A Guide to Scale Solutions for Bulk Weighing
Weighing large quantities of materials presents unique challenges. Inconsistent material flow, environmental factors, and the sheer volume of material can introduce errors that can have significant repercussions. Accurate bulk weighing is not just a matter of convenience; it’s a critical factor in ensuring efficiency, safety, and profitability across diverse industries, from food processing to mining. This guide will explore a range of scale solutions designed to address these challenges, providing insights into the various technologies and considerations involved in selecting the most suitable weighing systems for your specific needs.
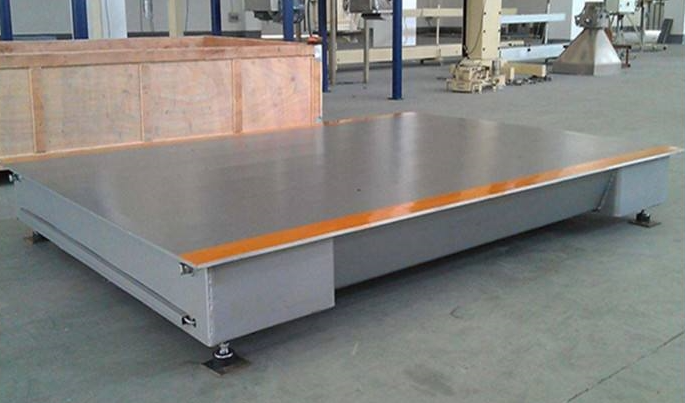
Types of Scale Solutions for Bulk Weighing
A. Floor Scales:
Platform Scales:
These are flat, sturdy platforms designed to weigh various items directly on their surface. They come in a wide range of sizes and capacities, from small benchtop models to large industrial platforms capable of handling heavy machinery. General-purpose weighing, inventory control, package weighing, industrial applications.
Advantages: Versatile, durable, available in various sizes and capacities.
Disadvantages: Can be less accurate for very precise weighing applications.
Bench Scales:
These are compact floor scales typically used for smaller weighing tasks, often found in laboratories, workshops, or retail settings. They are known for their portability and ease of use. Laboratory use, small-scale manufacturing, retail weighing, educational settings.
Advantages: Portable, easy to use, relatively inexpensive.
Disadvantages: Limited weight capacity compared to larger floor scales.
Heavy-Duty Floor Scales:
These are robust scales designed to withstand high loads and frequent use in demanding environments. They are commonly used in warehouses, shipping yards, and manufacturing facilities to weigh pallets, drums, and other heavy items. Warehouse weighing, shipping and logistics, industrial manufacturing, agriculture.
Advantages: High capacity, robust construction, suitable for harsh environments.
Disadvantages: Can be more expensive and less portable than other types.
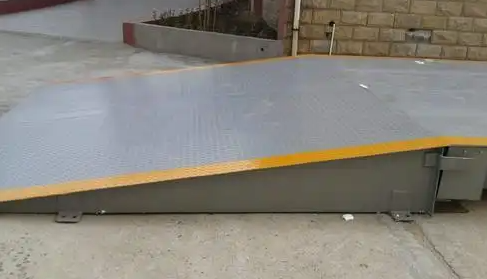
B. Hopper Scales:
Hopper scales are designed to weigh materials held within a hopper, which is a funnel-shaped container. They typically employ load cells, which are highly sensitive transducers that measure the force exerted by the weight of the material on the hopper. As material is added to the hopper, the load cells detect the increasing weight and transmit this information to a digital display or a connected control system.
Advantages of Hopper Scales:
- High accuracy: Load cell technology enables precise weight measurements, minimizing errors associated with manual weighing.
- Automation potential: Hopper scales can be easily integrated into automated systems for batching, blending, and dispensing operations.
- Improved efficiency: Automation reduces labor costs and increases throughput by streamlining weighing processes.
- Versatility: Suitable for a wide range of materials, from powders and granules to liquids and pastes.
Disadvantages of Hopper Scales:
- Cost: Hopper scales can be more expensive than simpler weighing solutions like platform scales.
- Complexity: Installation and maintenance may require specialized expertise.
- Space requirements: Hoppers can occupy significant floor space, especially for large-scale operations.
Applications of Hopper Scales:
- Batching: Accurately weighing and combining multiple ingredients for various formulations (e.g., food, pharmaceuticals, chemicals).
- Blending: Ensuring consistent material composition by accurately weighing and mixing components.
- Dispensing: Precisely dispensing materials into containers or onto conveyors.
- Process control: Monitoring and controlling material flow within production lines.
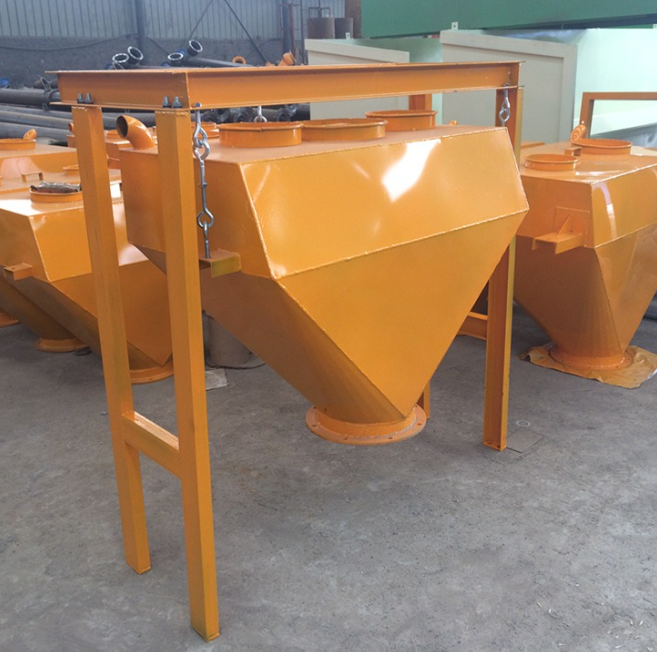
C. Conveyor Scales:
Types of conveyor scales:
- Belt Scales: These are commonly used for continuous weighing of bulk materials moving along a conveyor belt. They typically utilize load cells to measure the weight of material passing over the belt.
- Weigh-in-Motion Scales: These advanced systems are designed to weigh vehicles (trucks, trains) while they are in motion. They use specialized sensors embedded in the roadway to determine the weight of passing vehicles.
Advantages of conveyor scales:
- Continuous weighing: Belt scales provide real-time data on material flow rates, enabling continuous monitoring and control of production processes.
- High throughput: Suitable for high-volume applications, allowing for efficient material handling.
- Automation potential: Easily integrated into automated systems for process control, inventory management, and billing.
- Data acquisition: Provides valuable data for optimizing production processes, improving efficiency, and reducing waste.
Disadvantages of conveyor scales:
- Potential for inaccuracies: Belt scales can be affected by factors such as belt slippage, material flow variations, and changes in belt tension.
- Maintenance requirements: Regular maintenance is crucial to ensure accurate weighing, including belt cleaning and calibration.
- Cost: Conveyor scales can be a significant investment, especially for large-scale installations.
Applications of conveyor scales:
- Bulk material handling: Widely used in mining, agriculture, and other industries for transporting and weighing materials such as coal, ore, grain, and sand.
- Production lines: Integrated into manufacturing processes for continuous monitoring and control of material flow.
- Inventory management: Tracking material flow in warehouses and distribution centers.
- Toll collection: Weighing vehicles for road toll purposes.
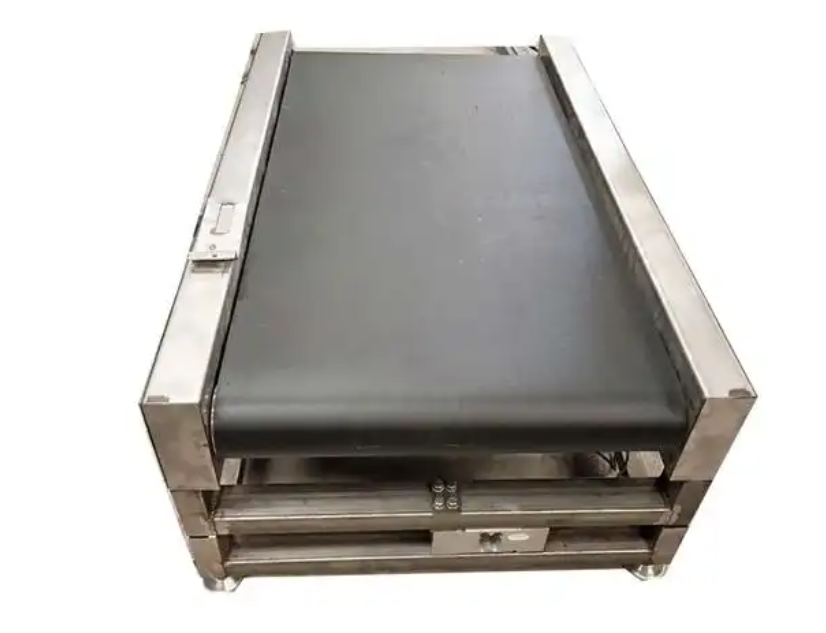
Factors to Consider When Choosing a Scale
A. Accuracy Requirements:
Legal for Trade applications demand the highest level of accuracy and require scales to be regularly calibrated and certified by relevant authorities.
Inventory control may require less stringent accuracy but still needs to be reliable to prevent stock discrepancies and associated financial losses.
Production processes may have specific accuracy requirements depending on the nature of the product and the tolerance levels for variations in ingredient amounts.
B. Capacity and Throughput:
Capacity: The scale must be able to handle the maximum weight of material that will be weighed. Underestimating capacity can lead to equipment failure and safety hazards.
Throughput: The desired weighing speed is crucial, especially in high-volume applications. Conveyor scales and automated systems are ideal for high-throughput operations.
C. Material Type:
Density variations can affect the accuracy of weight measurements.
Flowability can influence the design of hoppers and the effectiveness of conveyor systems.
Abrasiveness can wear down scale components, requiring more frequent maintenance.
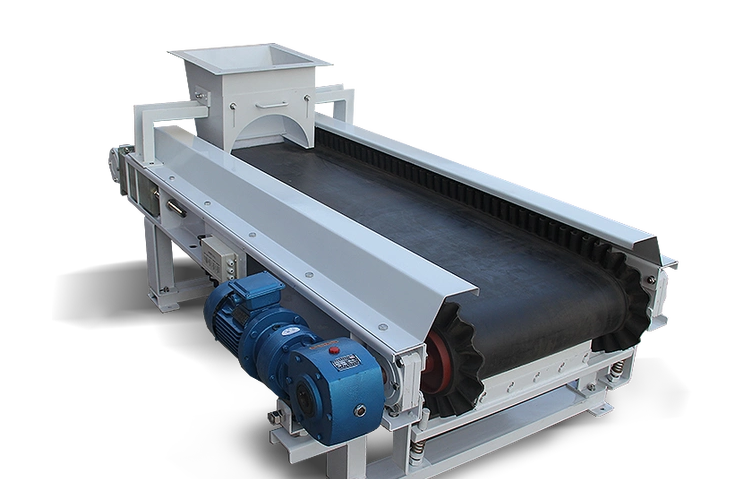
D. Environmental Conditions:
Extreme temperatures can affect the performance of electronic components and cause dimensional changes in the scale structure.
High humidity can lead to corrosion and electrical problems.
Exposure to harsh chemicals can damage the scale and compromise its accuracy.
E. Budget Constraints:
Evaluate the initial cost of the scale, including installation and any necessary modifications to the existing infrastructure.
Factor in ongoing maintenance costs, including calibration, repairs, and the cost of consumables.
F. Automation Needs:
Does the application require data integration with other systems, such as:
PLCs (Programmable Logic Controllers) for automated control of material flow and production processes?
ERP (Enterprise Resource Planning) software for inventory management, order tracking, and production planning?
Evaluate the available data communication options (e.g., RS-232, Ethernet, Wi-Fi) and the compatibility of the chosen scale with existing systems.
A Path to Weighing Success
Selecting and implementing the right bulk weighing solution requires careful planning and consideration. Working with experienced suppliers and regularly maintaining and calibrating your equipment are essential for ensuring long-term accuracy and maximizing your investment. By embracing advanced weighing technologies and implementing best practices, businesses can optimize their weighing processes, gain a competitive edge, and achieve sustainable success. determines their weight and other data. Additionally, weigh stations may be closed or out of service, allowing trucks to continue without stopping.