Why You Need a Batching Control System for Accurate and Efficient Batching
In today’s industrial landscape, consistency and efficiency are paramount. Whether you’re in the manufacturing, chemical, or food processing industry, when it comes to combining ingredients to create a final product, maintaining precise measurements and minimizing errors is crucial. This is where industrial batching control systems come into play.
What is a Batching Control System?
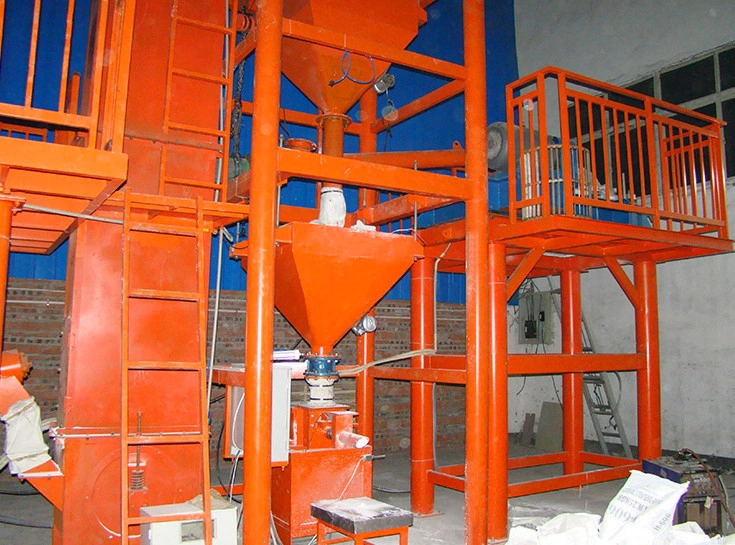
A batching control system is a comprehensive solution that integrates software, hardware, and instrumentation to automate and optimize the batching process.
At its core, a batching control system is designed to manage the precise measurement and dispensing of raw materials required for manufacturing processes. These systems are highly adaptable, capable of accommodating a wide range of industries.
The components of a batching control system typically include:
- Sensors: These devices play a crucial role in capturing real-time data related to the quantity, flow rate, and characteristics of raw materials. Sensors can include weight sensors, flow meters, level sensors, and temperature sensors, among others.
- Actuators: Actuators are responsible for controlling the flow of materials based on the instructions provided by the control system. These can include valves, pumps, conveyors, and other mechanical devices.
- Controllers: The heart of the batching control system, controllers process the data collected from sensors and issue commands to actuators to achieve the desired batching outcome. These controllers can range from simple programmable logic controllers (PLCs) to more sophisticated distributed control systems (DCS) or supervisory control and data acquisition (SCADA) systems.
- Software: Batching control systems rely on specialized software to facilitate programming, recipe management, data logging, and process visualization. This software allows operators to define batching recipes, set tolerances, and monitor the entire process in real-time.
- Human Machine Interface (HMI): HMIs provide operators with an intuitive interface to interact with the batching control system. Through HMI screens, operators can monitor process parameters, receive alerts, and make adjustments as needed.
The integration of these components enables batching control systems to automate complex batching processes with precision and repeatability. By eliminating manual intervention and human error, these systems ensure consistent product quality, reduce waste, and enhance operational efficiency. Furthermore, advancements in technology, such as cloud-based computing, machine learning, and IoT (Internet of Things) connectivity, are transforming batching control systems into intelligent platforms capable of predictive analytics, remote monitoring, and adaptive control strategies.
In essence, a batching control system serves as the cornerstone of modern industrial automation, empowering businesses to achieve unparalleled levels of accuracy, efficiency, and reliability in their batching operations. Whether it’s optimizing production processes, meeting regulatory requirements, or improving competitiveness, investing in a robust batching control system is a strategic imperative for forward-thinking organizations.
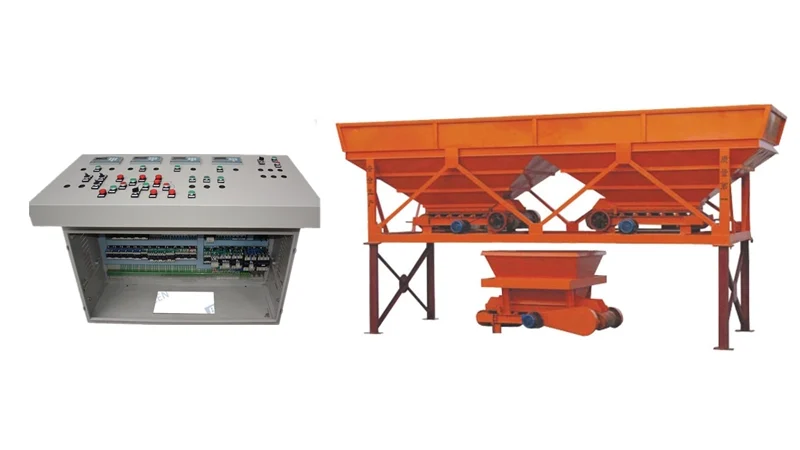
Importance of Accuracy in Batching
Maintaining precise measurements in industrial batching is not just about following a recipe; it’s the foundation for consistent, high-quality products. Even minor deviations from the intended ingredient ratios can have significant consequences throughout the production chain. Here’s a deeper dive into why accuracy in batching is paramount:
- Product Quality and Performance: In many industries, the final product’s effectiveness hinges on the precise combination of ingredients. For example, a slight under-measurement of a key component in a chemical formula could alter the final product’s properties, rendering it ineffective or even hazardous.
- Maintaining Brand Reputation: Consumers expect consistent quality from the brands they trust. Inaccurate batching can lead to variations in taste, texture, or performance, creating a negative brand experience and potentially damaging customer loyalty.
- Safety Concerns: Certain industries, like pharmaceuticals or food production, have strict regulations regarding ingredient ratios to ensure product safety. Inaccurate batching can introduce inconsistencies that violate these regulations, posing potential safety risks.
- Increased Costs: Inaccurate batching often leads to wasted materials. Overfilling containers or using incorrect amounts can force you to discard unusable products, impacting your bottom line. Additionally, inaccurate batches may require rework or even product recalls, further escalating costs.
By prioritizing accuracy in batching, you can ensure consistent product quality, maintain brand reputation, comply with safety regulations, and minimize waste, ultimately contributing to a more efficient and profitable operation.
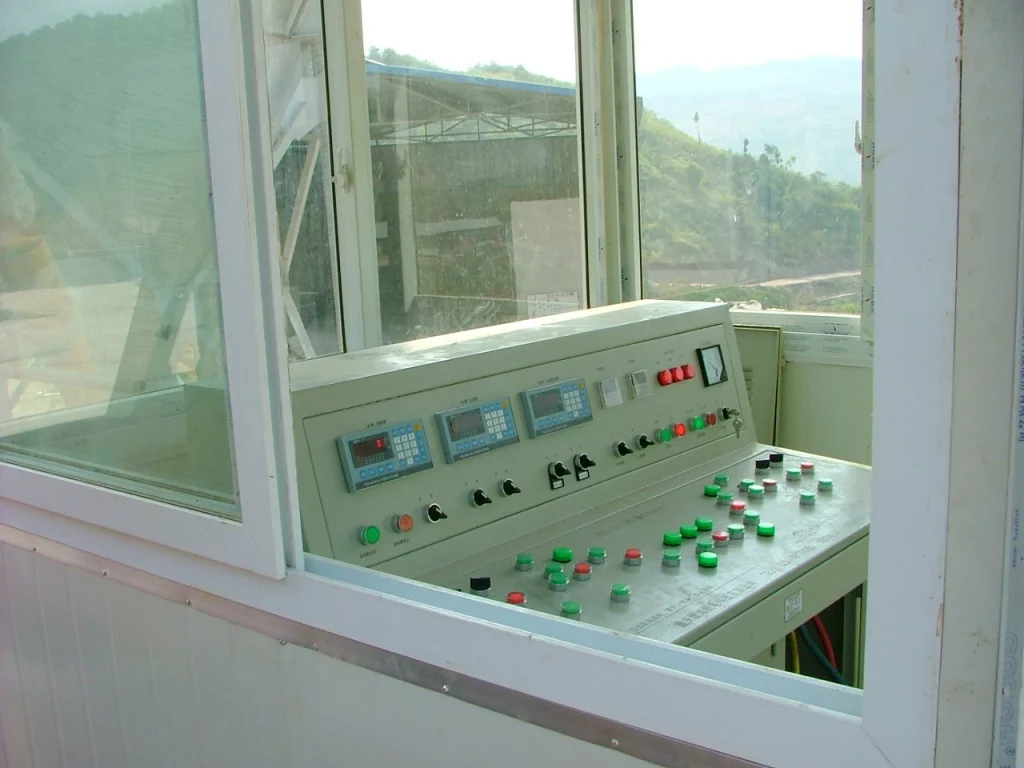
How Can You Benefit from Batching Control Systems
The industrial ingredient control system provides a comprehensive solution, not just ensuring precise measurement. These automation solutions have the potential to change the way you operate, significantly improving efficiency, reducing costs, and overall production management. By applying the ingredient control system, you can gain the following benefits:
- Improving accuracy and uniformity: Through automated weighing, feeding, and mixing processes, the ingredient control system eliminates the possibility of human errors. This allows for precise composition measurement of each batch of products, ensuring consistent product quality.
- Improving productivity and yield: Manual batching can be both labor-intensive and time-consuming. The ingredient control system can automatically execute repetitive tasks, shorten ingredient time, and increase yield. This enables you to meet higher demands and quickly fulfill orders.
- Better traceability and regulatory compliance: Modern ingredient control systems carefully record and document all batch-related data, including ingredient types, quantities, and timestamps. This comprehensive data tracking simplifies traceability and helps track the ingredients used in specific batches. Especially for industries with strict regulatory standards for ingredient ratios and procurement, this feature is extremely valuable for maintaining compliance.
- Reduce waste and improve cost efficiency: Accurate measurement can reduce spills and spills, thereby saving a large amount of raw materials. In addition, by using consistent ingredients, the risk of producing unusable or substandard products due to inaccurate proportions can be minimized. This will reduce product waste and have a positive impact on your financial bottom line.
- Simplified operations and scalability: A user-friendly interface and automated processes make batch operations easier to supervise and manage. Operators can quickly learn the operating system and reduce training needs. In addition, ingredient control systems are usually scalable, allowing you to easily expand production capacity as your business grows.
The investment ingredient control system is a strategic initiative that goes beyond simple task automation. It represents an investment in maintaining consistent product quality, improving efficiency, simplifying operations, and ultimately cultivating greater competitiveness and profitability.
Conclusion
By leveraging advanced automation and data-driven insights, batching control system enable businesses to achieve unparalleled levels of accuracy, efficiency, and quality assurance. Whether you’re looking to optimize production processes, meet regulatory requirements, or gain a competitive edge, investing in a batching control system is a strategic decision with far-reaching benefits.