The Why and How of Calibrating Your Electronic Belt Scale
Precise measurement is crucial for efficient operations and accurate inventory management. Within the industrial landscape. Electronic belt scales play an important role in this process by continuously measuring the weight of bulk materials moving along conveyor belts. However, over time, a variety of factors can influence the accuracy of these scales. Here’s where calibration comes in. Bincen will explain what calibration is and why it is necessary for maintaining accurate weight measurements. We will also discuss frequency and assist you in determining the best calibration schedule for your specific requirements. Finally, we’ll discuss the various calibration methods available, allowing you to select the most appropriate approach for your application.
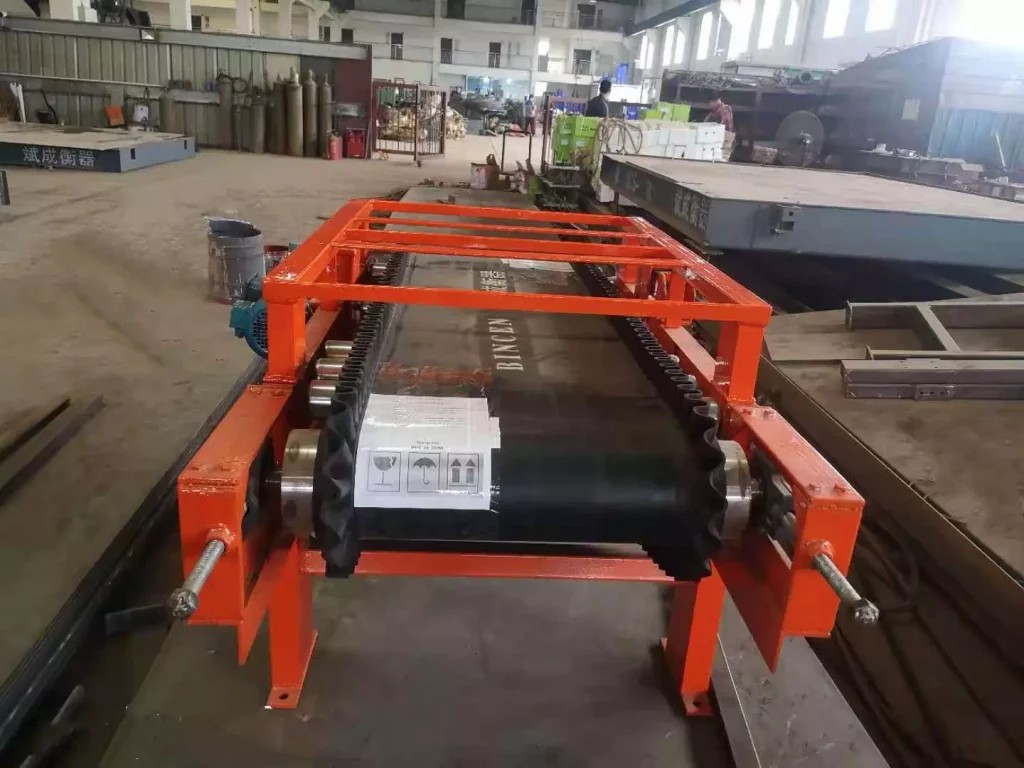
What Is Calibration and Why Is It Important for Electronic Belt Scales?
Calibration refers to the meticulous process of verifying and adjusting the accuracy of an electronic belt scale. It ensures that the scale’s weight readings accurately reflect the actual weight of material moving across the conveyor belt. Imagine a belt scale as a ruler. Temperature changes and frequent use may cause the ruler to warp slightly over time. Calibration is the process of checking a ruler against a known standard and making small adjustments to ensure that it continues to measure inches accurately.
Why Is Calibration Important?
- Accurate Inventory Management: Many industries require precise measurement of bulk materials for inventory control. Inaccurate belt scale readings can result in overpaying for materials or unintentionally running out of stock, affecting production and profit.
- Quality Control: Accurate weight data is frequently a critical component of quality control processes. For example, in food production, precise recipe adherence is dependent on accurate ingredient weighing. Inaccurate belt scale readings can result in inconsistent product quality.
- Billing and Customer Satisfaction: Accurate belt scale readings are crucial for maintaining customer trust and fair billing practices when selling materials by weight. Inaccurate readings can result in disputes and dissatisfied customers.
- Process Optimization: Real-time weight data from belt scales is crucial for optimizing production efficiency in various industrial processes. Inaccurate readings can result in inefficiencies and even equipment damage from improper material handling.
- Compliance with Regulations: Certain industries have regulations that require regular calibration of weighing instruments to ensure accuracy. Failure to comply may result in fines or even production shutdowns.
The Effects of Uncalibrated Scales
- Inaccurate weight readings: This can result in overpayment for materials, product inconsistencies, and billing errors.
- Loss of trust: When customers or stakeholders have doubts about the accuracy of weight measurements, trust and credibility can suffer.
- Process inefficiencies: Inaccurate data can result in suboptimal production processes, reducing output and potentially causing equipment failure.
- Regulatory non-compliance: Failure to maintain proper calibration can result in fines or even production stoppages.
Regular calibration serves as preventative maintenance, ensuring that your belt scale produces dependable and accurate data, which is the foundation for efficient and cost-effective operations.
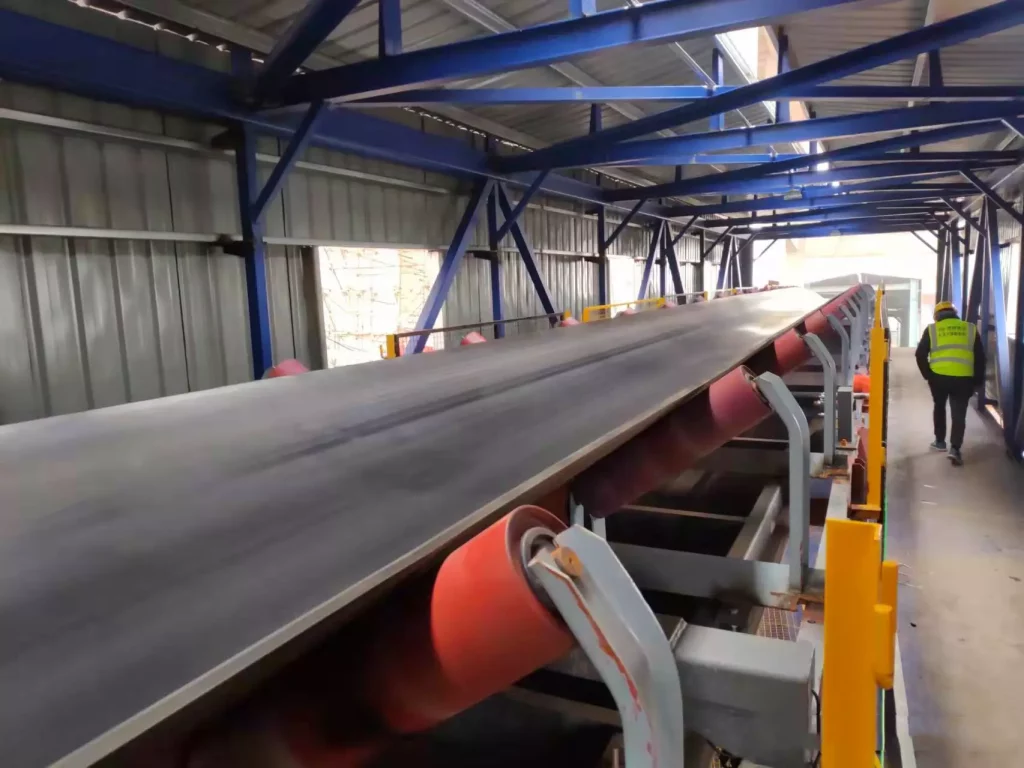
How Often Should I Calibrate My Electronic Belt Scale?
The ideal calibration frequency for your electronic belt scale is determined by a complex interplay of several variables. Here’s a breakdown to help you decide on the best schedule for your specific needs:
Factors Influencing Calibration Frequency
- Regulations: Certain industries, such as pharmaceuticals or food production, have specific regulations governing how frequently belt scales need calibration. These regulations are typically established by government agencies or industry standards organizations. Always check the applicable regulations for your industry to ensure compliance.
- Scale Usage: The frequency and intensity of use have a significant impact on calibration requirements. Here’s how usage comes in:
- Frequency: Continuous or long-term use of a scale may necessitate more frequent calibrations than sporadic use.
- Material: Heavy or abrasive materials can put more stress on the scale, requiring frequent adjustments.
- Accuracy Requirements: The level of precision required for your application has an impact. If your process requires extremely high accuracy (for example, weighing precious metals), you may require more frequent calibrations than less stringent applications (for example, coal transportation).
- Environmental Conditions: Temperature fluctuations, humidity levels, and even vibrations can all have an impact on the scale’s performance. If your scale is in a harsh or fluctuating environment, you should consider more frequent calibration.
- Scale History and Performance: If your scale has a history of calibration issues, or if you notice significant changes in its readings, it may indicate underlying problems that necessitate more frequent calibration until the problem is resolved.
General Recommendations
Always consult your scale’s manual for specific advice.
- Zero Calibration: A daily zero calibration is a commonly recommended procedure. This quick process ensures that the scale reads zero weight when no material is present. It aids in the detection of minor drifts while maintaining basic accuracy.
- Full Calibration: The frequency of full calibration, which entails running known weights across the belt, can vary greatly depending on the factors listed above. Here’s the general range:
- High Accuracy Needs (Monthly): If your application requires high precision, consider monthly full calibrations.
- Standard Applications (Quarterly): For the majority of industrial applications, quarterly full calibrations are a good starting point.
- Less Demanding Applications (Biannually or Annually): For less critical applications, biannual or annual full calibrations may suffice (depending on regulations and usage).
Additional Tips
- Consult your scale’s manual: The manufacturer’s manual will frequently make specific recommendations for calibration frequency based on the scale’s model and intended application.
- Consider a preventative maintenance program: Regular preventative maintenance can detect issues before they affect accuracy, potentially reducing the need for frequent calibrations.
- Track your calibrations: Keep a detailed record of all calibrations, including dates, weights, and any adjustments made. This record helps you track your scale’s performance over time and identify trends.
By carefully considering these factors and consulting your scale’s manual, you can determine a calibration frequency that ensures maximum accuracy for your electronic belt scale while minimizing downtime and costs. Remember that regular calibration is an investment that pays off in the form of consistent data, efficient operations, and, ultimately, a healthy bottom line.
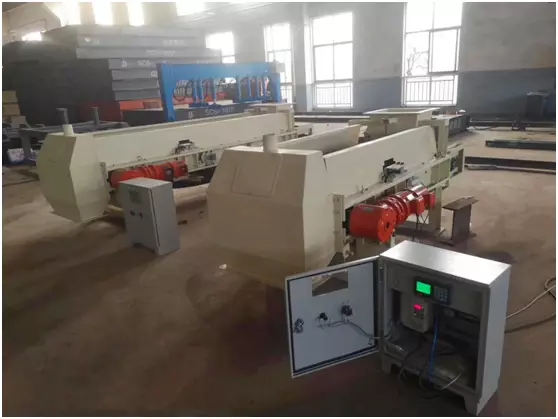
Are There Different Methods for Calibrating Electronic Belt Scales?
Two primary methods are commonly employed for calibrating electronic belt scales:
Electronic Calibration | Material Calibration | |
Method | Utilizes internal software adjustments within the scale’s electronics. | Involves running known test weights over the conveyor belt while it is operational. |
Advantages | Faster and more convenient Can be performed without interrupting material flow | Simulates real-world operating conditions Provides the highest level of accuracy |
Disadvantages | Less accurate than material calibration May not detect mechanical or system-wide issues | Requires stopping material flow More time-consuming and labor-intensive |
Suitability | Ideal for quick checks and minor adjustments Suitable for applications where interrupting material flow is not a major concern | Recommended for high-accuracy applications Essential when regulations mandate material calibration |
Additional Considerations
- Scale Type: Certain scale models may require specific calibration procedures or limitations. Always refer to the manufacturer’s manual for detailed instructions.
- Calibration Expertise: Material calibration often requires certified technicians with specialized equipment and expertise, unlike electronic calibration which can be performed by trained personnel.
The choice between electronic calibration and material calibration is determined by the specific application, accuracy requirements, and operational constraints. Electronic calibration is a useful tool for performing quick checks and minor adjustments. However, when high accuracy is required or regulations are in place, material calibration remains the gold standard. Regular calibration, regardless of method, is required to ensure the reliability and precision of electronic belt scales, protect product quality, optimize processes, and maintain regulatory compliance.
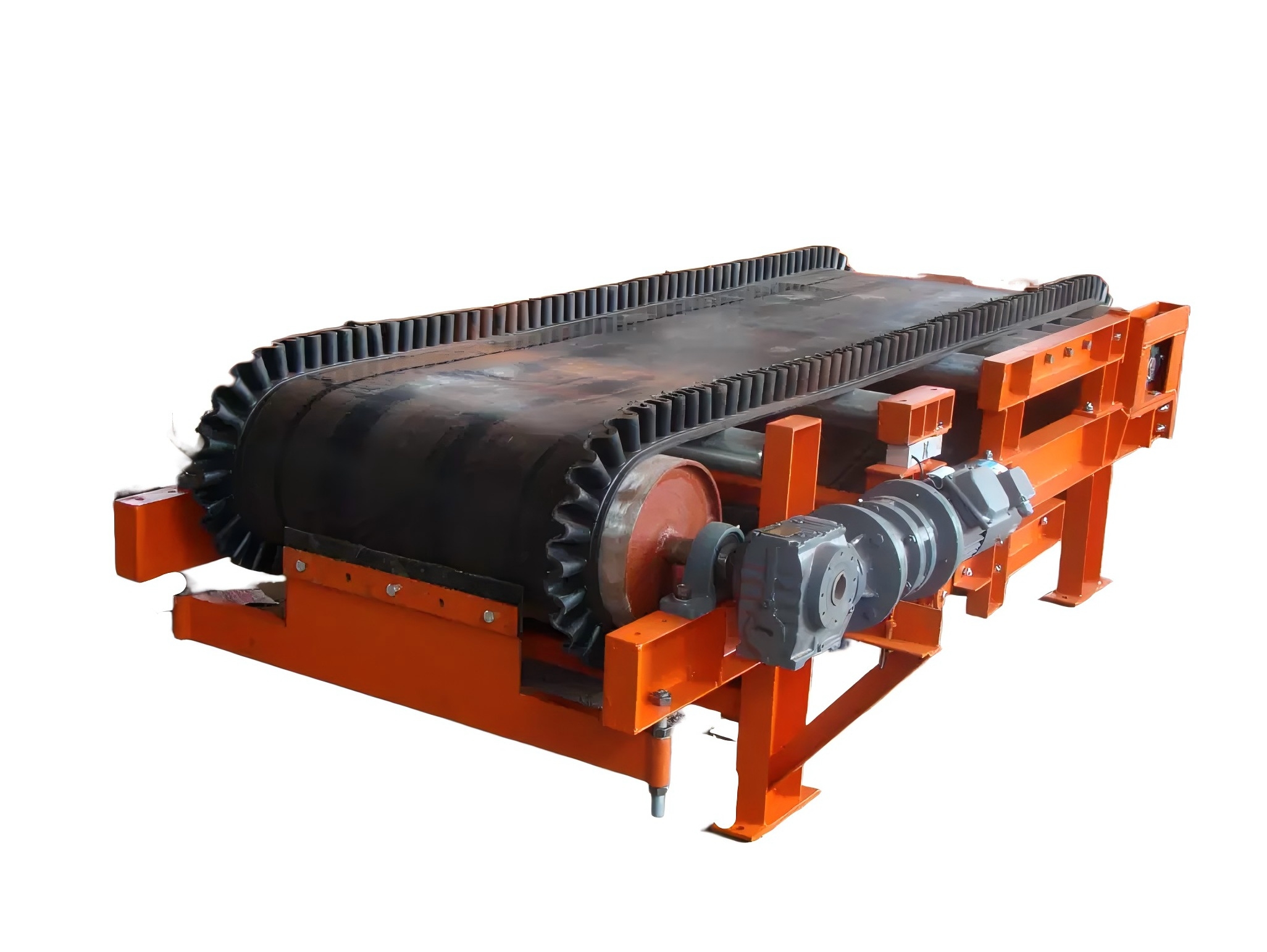
Conclusion
You can establish a robust calibration program for your electronic belt scales by understanding the importance of calibration and the factors that influence its frequency with Bincen, a China belt scale manufacturer. This ensures that they consistently deliver accurate data, which serves as the foundation for efficient material handling, optimal processing, and, eventually, a successful operation. The article examined the two main calibration methods, electronic and material calibration, and provided a clear understanding of their strengths and limitations. Remember that regular calibration is an investment that protects your bottom line and ensures an uninterrupted flow of accurate data in your industrial processes.