Quantitative Belt Feeder Selection Guide
Quantitative belt feeders, also known as continuous weighing and feeding equipment, are vital across a vast array of industries. From the backbone of our energy infrastructure in coal mines and power plants to the foundation of manufacturing in steel, cement, and chemicals, Quantitative belt feeders play a crucial role in ensuring a consistent and accurate flow of materials. Their applications extend further, encompassing environmental protection, metallurgy, petrochemicals, food production, pharmaceuticals, and even the efficient operation of ports and terminals. Given the widespread use and critical function of quantitative feeders, selecting the right one for your specific needs is essential. Here at Chongqing Bincheng Mechanical and Electrical Technology Co., Ltd., we leverage our extensive experience and technical knowledge in industrial weighing to provide a comprehensive guide for choosing the optimal quantitative feeder.
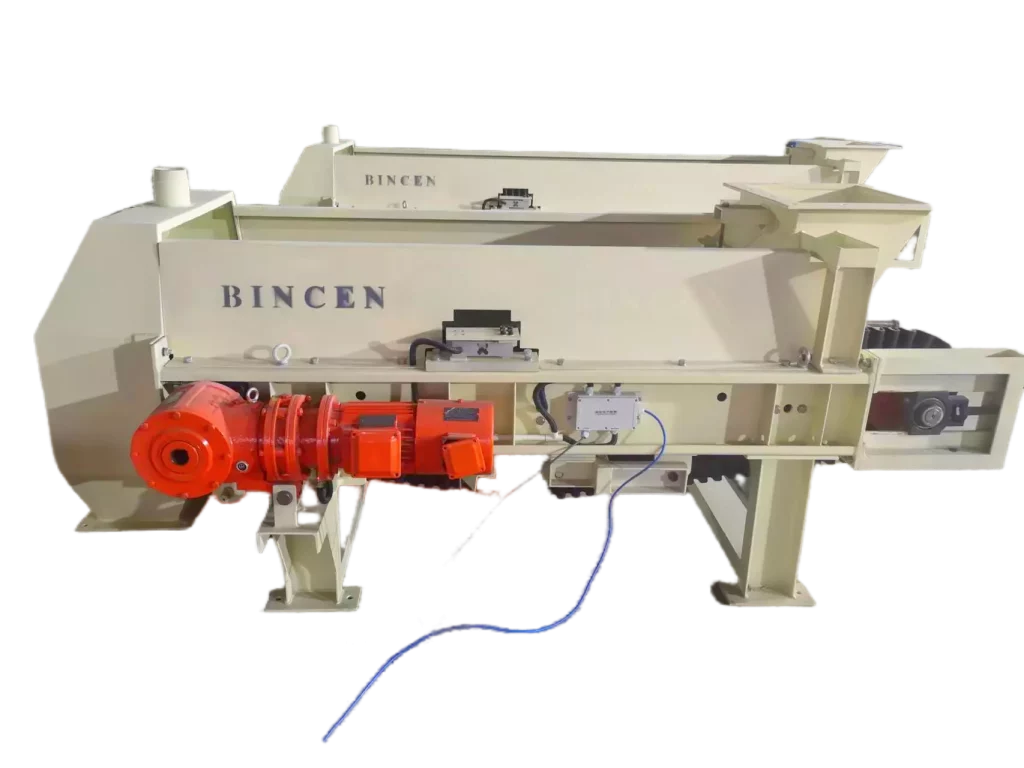
What Factors Influence Belt Quantitative Feeder Selection?
Unlike traditional feeders that rely on volume or time estimation, this innovative equipment utilizes a weighing system to ensure the material flow strictly adheres to the production process requirements. Choosing the right belt quantitative feeder for your specific needs requires careful consideration of several on-site factors. These factors are crucial for ensuring optimal performance and seamless integration into your existing operation. Here’s a breakdown of some key considerations:
- Material Properties: The physical characteristics of the material you’re handling, such as size, shape, abrasiveness, and moisture content, play a significant role in feeder selection.
- Operating Environment: Factors like temperature, dust levels, and potential for explosions need to be evaluated to ensure the feeder is suitable for the working conditions.
- Application Purpose: Whether you require continuous or batch feeding will influence the feeder’s design and functionality.
- Flow Setting: The target flow rate you need to achieve is a critical factor in determining the feeder’s capacity and control system.
- Superior Feeding Method: Existing methods of material delivery to the feeder need to be considered for compatibility and seamless integration.
- Structural Form and Size: The physical layout of your operation will dictate the size and configuration of the feeder to ensure proper space utilization and efficient material handling.
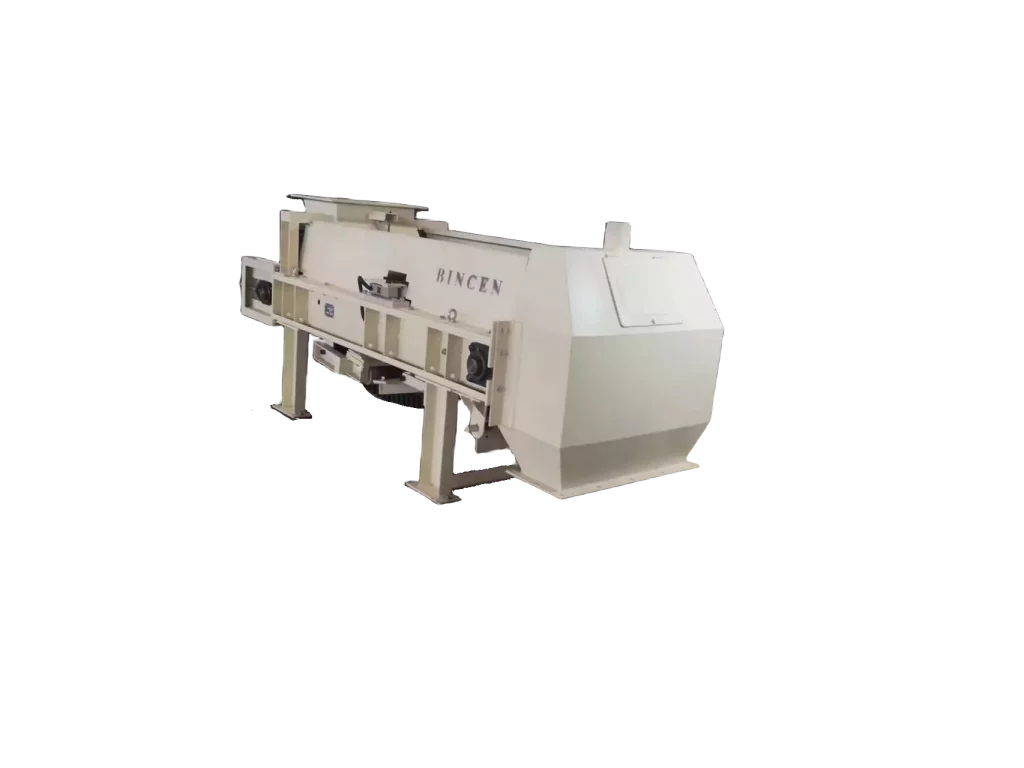
Specialized Quantitative Feeders for Unique Applications
- Taking the conventional series of quantitative belt feeders as an example, if it is a large-flow weighing feeder, you can choose a heavy-duty quantitative belt feeder. This feeder has significant advantages such as a large range and heavy load. The heavy-duty quantitative belt feeder adopts a dual-sensor direct weighing structure, which has a simple structure, low failure rate, and low maintenance;
- The medium-load quantitative belt feeder is suitable for materials ranging from medium to larger ranges, and is suitable for feeders with belt widths from 500mm to 1400mm and conveyor lengths of 1.5 meters or longer;
- Light-load quantitative belt feeder is designed to meet the industry needs of small flow rate and belt load. It has innovative and unique performance and can be used in places with high demand for accuracy;
- Double-belt quantitative belt feeder, the belt conveyor, and the metering belt conveyor are completely separated. The upper belt is responsible for pre-feeding and the lower belt is responsible for weighing. The system will adjust the feeding rate of the feeding belt according to the measurement results, making the batching efficiency more efficient. high;
- The double-belt suspended quantitative belt feeder has an overall fully suspended metering structure and 4 high-precision weighing sensors, without the influence of remaining materials;
- The chain plate weighing feeder is specially designed for batching and measuring high-temperature materials during the transportation process in metallurgy, chemicals, cement, and other industries. It is suitable for measuring materials with high moisture, high temperature, high viscosity, high warehouse pressure, etc.;
- The tape chain plate scale is designed for sticky or high-temperature materials. It is suitable for limestone, clay, iron concentrate, and other materials that are difficult to remove or high-temperature and have high requirements for weighing accuracy…..
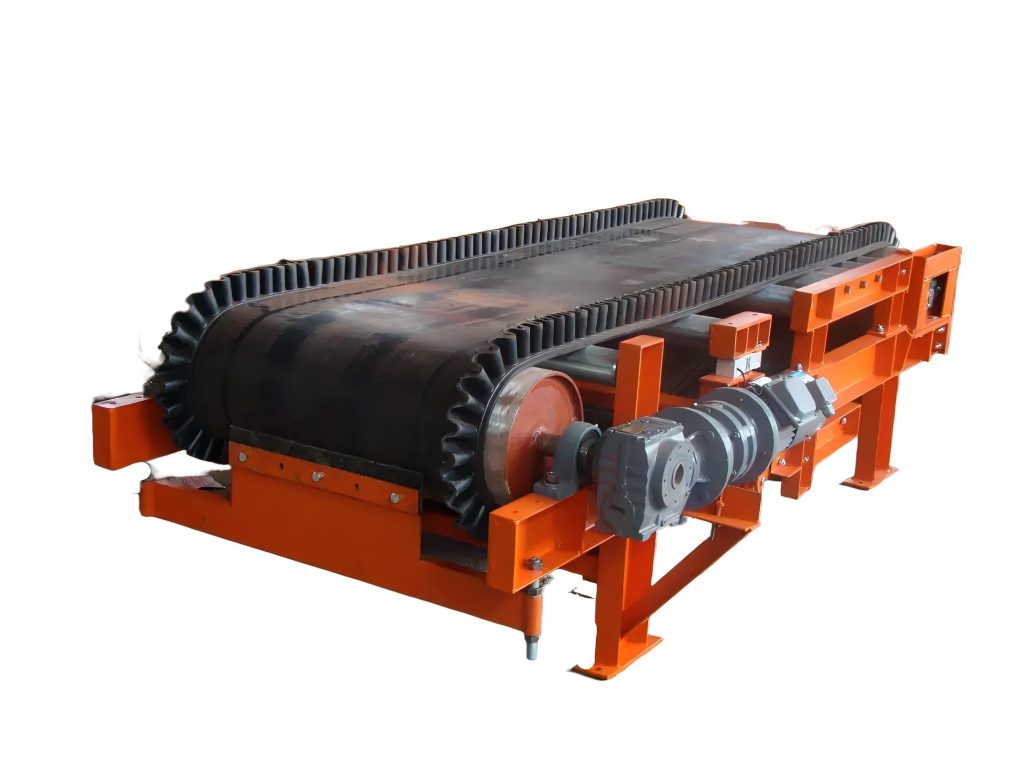
Conclusion
Quantitative belt feeders play a crucial role in controlling the precise flow of materials within your production process. The right feeder ensures you deliver the exact amount of material needed at each stage, leading to efficiency, reduced waste, and improved product quality. These feeders come in various configurations suited for different materials, environments, and applications. A selection guide helps you choose a feeder that can handle the specific material properties, operating conditions, and flow rates you require.
The series of quantitative belt feeders produced by Bincen is a new generation of series products developed and produced by industrial technology. They have the characteristics of high measurement and control precision and stable performance. The R&D team adopts corresponding structures and configurations according to the specific situations of quantitative feeding in the production of various enterprises and subversively solves the problems faced by many enterprises in quantitative feeding. As the series of quantitative feeders are widely used in various industries, not only gained a good market reputation but also won a large number of customers who came to visit and negotiate business. If you want to get more information about quantitative belt feeders, please contact us.