier or through online resources.
- Flowability Testing: If unsure about your powder’s flow characteristics, conduct a simple flowability test. This can involve pouring the powder from a container and observing its movement. Smooth and consistent flow indicates good suitability for the machine.
- Consulting the Manufacturer: For specific recommendations, consult the machine manufacturer. They can provide guidance on the types of powders the machine can handle effectively based on their experience and technical specifications.
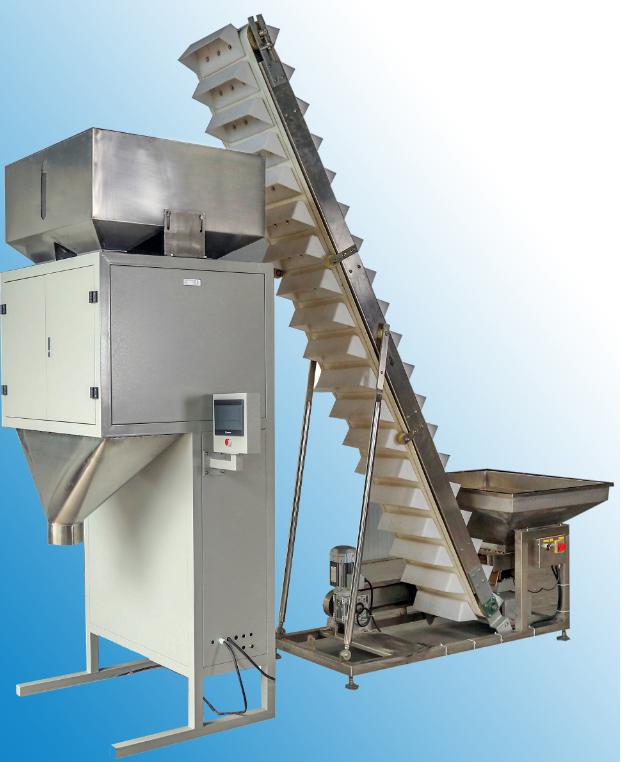
Conclusion
Kinds of packaging scales offer a diverse range of solutions for businesses with varying needs. You can make an informed decision and select the perfect fit for your product by understanding the functionalities and ideal applications of quantitative packaging machines, ton bag packaging machines, double spiral feeding hopperless packaging machines, and 15L small bag powder packaging machines. As a professional company on various scales, we will provide the products you want. Choosing efficient packaging from Bincen not only saves time and money but also ensures your products reach their destination safely and look their best.